XJ900RL Service Manual
XJ900RL Service ManualTable of Contents
Introduction
IntroductionNOTE:
The motorcycle you have purchased may differ slightly from those shown in the photographs.
FEATURES
ENGINE
The compact basic design is made possible by the re-siting of the alternator behind the crankshaft driven by a gear train, instead of simply positioned directly at the end of the shaft. Double overhead camshafts are driven by chain from the crankshaft, with an automatic chain tensioner reducing the need for maintenance.
The more normal two-valves per cylinder configuration is retained for ease of servicing and the fact that the valves can be operated directly by the camshafts without the added complication of cam followers. The camshafts are supported at four points for reliability at sustained high rpm. Carburetion of the XJ900RK is by four 34 mm constant vacuum units which, combined with the precise ignition timing of the electronically-governed T.C.I, unit, provides quick starting and smooth pick-up from any point in the rpm range. Coupled with this, the Yamaha Induction Control System (Y.I.C.S.) adds power in the low to mid-range and delivers about 10% increase in fuel efficiency. YICS is a secondary port cast into the cylinder head, linking the main induction tracts. It brings the secondary charge into the main tract at an angle so that it mixes with the main flow of fuel and the mixture is swirled completely around the combustion chamber, thus resulting in more complete cylinder filling which leads to more power and less fuel consumption.
Compact and powerful DOHC four.
CHASSIS/ELECTRICAL
The XJ900RK features a proven two-loop, full cradle chassis design. Shock absorbers, which are a new design, exclusive to Yamaha, have the unique feature that both the damping characteristics and the spring tension of the shock can be adjusted simultaneously by a single action.
The triple disc brakes on the XJ900RK owe much to technology developed for Grand Prix race. The disc caliper is of the opposed piston type, another development from the race tracks, and brake pads are semi-metallic. This improves wet weather performance, eliminates brake judder and cuts out the noise, squealing often found with asbestos components.
The new three-spoke type cast wheels are light but extremely rigid. Wider allow a flatter tyre profile for maximum cornering advantage. Tyres themselves are V-rated for the ultimate in safety at the highest cruising speeds. The 22 litre fuel tank blending smoothly into side panels and seat unit is very attractive, while at the same time helping greatly to provide the ultimate in rider comfort and protection.
A trim headlight fairing smooths out the area around the steering head and contains an aircraftstyle instrument panel with centrally-mounted tachometer, the speedometer on the left plus fuel gauge and digital clock on the right. The trip meter can be re-set at a single touch.
The forged alloy handlebars are adjustable to give the rider his most comfortable position. A louvred duct around the frame-mounting oil cooler directs a cooling air flow over the cylinder head. Continuing the "integrated" styling theme, the ribbed, alloy footrest mounting plates fill in the usually-untidy gap between side panels and the upswept mufflers. A cast alloy grab bar enhances passenger confidence while the contoured seat provides both comfort and a positive location.
Opposed piston type disc brake.
Adjustable handlebars.
Triple-meter console with digital clock.
Air-assisted fork with anti-dive system and fork brace.
Programmed rear suspension damping/preload adjustment.
Chapter 1. General Information
Chapter 1. General InformationMOTORCYCLE IDENTIFICATION
Frame serial number
The frame seria number is stamped into the right side of the steering head pipe.
Starting serial number: XJ900RL 33F-001101
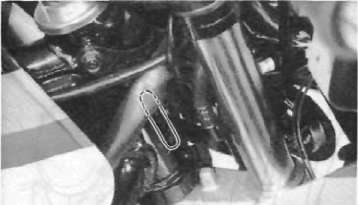
1. Frame serial number
Engine serial number
The engine serial number is stamped into the elevated part of the right rear section of the engine.
NOTE: The first three digits of these numbers are for model identifications; the remaining digits are the unit production number.
Starting serial number: 33F-001101
1. Engine serial number
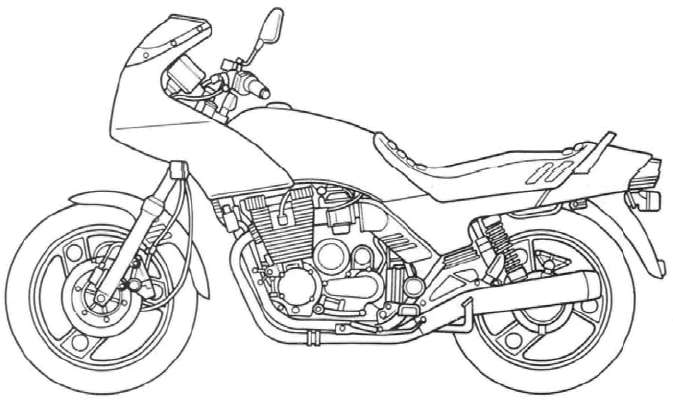
SPECIAL TOOLS
The proper special tools are necessary for complete and accurate tune-up and assembly. Using the correct special tool will help to prevent damage from improper tools or improvised techniques.
For tune-up
1. Compression gauge P/N. 90890-03081
2. Inductive timing light P/N. 90890-03109
3. Inducive tachometer P/N. 90890-03113
4. Fuel level gauge P/N. 90890-01312
5. Vacuum gauge P/N. 90890-03094
This gauge is needed for carburetor synchronization.
For engine service
1. Clutch holding tool P/N. 90890-04086
This tool is used to hold the clutch when removing or installing the clutch boss lock nut
2. Tappet adjusting tool P/N. 90890-01245
This tool is necessary to replace valve adjusting pads.
3. Valve guide reamer P/N. 90890-01227
This must be used when replacing the valve guide.
4. Valve seat cutter set P/N. YM-91043
This tool is needed to re-surface the valve seat.
5. Valve guide remover P/N. 90890-01225
This must be used to remove the valve guides.
6. Valve guide installer P/N. 90890-04017
This tool is needed for proper installation of the valve guides.
7. Valve spring compressor P/N. 90890-04019
This tool must be used for removing and installing the valve assemblies.
8. Piston ring compressor P/N. 90890-04044
This is used to compress piston rings when installing the cylinder.
9. Piston base
P/N. 90890-01067
Use 4 of these to hold the piston during cylinder installation.
10. Rotor puller
P/N. 90890-01080
This tool is needed to remove the A. C. generator
11. Rotor puller attachment P/N. 90890-04052
This tool is needed when removing the A. C. generator rotor together with the rotor puller.
12. Rotor holding tool P/N. 90890-04043
This tool is used to hold the A. C. generator rotor during removal and installation.
13. Piston pin puller P/N. 90890-01304
This tool is used to remove the piston pin.
14. Y. I. C. S. (Yamaha Induction control system) shut off tool P/N. 90890-04068
This tool is used to carburetor synchronization.
15. Plastigauge set "Green" P/N. YU-33210
This gauge is needed when measuring clearance for connecting rod bearing.
For chassis service
1. T-handle
P/N. 90890-01326 Damper rod holder P/N. 90890-01365
This tool is used to loosen and tighten the front fork cylinder holding bolt
2. Fork seal driver
P/N. 90890-01367
Fork seal driver attachment
P/N. 90890-01371
This tool used to reassemble the front fork.
For shaft drive service
1. Middle drive pinion holder P/N. 90890-04080
This tool is needed when measuring gear lash.
2. Middle and final gear holding tool P/N. 90890-01229
This tool is needed when measuring gear lasn.
3. Torx driver (# 40) P/N. 90890-04049
This tool is used to loosen or tighten the drive axle bearing stopper bolt
4. Dial gauge
P/N. 90890-03097
This too is used when measuring gear lash for middle and final gear.
5. Gear lash measurement tool (Final gear) P/N. 90890-01230
This tool is needed when measuring gear lash for final gear.
Chapter 2. Periodic Inspections
Chapter 2. Periodic InspectionsMaintenance Intervals
Maintenance IntervalsINTRODUCTION
This chapter includes all information necessary to perform recommend inspection and adjustments. These preventative maintenance procedures, if followed, will insure more reliable vehicle operation and a longer service life. The need for costly overhaul work will be greatly reduced. This information applies not only to vehicles already in service, but also to new vehicles that are being prepared for sale. Any service technician performing preparation work should be familiar with this entire chapter.
PERIODIC MAINTENANCE/LUBRICATION INTERVALS
ITEM |
REMARKS |
BREAK-IN 1,000 (600) |
EVERY |
|
6,000 (4,000) or 6 months |
12,000 (8,000) or 12 months |
|||
Valve clearance |
Check/Adjust valve clearance. |
0 |
||
Spark plug(s) |
Check/Clean or replace. |
O |
O |
Replace |
Air filter |
Clean. Replace every 24,000 (16,000). |
O |
O |
|
Carburetor |
Check/Adjust/idle speed, synchronization, starter operation. |
o |
O |
O |
Fuel line |
Check fuel hose and vacuum pipe for cracks or damage. |
O |
o |
|
Engine oil |
Replace (Warm engine before draining). |
o |
O |
o |
Engine oil filter |
Replace. |
o |
o |
|
Final gear oil |
Replace every 24,000 (16,000) or 24 months. |
o |
Check |
Check |
Brake |
Check operation/fluid leakage/See NOTE. |
O |
O |
|
Clutch |
Check operation |
O |
o |
|
Rear arm pivot bearings |
Check bearing assembly for looseness. Moderately repack every 24,000 (16,000) or 24 months. Use medium weight wheel bearing grease. |
Check |
||
Wheels |
Check balance/damage/runout. |
o |
O |
MAINTENANCE INTERVALS CHARTS
Proper periodic maintenance is important. Especially important are the maintenance services related to emissions control. These controls not only function to ensure cleaner air but are also vital to proper engine operation and maximum performance. In the following maintenance tables, the services related to emissions control are grouped separately.
ITEM |
REMARKS |
BREAK-IN 1,000 (600) |
EVERY |
|
6,000 (4,000) or 6 months |
12,000 (8,000) or 12 months |
|||
Wheel bearings |
Check bearings assembly for looseness/damage. Replace if damaged. |
O |
O |
|
Steering bearing |
Check bearings assembly for looseness. Moderately repack every 24,000 (16,000) or 24 months. Use medium weight wheel bearing grease. |
Check |
||
Front forks |
Check operation/oil leakage |
o |
O |
|
Rear shock absorber |
Check operation/oil leakage |
o |
o |
|
Fittings/Fasteners |
Check all chassis fittings and fasteners. |
o |
o |
o |
Batlery |
Check specific gravity. Check breather pipe for proper operation. |
o |
o |
|
A.C.Generator |
Replace generator brushes. |
o |
NOTE:
Brake fluid replacement:
1. When disassembling the master cylinder or caliper cylinder, replace the brake fluid. Normally check the brake fluid level and add the fluid as required.
2. On the inner parts of the master cylinder and caliper cylinder, replace the oil seals every two years.
3. Replace the brake hoses every four years, or if cracked or damaged.
Chassis Maintenance
Chassis MaintenanceBrakes
BrakesFront brake adjustment
The brake can be adjusted by simply adjusting the free play of the brake lever. The piston in the caliper moves forward as the brake pad wears out, automatically adjusting the clearance between the brake pads and brake disc.
CAUTION: Proper lever free play is essential to avoid excessive brake drag.
The free play at the end of the front brake lever should be 5 — 8 mm (0.2 — 0.3 in).
1. Loosen the lock nut.
2. Turn the adjuster so that the brake lever movement at the lever end is 5 - 8 mm (0.2 - 0.3 in) before the adjuster contacts the master cylinder piston.
3. After adjusting, tighten the lock nut
WARNING: Check the brake lever free play. Be sure the brake is working properly.
1 Adjuster 2. Lock nut a. 5 — 8 mm (0.2 — 0.3 in)
Rear brake pedal position adjustment
The brake pedal top end should be 27 - 33 mm (1.1 - 1.3 in) below the top of the footrest.
1. Remove the brake pedal pinch bolt and remove the brake pedal.
2. The punched mark on the brake pedal shaft and the punched mark on the brake pedal which must be aligned to install the brake pedal.
3. Install the brake pedal pinch bolt securely.
1. Pinch bolt 2 Punched marks a. 27 — 33 mm (1.1 —1.3 in)
Rear brake adjustment
The brake pedal free play is set at the factory. This free play ranges from where the brake pedal is trod to where the brake begins to take effect. No adjustment is necessary.
Free play: 20 - 30 mm (0.8 — 1.2 in)
a. 20 - 30 mm {0.8 -1.2 in)
Front and rear brake pad check
A wear indicator is attached to each brake pad to facilitate disc brake pad checks. This indicator permits a visual check without disassembling the pads. To check, look at the pad wear indicator in back of the caliper. If any pad is worn to the wear limit, replace both pads in the caliper.
FRONT
1. Wear indicator
REAR
1 Wear indicator
Inspecting the brake fluid level
Insufficient brake fluid may allow air to enter the brake system, possibly causing the brake to become ineffective. Check the brake fluid level and replenish when necessary observing these precautions:
FRONT
1. Lower level
REAR
1. Lower level
1. Use only the designated quality brake fluid; otherwise, the rubber seals may deteriorate, causing leakage and poor brake performance.
Recommended brake fluid: DOT #3
2. Refill with the same type and brand of brake fluid; mixing fluids may result in a harmful chemical reaction and lead to poor performance.
3. Be careful that water or other contamination does not enter the master cylinder when refilling. Water will significantly lower the boiling point and may result in vapor lock.
4. Brake fluid may erode painted surfaces or plastic parts. Always clean up spilled fluid immediately.
Brake fluid replacement
1. Complete fluid replacement should be done whenever the caliper cylinder or master cylinder is disassembled, or the fluid becomes seriously contaminated.
2. Replace the following components whenever damaged or leaking.
a. Replace all brake seals every two years.
b. Replace all brake hoses every four years.
c. Replace the plunger kits every two years.
Brake light switch adjustment
The brake light switch is operated by movement of the brake pedal. To adjust, hold the main body of the switch with your hand so it does not rotate and turn the adjusting nut. Proper adjustment is achieved when the brake light comes on just before the brake begins to take effect.
1. Main body 2. Adjusting nut
Clutch and Handlebars adjustment
Clutch and Handlebars adjustmentClutch adjustment
This model has two clutch cable length adjusters. The cable length adjusters are used to take up slack from cable stretch and to provide sufficient free play for proper clutch operation. Normally, once the clutch cable length adjuster (crankcase) is properly set; the only adjustment required is maintenance of free play at the clutch cable length adjuster (handlebar lever).
1. Loosen either the handlebar lever adjuster lock nut or the cable length adjuster lock nut.
2. Turn the cable length adjuster either in or out until proper lever free play is achieved.
Clutch lever free play: 2 —3 mm (0.08 —0.12 in)
1. Lock nut 2. Adjuster
1. Lock nut 2. Adjuster a. 2 - 3 mm (008 — 0.12 in)
Handlebars adjustment
1. Vertical adjustment
Five-stage adjustment is possible. a. Remove the cap and loosen the grip bar installation bolt.
1. Grip bar bolt
b. Loosen the grip bar and turn and align the adjusting collar either clockwise or counterclockwise. To adjust turn the collar counterclockwise to raise the grip ban turn the collar clockwise to lower the gip bar. (The red mark indicates the standard position.)
NOTE: Check to see that the projection on the handlebar fits a notch in the collar.
2. Horizontal adjustment
Four-stage adjustment is possible. a. Remove the cap and loosen the handlebar installation bolt.
1. Handlebar bolt
b. Loosen the handlebar and turn and align the adjusting collar either clockwise or counterclockwise. To adjust, turn the collar counterclockwise to move the handlebar inward, turn the collar clockwise to move the handlebar outward. (The red make indicates the standard position.)
NOTE: Check to see that the projection on the handlebar fits a notch in the collar.
Electrical
ElectricalELECTRICAL
Battery
1. The fluid level should be between the upper and lower level marks. Use only distillod water if refilling is necessary.
CAUTION: Normal tap water contains minerals which are harmful to a battery; therefore, refill only with distilled water.
2. Always make sure the connections are correct when installing the battery. Make sure the breather pipe is properly connected, properly routed, and is not damaged or obstructed.
CAUTION: The battery must be charged before using to insure maximum performance. Failure to properly charge the battery before first use, or low electrolyte level will cause premature failure of the battery. Charging current: 1.4 amps/10 hrs or until the specific gravity reaches 1.280 at 20°C (68°F)
WARNING: Battery electrolyte is poisonous and dangerous, causing severe burns, etc. It contains sulfuric acid. Avoid contact with skin, eyes or clothing.
Antidote: EXTERNAL-Flush with water. INTERNAL-Drink large quantities of water or milk. Follow with milk of magnesia, beaten egg, or vegetable oil. Call physician immediately.
Eyes: Flush with water for 15 minutes and get prompt medical attention. Batteries produce explosive gasive gases. Keep sparks, flame, cigarettes, etc. away. Ventilate when charging or using in closed space. Always shield eyes when working near batteries. KEEP OUT OF REACH OF CHILDREN.
Spark plug
1. Check the electrode condition and wear, insulator color and electrode gap.
2. Use a wire gauge for measuring the plug gap.
3. If the electrodes become too worn, replace the spark plug.
4. When installing the plug, always clean the gasket surface. Wipe off any grime that might be present on the surface of the spark plug, and torque the spark plug properly.
Standard spark plug:
BPR8ES (NGK) Spark plug gap:
0.7 - 0.8 mm (0.028 ~ 0.032 in) Spark plug tightening torque:
20 Nm (2.0 mkg, 14 fMb)
Replacing the headlight bulb
This motorcycle is equipped with a quartz bulb headlight. If the headlight bulb burns out, replace the bulb as follows: 1. Remove the 2 screws holding the light unit assembly to the headlight body.
2. Disconnect the leads, and remove the light unit assembly.
3. Turn the bulb holder couterclockwise and remove the defective bulb.
WARNING: Keep flammable products or your hands away from the bulb while it is on, it will be hot. Do not touch the bulb until it cools down.
4. Slip a new bulb into position and secure it in place with the bulb holder.
CAUTION: Avoid touching the glass part of the bulb. Keep it free from oil; otherwise, the transparency of the glass, life of the bulb, and illuminous flux will be adversely affected. If oil gets on the bulb, throughly clean it with a cloth moistened with alcohol or lacquer thinner.
1. Don't touch
5. Reinstall the light unit assembly to the headlight body. Adjust the headlight beam if necessary.
Headlight beam adjustment
1. Horizontal adjustment:
To adjust the beam to the left, turn the adjusting screw clockwise. To adjust the beam to the right turn the screw counterclockwise.
2. Vertical adjustment:
To raise the beam, turn the adjusting screw clockwise.
To lower the beam, turn the screw counterclockwise.
1. Horizontal adjusting screw 2. Vertical adjusting screw
Fuse replacement
1. The fuse block is located under the seat.
2. If any fuse is blown, turn off the ignition switch and the switch in the circuit in question, install a new fuse of proper amperage.
Turn on the switches, and see if the electrical device operates. If the fuse immediately blows again, find the cause in the circuit in question.
1. Main fuse 2. Spare fuse
WARNING: Do not use fuses of a higher amperage rating than those recommended. Substitution of a fuse of improper rating can cause extensive electrical system damage and possible fire.
Generator brushes replacement
The generator carbon brushes require periodical replacement.
1. Remove the generator cover screws and the left side generator cover.
2. Remove the screws and separate the brushes assembly from the cover.
3. Remove the panhead screws and replace the old brushes to new ones.
Fuel Petcock
Fuel PetcockFuel petcock cleaning
1. Turn the fuel petcock lever to the "RES". Remove the fuel pipe from the fuel petcock.
2. Remove the seat, the fuel tank clamp, and the fuel-tank-retainer plate.
3. Lift the tank and remove the drain cover and clean it with solvent. If gasket is damaged, replace.
1. Drain cover
Fuel petcock disassembly
If the fuel petcock is leaking or excessively contaminated, it should be removed from the fuel tank and inspected.
1. Remove the fuel tank and position it so that fuel will not spill when the cock is removed.
2. Remove the petcock and inspect the filter screen. Replace the filter if seriously contaminated.
3. Remove the screws on front and rear of the petcock and remove the plate, gaskets, lever, and diaphragm.
4. Inspect all components and replace any that are damaged. If the diaphragm is in any way damaged, or the petcock body gasket surfaces scratched or corroded, the petcock assembly must be replaced. If there is abrasive damage to any component, the fuel tank must be drained and flushed.
5. Reassemble the petcock and install it on the fuel tank.
Other Lubrication points
Other Lubrication pointsCable inspection and lubrication
WARNING: Damage to the outer housing of the various cables, may cause corrosion and often free movement will be obstructed. An unsafe condition may result so replace such cables as soon as possible.
Lubricate the inner cable and cable end. If they do not operate smoothly, replace them.
Recommended lubricant: SAE 10W30 motor oil
Throttle cable and grip lubrication
The throttle twist grip assembly should be greased when the cable is lubricated, since the grip must be removed to get at the end of the throttle cable. Two screws clamp the throttle housing to the handlebar. Once these two are removed, the end of the cable can be held high to pour in several drops of lubricant. With the throttle grip disassembled, coat the metal surface of the grip assembly with a suitable all-purpose grease to cut down friction.
Rear arm pivot bearings
The swing arm must pivot freely on its bearings but not have any excess play. Check and adjust pivot bearings if necessary. (Refer to CHAPTER 5. SWING ARM).
Brake and change pedals/brake and clutch levers
Lubricate the pivoting parts of each lever and pedal.
Recommended lubricants: SAE 10W30 motor oil
Center and side stand pivots
Lubricate the center and side stands at their pivot points.
Recommended lubricants: SAE 10W30 motor oil
Steering Head Bearings
Steering Head BearingsSteering head adjustment
1. Raise the front end of the motorcycle so that there is no weight on the front wheel.
WARNING: Securely support the motorcycle so there is no danger of it falling over.
2. Grasp the bottom of the forks and gently rock the fork assembly backward and forward, checking for looseness in the steering assembly bearings.
3. If there is looseness in the steering head, loosen the steering fitting bolt
1. Steering fitting bolt 2. Steering fitting nut
4. Use steering nut wrench to loosen top steering fitting nut. The top nut serves as a lock nut.
1. Steering nut wrench
5. Tighten the lower steering fitting nut until the steering head is tight but does not bind when forks are turned.
6. Retighten the top steering fitting nut and steering fitting bolt.
7. Recheck steering adjustment to make sure there is no binding when the forks are moved from lock to lock. If necessary, repeat adjustment procedure.
Suspension
SuspensionFront fork oil change
WARNING.
1. Fork oil leakage can cause loss of stability and safe handling. Have any problem corrected before operating the motorcycle.
2. Securely support the motorcycle so there is no danger of it falling over.
1. Elevate the front wheel by placing a suitable stand under the engine.
2. Remove the rubber cap from the top of each fork.
3. Remove the air valve cap from the left fork.
4. Keep the valve open by pressing it for several seconds so that the air can be let out of the inner tube.
1. Air valve cap
5. Loosen the front fork pinch bolts and remove the cap bolts from the inner fork tubes.
1. Pinch bolt 2. Cap bolt
6. Place an open container under each drain hole. Remove the drain screw from each outer tube.
WARNING:
Do not let oil contact the disc brake components. If any oil should contact the brake components, it must be removed before the motorcycle is operated. Oil will cause diminished braking capacity and will damage the rubber components of the brake assembly.
1. Drain screw
7. After most of the oil has drained, slowly pump the forks up and down to remove any remaining oil.
8. Inspect the drain screw gasket. Replace if damaged. Reinstall the drain screws.
9. Pour the specified amout of oil into each the fork inner tube.
Front fork oil capacity (each fork): 286 cm3 (10.1 Imp oz, 9.67 US oz)
Recommended oil: SAE 5W type SE motor oil or equivalent
10. After filling, slowly pump the forks up and down to distribute the oil.
11. Inspect the O-ring on the cap bolt. Replace if damaged.
1. O-ring
12. Reinstall the cap bolt and tighten the pinch bolt.
Tightening torque: Cap bolt: 23 Nm (2.3 mkg, 17 ft-lb) Pinch bolt: 23 Nm (2.3 mkg, 17 ft lb)
13. Fill the fork with air using an air pump or pressurized air supply. Refer to "Front fork and rear shock absorber adjustment" for proper air pressure adjusting.
Maximum air pressure: 118 kPa (1.2 kg/cm2, 17.1 psi) Do not exceed this amount.
Since the right and left front forks are connected by one air hose, there is only one valve where the air pressure is measured and adjusted.
Front fork and rear shock absorber adjustment
Front fork:
1. Elevate the front wheel by placing the motorcycle on the centerstand.
NOTE: When checking and adjusting the air pressure, there should be no weight on the front end of the motorcycle.
2. Remove the valve cap from left fork.
3. Using the air check gauge, check and adjust the air pressure.
If the air pressure is increased, the suspension becomes stiffer and if decreased, it becomes softer.
1. Air gauge
To increase: Use an air pump or pressurized air supply To decrease: Release the air by pushing the valve.
NOTE:
An optional air check gauge is available. Please ask a nearby Yamaha dealer. P/No. 2X4-2811A-00.
Air pressure:
39.2 kPa (0.4 kg/cm2, 5.7 psi) Maximum air pressure:
118 kPa (1.2 kg/cm2, 17.1 psi) Minimum air pressure: Zero
CAUTION: Never exceed the maximum pressure, or oil seal damage may occur.
4. Install the valve cap securely.
Rear shock absorber:
The rear shock absorber of this model features a spring seat, which is a combined spring preload and damping adjuster. Normal adjustment can be made by turning this spring seat; whereas damping adjustment only can be made by the damping adjuster.
CAUTION: Before adjustment, make sure of the following:
1. Turn in the damping adjuster fully. Then turn it back until its red painted slit aligns with the pointer "▼" on the spring cover.
2. For alignment in the absence of the red paint, turn the damping adjuster 6 clicks back from the fully turned-in position.
1. Spring seat adjustment
To increase the preload, turn the spring seat clockwise. To decrease the preload, turn the spring seat counterclockwise.
NOTE: When adjusting, use the special wrench which is included in the owner's tool kit
Hard -------------------------------Soft | |
Mark |
|
1. Spring seat
2. Damping adjustment
To increase the damping, turn the adjuster clockwise. To decrease the damping, turn the adjuster counterclockwise.
Standard position:
6 clicks turns out (or red mark) Minimum 12 clicks turns out Maximum 1 clicks turn out
NOTE: Make adjustment in less than one full turn of the adjuster.
1. Damping adjuster
Recommended combinations of the front fork and the rear shock absorber settings.
Use this table as guidance to meet specific riding and motorcycle load conditions.
Front frok |
Rear shock absorber |
Loading condition |
|||||
Air pressure |
Spring seat |
Damping adjuster turns out |
Solo rider |
With passenger |
With accessory equipment |
With accessory equipments and passenger |
|
1 |
39.2 ~ 78.5 kPa (0.4 ~ 0.8 kg/cm2, 5.7 - 11.4 psi) |
|
6 |
O |
|||
2 |
39.2 ~ 78.5 kPa (0.4 ~~ 0.8 kg/cm2, 5.7 ~11.4 psi) |
|
4 |
0 |
|||
3 |
58.8 - 98.1 kPa (0.6 ~ 1.0 kg/cm2. 8.5 — 14.2 psi) |
|
4 |
O |
|||
4 |
78.5 — 118 kPa (0.8 ~ 1.2 kg/cm2, 11.4- 17.1 psi) |
|
3 |
O |
* Each numeral shows the damping value which can be set when the pointer is aligned with the individual slit in the spring seat. The damping adjuster may be further turned for a softer or a harder damping; in each of the above settings, it is recommended that the damping be adjusted by one (1) or two (2) clicks on the softer side and one (1) click on the harder side.
1 |
Air bleed screw |
2 |
Brake fluid |
3 |
Vaive |
4 |
Valve seat |
5 |
Adjusting bolt |
6 |
Fork oil |
7 |
Pilot hole |
1. Remove the rubber cap from the bottom of the anti-dive unit.
1. Rubber cap
2. Look at the head of the adjusting bolt through the slots in the bottom of the anti-dive unit. In the standard position, two lines will be visible on the adjusting bolt head. Consult the fork adjustment chart below to determine the proper setting.
3. To decrease the anti-dive effect turn the adjusting bolt clockwise until the first line appears level to the top of the machined slot(s).
CAUTION: When the first line appears in the machined slot(s), the adjusting bolt will bottom in the anti-dive unit and a resistance will be felt. Do not attempt to turn the adjusting bolt beyond this point or the anti-dive unit will be damaged.
4. To increase the anti-dive effect, turn the adjusting bolt counterclockwise.
5. Replace the rubber cap.
WARNING: The anti-dive settings must be the same on both anti-dive units. Hence, be sure to perform the above procedure on both anti-dive units.
Adjusting bolt position |
Loading condition |
||
Solo rider |
With accessory equipments or passenger |
Wigh accessory equipments and passenger |
|
1 |
O |
||
2 |
O |
O |
|
3 |
O |
O |
|
4 |
O |
Engine Maintenance
Engine MaintenanceCam chain, Ignition timing and Air filter
Cam chain, Ignition timing and Air filterCam chain adjustment
This model has been equipped with the automatic cam chain tensioner. No adjustment is necessary.
Ignition timing check
1. Ignition timing is checked with a timing light by observing the position of the stationary pointer and the marks stamped on the timing plate.
The timing plate is marked as follows: |
|
|
.. Firing range for No. 1 (L.H.) cylinder |
|
.. Top Dead Center for No. 1 (L.H.) and No. 4 (R.H.) cylinders |
2. Connect the timing light to No. 1 (L.H.) spark plug lead.
3. Start the engine and keep the engine speed as specified. Use a tachometer to check the engine speed.
Specified engine speed: 1,050 r/min
4. The stationary pointer should be within the limits of "["]" on the timing plate. If it exceeds the limits or does not steady, check the timing plate for tightness and/ or ignition system for damage. (See "CHAPTER 6. ELECTRICAL)
CAUTION:
Never bend the stationary pointer.
Air filter
1. Removal
a. Remove the seat.
b. Remove the left and right side covers.
c. Remove the tool box.
d. Lift and loosen the electric fitting housing box from the frame.
e. Remove the air filter case cover by removing the four screws.
f. Pull out the element.
1. Air filter element
2. Cleaning method
Tap the element lightly to remove most of the dust and dirt; then blow out the remaining dirt with compressed air from the inner surface of the element. If element is damaged, replace it.
3. Reassemble by reversing the removal procedure. Check whether the element is seated completely against the case.
4. The air filter element should be cleaned at the specified intervals.
CAUTION:
The engine should never be run without the air cleaner element installed; excessive piston and/or cylinder wear may result.
Idle mixture setting
The idle mixture is set at the factory by the use of special equipment. No attempt should be made by the dealer to change this adjustment
Carburettor Adjustments
Carburettor AdjustmentsCarburetor synchronization
The seat must be removed and the rear of the tank elevated to gain access to the vacuum connections and synchronizing screw.
NOTE:
The valve clearances must be set properly before synchronizing the carburetors.
NOTE:
The carburetors are numbered 1, 2, 3, and 4 from the left when viewed from astride the motorcycle.
1. Remove the vacuum pipe from the carburetor manifold (No. 3 cylinder) and turn the fuel cock to "PRI."
2. Remove the rubber caps from the No. 1, 2, and 4 carburetor manifolds.
1. Rubber cap
3. Remove either the left or right (but not both) blind plug at the end of the YICS (Yamaha Induction Control System) passage in the cylinder.
1 Blind plug
4. Insert the YICS shut-off tool (special tool) fully and flip the locking lever.
5. Connect each vacuum gauge hose to its proper carburetor.
1. Vacuum gauge
6. Start the engine and allow it to warm up for a few minutes. The warm-up is complete when the engine responds normally to the throttle opening.
7. Make sure the engine idle speed is 950 ~- 1,000 r/min. If it is not adjust the idle speed with the throttle stop screw.
NOTE:
With the YICS shut off tool fitted, the engine speed generally drops a little. Thus, continue with the following steps at an idle speed of 950 — 1,000 r/min.
8. Each gauge reading will indicate the same if the carburetors are synchronized. The No. 3 carburetor has no synchronizing screw, and the other carburetors are to be synchronized to it in order, one at a time. First, synchronize carburetor No. 1 to carburetor No. 2 by turning the No. 1 synchronizing screw until both gauges read the same.
Second, in the same way synchronize carburetor No. 4 to carburetor No. 3. Third, by adjusting No. 2 screw, watch No. 3 carburetor reading. No. 1 and No. 2 carburetors will both change to match No. 3 carburetor.
9. Remove the YICS shut-off tool and reinstall the blind plug.
Tightening torque:
22 Nm (2.2 mkg, 16 ft-lb)
10. Check the idle speed. Adjust if necessary.
Idle speed adjustment
NOTE:
Carburetors must be synchronized before setting the final idle speed. The idle speed adjustment is made by turning only one throttle stop screw.
1. The engine must be warmed up, before setting the idle speed.
2. Set the engine idle speed by turning the throttle stop screw in (to increase engine speed) or out (to decrease engine speed).
Standard idle speed: 1,100 r/min
1. Throttle stop screw
Engine Oil, Gear lube and Compression check
Engine Oil, Gear lube and Compression checkEngine oil level measurement
1. Place the motorcycle on its centerstand. Warm up the engine for several minutes.
NOTE:
Be sure the motorcycle is positioned straight up when checking the oil level; a slight tilt toward the side can produce false readings.
2. With the engine stopped, check the oil level through the level window located at the lower part of the right side crankcase cover.
NOTE:
Wait a few minutes until the oil level settles before checking.
1. Level window 2. Maximum mark 3. Minimum mark
3. The oil level should be between maximum level and minimum marks. If the level is lower, add sufficient oil to raise it to the proper level.
Engine oil and oil filter replacement
1. Start the engine and stop it after a few minutes of warm-up.
2. Place an oil pan under the engine and remove the oil filler cap.
3. Remove the drain plug and drain the oil.
4. Remove the #2 exhaust pipe.
5. Remove the oil filter bolt and filter element.
1. Drain plug
1. Oil filter cover
6. Reinstall the drain plug (make sure it is tight).
Drain plug torque: 43 Nm (4.3 m-kg, 31 ft lb)
7. Install the new oil filter element new CD-ring and filter cover; tighten the oil filter bolt.
Oil filter bolt torque:
15 Nm (1.5 m-kg, 11 ft-lb)
NOTE:
Make sure the O-ring is positioned properly.
8. Install the #2 exhaust pipe.
Tightening torque: 8 Nm (0.8 m-kg, 5.8 ft-lb)
9. Add oil through the oil filler hole.
Periodic oil change: |
2.5 L (2.2 Imp qt 2.6 US qt) |
With oil filter replacement: |
2.8 L (2.5 Imp qt, 3.0 US qt) |
Recommended oil: |
SAE 20W40 type SE motor oil SAE 10W30 type
|
CAUTION:
Take care not to allow foreign material to enter the crankcase.
10. After replacement of the engine oil, and/ or oil filter, be sure to check for oil leakage. The oil level indicator light should go off after the oil is filled.
CAUTION:
If the indicator light flickers or remains on, the oil level switch may be damaged. Refer to "CHAPTER 6" for corrective action.
Final gear oil level measurement
1. Place the motorcycle on a level place and place it on the centerstand. The engine should be cool (at atmospheric temperature).
2. Remove the oil filler cap and check the oil level whether it is to the hole brim. If it is not up to this level, replenish oil.
1. Final gear oil 2. Correct oil level
CAUTION:
Take care not to allow foreign material to enter the final gear case.
Final gear oil replacement
1. Place an oil pan under the final gear case.
2. Remove the final gear oil filler cap and the drain plug, and drain the oil.
1. Final gear drain plug
3. Reinstall and tighten the final gear drain plug.
4. Fill the gear case to the specified level.
Oil capacity:
Final gear case:
0.2 L (0.18 Imp qt, 0.21 US qt) Recommended oil:
SAE 80 API "GL-4" Hypoid gear oil If desired, an SAE 80W90 hypoid gear oil may be used for all conditions.
5. Reinstall the filler cap securely.
Compression pressure measurement
Insufficient compression pressure will result in performance loss and may indicate leaking valves or worn or damaged piston rings.
Procedure:
1. Make sure the valve clearance is correct
2. Warm up the engine 2—3 minutes. Stop the engine.
3. Remove the all spark plugs.
4. Install a compression check gauge.
5. Turn over the engine with the electric starter (make sure the battery is fully charged) with the throttle wide open until the pressure indicated on the gauge does not increase further.
Compression pressure (at sea level): Standard
981 kPa (10 kg/cm2, 142 psi) Minimum
785 kPa (8 kg/cm2, 114 psi) Maximum
1,177 kPa (12 kg/cm2, 171 psi)
WARNING:
When cranking the engine, ground the removal spark plug leads to prevent sparking.
1. Compression gauge
6. If the pressure is too low, squirt a few drops of oil into the cylinder being measured. Measure compression again. If there is a higher reading than before (without oil), the piston rings may be worn or damaged. If the pressure remains the same after measuring with the oil, either or both the rings and valves may be the cause.
7. Check each cylinder. Compression pressure should not vary more than 98.1 kPa (1 kg/cm2, 14 psi) from one cylinder to any other cylinder.
Valve Clearance Check
Valve Clearance CheckNOTE:
Valve clearance must be measured with the engine and at room temperature.
1. Remove the seat and remove the fuel tank holding clip and retainer.
1. Clip 2. Retainer
2. Remove the starter (CHOKE) wire and spark plug leads.
1. Starter (CHOKE) wire
3. Remove the cylinder head cover and left crankcase cover (pick-up base cover). Care should be taken to not scratch or damage the gasket sealing surfaces.
4. Turn the crankshaft with the nut on the left end of the crankshaft to turn the cams. The proper position of the cam when measuring the valve clearance is with the cam lobe directly opposite the valve lifter.
5. Insert a feeler gauge between the valve lifter and the camshaft base circle.
Intake valve clearance (cold): |
0.11 - 0.15 mm (0.0043 ~~ 0.0059 in) |
Exhaust valve clearance (cold): |
0.16 — 0.20 mm (0.0063 — 0.0079 in) |
Valve clearance adjustment
Valve clearance is adjusted by replacing the adjusting pad on the top of the valve lifter. Adjusting pads are available in 25 thicknesses ranging from No. 200 (2.00 mm) to No. 320 (3.20 mm) in steps of 0.05 mm. The thickness of each pad is marked on the pad face that contacts the valve lifter (not the cam). Adjustment of the valve clearance is accomplished as follows:
1. Determine valve clearance (feeler gauge measurement.)
2. Remove adjusting pad and note number.
3. Select proper pad from appropriate chart (intake or exhaust chart).
4. Install new pad andcheck installed clearance.
Pad selection procedure
1. Measure valve clearance. If clearance is incorrect record the measured amount of clearance. This must be measured carefully.
2. There is a slot in the valve lifter. This slot must be positioned opposite the blade of the tappet adjusting tool before the tools is installed.
3. Turn the cam until the lobe fully depresses the valve lifter and opens the valve. Install the tappet adjusting tool as shown to hold the lifter in this depressed position.
NOTE:
The tappet adjusting tool is fastened to the cylinder head securely using an alien screw. Make sure that the tool contacts the lifter only, and not the pad.
CAUTION:
If the cam lobe touches the tappet adjusting tool, the stress may fracture the cylinder head. DO NOT ALLOW THE CAM LOBE TO CONTACT THE TAPPET ADJUSTING TOOL.
1. Tappet adjusting tool
4. Carefully rotate the cam so that the pad can be removed. To avoid cam touching the adjusting tool, turn cams as follows: (view from left side of the motorcycle)
Intake: Carefully rotate CLOCKWISE. Exhaust: Carefully rotate COUNTERCLOCKWISE.
5. Remove the pad from the lifter. There is a slot in the lifter. Use a small screwdriver or other blade and tweezers or a magnetic rod to remove the pad. Note the number on the pad.
1 Adjusting pad
6 Proper pad selection is made as follows:
Chart lookup method:
Refer to the appropriate chart for exhaust or intake valves:
0.11 to 0.15mm required clearance (Intake side) chart
0.15 to 0.20mm required clearance (Exhaust side) chart
a. Find number of original (installed) pad number on chart. Read down on chart.
b. Find measured valve clearance (from step 1) on chart. Read across.
c. At the intersection of installed pad number (down) and measured clearance (across) is a new pad number.
EXAMPLE:
Intake valve, installed pad: No. 250 (read down)
Measured clearance:0.32 mm (read across)
New pad number: No. 270(intersection of down & across)
Alternate shim calculation method:
Since all shims come in .05mm (.002") increments, you can quickly calculate the required size without a chart.
If the measured clearance is within 0.05mm (0.002") of the required clearance, then no change is needed.
If the measured clearance greater than 0.05mm (0.002") but 0.10mm (0.004") or less different than the required clearance then the next size shim is required.
If the measured clearance greater than 0.10mm (0.004") but 0.15mm (0.006") or less different than the required clearance then the next size shim is required.
Clearances that are too small require thinner shims. Clearances that are too large require thicker shims.
Example: Required exhaust valve clearance is 0.16~0.20mm. Measured clearance is 0.12mm (gap too small). Installed shim is Y270. Required shim is one size thinner: Y265.
NOTE:
The new pad number is to be used as a guide only. Verify the correctness of this choice in the following step(s).
7. Install the new pad in the lifter. Install the pad with the number down.
8. Remove tappet adjusting tool.
9. Turn crankshaft to rotate cam several rotations. This will set the pad in the lifter.
10. Check valve clearance (step 3). If clearance is incorrect, repeat preceding steps until proper clearance is obtained.
11. Inspect head cover gasket. If bent or torn, replace gasket.
12. Reinstall removed parts in reverse order.
Chapter 3. Engine Overhauling
Chapter 3. Engine OverhaulingEngine Removal
Engine RemovalENGINE REMOVAL
NOTE: It is not necessary to remove the engine in order to remove the cylinder head, cylinder, or pistons.
Preparation for removal
1. All dirt, mud, dust and foreign material should be thoroughly removed from the exterior of the engine before removal and disassembly. This will help prevent any harmful foreign material from engine oil.
2. Before the engine removal and disassembly, be sure that you have the proper tools and cleaning equipment so that you can perform a clean and efficient job.
3. During disassembly of the engine, clean and place all of the parts in trays in order of disassembly. This will speed up assembly time and help insure correct reinstall-action of all the engine parts.
4. Place the motorcycle on its center stand. Start the engine and allow it to warm up. Stop the engine and drain the engine oil.
5. Remove the left and right side covers, and remove the left and right oil cooler covers.
Fuel tank
1. Turn the fuel cock to "ON".
2. Remove the seat and remove the fuel tank securing clamp and retainer. Lift the rear end of the fuel tank and disconnect the fuel pipe and vacuum pipe from the cock.
1. Clip 2. Retainer
3. Disconnect the fuel sender unit lead, and remove the fuel tank.
4. Disconnect all connectors from the electrical components holding plate. Remove the electrical components holding plate.
Brake pedal and exhaust pipes
1. Remove the rear brake pedal.
2. Remove the exhaust pipe holding nuts from the cylinder head.
3. Loosen the clamp bolts securing the exhaust pipes to the right and left mufflers. Remove the exhaust pipes.
2. Remove the starter motor lead from the starter relay and disconnect the relay leads from the wire harness.
4. Remove the bolts holding the muffler bracket to the crankcase.
Battery case
1. Remove the negative lead from the battery terminal then remove the positive lead. Remove the battery.
1. Starter motor lead 2. Starter relay
3. Remove the battery case holding bolts and disconnect the rectifier/regulator lead from the wire harness. Then, remove the battery case with the starter relay assembly and rectifier/regulator unit.
Air filter case
1. Remove the clamps holding the carburetors to theair filter case and intake maniholds. Remove the crankcase ventilation hose at the air filter case.
1 Crankcase ventilation hose
2. Remove the bolts holding the air filter case to the frame (upper)
3. Remove the tool box.
4. Remove the starter (CHOKE) and clutch cables from the carburetor assembly.
1 Starter (CHOKE) cable 2 Clutch cable
5. Pull the carburetor assembly to the rear.
6. Disconnect the throttle cable from the carburetor throttle lever and remove the carburetor assembly to the left.
1. Throttle cable
Wiring and cables
1. Disconnect the clutch cable at the crankcase side.
2. Remove the spark plug leads.
3. Disconnect the pick-up coil and A. C. G. lead couplers.
Position the disconnect leads so that they can be safely removed.
CAUTION: The A. C. G. lead, starter motor lead, and pick-up lead are clamped at the cross tube of the frame. Do not forget to remove this clamp before removing the engine.
Oil coolers
1. Remove the oil filter cover from the crankcase.
2. Remove the oil cooler spacer holding bolt and remove the spacer.
1. Oil cooler spacer
3. Remove the oil cooler hose bracket holding nut.
4. Remove the oil cooler holding bolts and clamp. Remove the oil cooler assembly.
Drive shaft joint
1. Remove the coil spring holding the rubber boot.
2. Pull the rubber boot from the drive shaft coupling to expose the joint bolts.
3. Remove the joint bolts on the drive shaft coupling.
Engine removal
1. Remove the front engine mounting bolts and nuts. Remove the brackets.
2. Remove the rear engine mounting bolts and right and left footrests.
3. Remove the muffler securing bolts and remove the mufflers.
4. Slide the engine forward slightly and remove the engine to the right
NOTE: Position a box or other support to the right side of the motorcycle for the assistance when removing the engine.
Engine Disassembly
Engine DisassemblyPickup coil, Shifter, Starter Motor, Generator, and Clutch
Pickup coil, Shifter, Starter Motor, Generator, and ClutchPick-up coil assembly
1. Remove the alien bolt that holds the timing plate.
2. Remove the pick-up coil securing screws and remove the pick-up coil assembly.
Shifter
1. Remove the change pedal.
2. Remove the left crankcase cover.
3. Remove the shift lever assembly and shift shaft assembly.
1. Shift lever assembly 2. Shift shaft assembly
4. Remove the middle gear case oil level maintaining plug.
1. Remove the starter motor securing bolts and remove the motor assembly.
2. Remove the generator cover and stator coil assembly.
3. Install the rotor holding tool (special tool) on the rotor as shown and remove the rotor holding bolt.
1 Rotor holding tool
4. Insert the holding tool as shown and insert the rotor puller adapter (special tool) into the rotor shaft and screw in the rotor puller (special tool). Remove the rotor.
1. Rotor puller adapter
1. Rotor puller
Clutch
1. Remove right crankcase cover.
2. Release the tension evenly on the 6 mm bolts and remove the clutch pressure plate and clutch springs.
3. Remove the friction plates and clutch plates.
4. Straighten the lock washer tab. Use the clutch boss holder (special tool) to hold the clutch boss and remove the lock nut and lock washer.
1. Clutch boss holder
5. Remove the clutch boss and spacer.
6. Screw in a suitable length of 6 mm bolt into the one of the threaded holes on the collar and pull out the collar and needle bearing from the primary driven gear.
1. Collar 2. Pull
7. Remove the primary driven gear assembly and oil pump drive sprocket
8. Remove the oil collector plate.
Oil pump, Middle gear, and Crankcase
Oil pump, Middle gear, and CrankcaseOil pump removal and disassembly
1. Remove the strainer cover. Note the wire harness clip position.
2. Remove the oil pump secruing bolts and remove the sprocket cover and oil pump assembly.
CAUTION: Do not attempt to remove the strainer screen as it is permanently fitted onto the pump housing. If the pump housing and/or any parts of the pump are damaged, the pump assembly must be replaced with a new one.
3. Remove the oil pump driven sprocket.
4. Remove the oil pump cover and rotor assembly.
5. Remove the pressure relief valve, spring and plunger.
Middle gear
1. Remove the middle driven gear housing holding bolts.
2. Remove the middle driven gear housing assembly and shims.
NOTE: If it is difficult to remove housing assembly, loosen the two crankcase bolts located near the middle driven gear housing.
3. Remove "TORX" screws holding the middle drive gear assembly.
4. Remove the bearing retainers.
Crankcase disassembly
1. Remove the upper crankcase bolts, starting the highest numbered bolt. Turn over the engine and remove the lower crankcase bolts.
CRANKCASE TIGHTENING SEQUENCE
LOWER CASE
UPPER CASE
Tightening Torque
8 mm bolt: 24 Nm (2.4 mkg, 17 ft-lb) O .... 6 mm bolt: 12 Nm (1.2 mkg. 8.7 ft-lb)
Separate the lower case from the engine. Use a soft rubber hammer to carefully separate the crankcase.
Upper crankcase
1. Remove the middle drive gear and damper assqmbly.
2. Remove the transmission main shaft assembly.
3. Remove the A. C. G. shaft cover.
4. Remove the oil spray nozzle.
5. Carefully remove the A. C. G. shaft from the gear.
6. Remove the gear from the chain.
7. Straighten the lock washer tab and remove the bolt securing the starter idle gear shaft. Remove the shaft and starter idle gear.
8. Remove the crankshaft.
Lower crankcase
1. Remove the dowel pin and "O-ring".
2. Remove the shift fork guide bar and shift forks. The shift forks are identified by numbers cast on their sides.
3. Remove the bolt securing the shift cam locating pin and remove the stopper plate and locating pin.
1. Shift cam locating pin 2. Neutral switch
4. Remove the neutral switch.
5. Pull out the shift cam.
6. Remove the driven shaft bearing cover holding screws and remove the bearing cover.
7. Remove the 5th wheel gear from the driven shaft and pull out the driven shaft assembly.
1. 5th wheel gear
Cylinder Head, Cylinder and Piston
Cylinder Head, Cylinder and PistonCylinder head and cylinder
1. Remove the cylinder head cover.
2. Remove the left crankcase cover (pickup coil cover).
3. Remove the cam chain tensioner.
4. Use a 19 mm wrench on the timing plate flats to rotate the crankshaft counterclockwise until the engine is at Top Dead Centre.
CAUTION: Never use an alien wrench to rotate the crankshaft. Always use the 19 mm flats provided on the timing plate to rotate this engine.
5. Remove the four cam sprocket bolts.
6. Slip each sprocket off its mounting boss on the cam.
CAUTION: From this point on, do not rotate the cam shaft or valve damage may occur. On this, it is not necessary to break the cam chain. However, it can be broken if so desired. It is easier to disassemble the engine without separating the chain.
7. Remove the cam chain guide.
1. Cam cham guide
8. Remove the cam caps. Note the location ofthe cam caps as shown. Directional arrows are cast on each cap and point toward the clutch side.
9. Fasten safety wire to the cam chain to prevent its falling into the crankcase cavity.
Slide the camshafts and sprockets from under the chain and remove the camshafts and sprockets.
10. Remove the front cam chain guide.
1. Front cam chain guide
11. Remove the spark plugs.
12. Remove the cylinder head bolts and nuts in the numerical order as shown. Start by loosening each nut 1/2 turn until all of the nuts are loose. Remove the cylinder head.
13. Remove the front cylinder holding nut and remove the cylinder assembly. It may be necessary to tap the cylinder lightly to loosen it from the base gasket.
14. Remove the rear cam chain guide by loosening the holding bolt.
1. Hoiding bolt 2 Rear cam chain guide
Cylinder head disassembly
1. Remove the valve lifters and pads. Be careful not to scratch the lifter bodies or lifter bores in the cylinder head. Be very careful to identify each lifters position so that it may be returned to its original place.
1 Valve lifter 2. Adjusting pad
2. Mount the valve spring compressor on the head and depress each valve spring. Take out the retainer and valve spring with tweezers.
1. Valve spring compressor
3. Remove valves.
NOTE: Deburr any deformed valve stem end. Use an oil stone to smooth the stem end. This will help prevent damage to the valve guide during valve removal.
DEBURR VALVE STEM
4. Use a small box to hold the parts and identify the original position of each lifter and valve. Be very careful not to mix the location of these components.
Piston
1. Make each piston to aid in reassembly.
2. Place a clean towel or rag into the cranckcase to keep circlips and material from falling into the engine.
3. Remove piston pin clips, piston pins, and pistons.
Engine Inspection and Repair
Engine Inspection and RepairCylinder, Head and Valves
Cylinder, Head and ValvesCylinder head cover
Place head cover on a surface plate. There should be no warpage. Correct by re-surfacing as follows:
Place # 400 or # 600 grit wet sandpaper on surface plate and re-surface head cover using a figure-eight sanding pattern. Rotate head cover several times to avoid removing too much material from one side.
Cylinder head
1. Using a rounded scraper, remove carbon deposits from combustion chamber. Take care to avoid damaging spark plug threads and valve seats. Do not use a sharp instrument. Avoid scratching the aluminum.
2. Check the cylinder head warpage with a straight edge as shown.
The warpage should not exceed the specified limit, it necessary resurface. If the warpage exceeds allowable limit, the cylinder head should be replaced with a new one.
Cylinder head warpage: less than 0.03 mm (0.0012 in) Allowable limit: 0.25 mm (0.010 in)
Valve, valve guide, and valve seat
1. Check the valve face and the stem end for wear. If the valve face and/or the stem end are pitted or worn, regrind the valve with a valve refacer. Replace the valve if any dimension exceeds the specifications in the illustration.
INTAKE/EXHAUST VALVE
2. Valve stem wear must be measured and then combined with valve guide measurements to guide clearance. This clearance must be within tolerances. If it exceeds the maximum limit, then replace either or both valve and guide, as necessary.
|
Valve Stem Clearance |
Maximum |
Intake |
0.010 —0.037 mm (0.0004 -0.0015 in) |
0.10 mm (0.004 in) |
Exhaust |
0.025 — 0.052 mm (0.0010 -0.0020 in) |
0.12 mm (0.005 in) |
3. Valve stem end
Inspect the end of the valve stem. If the end appears to be ''mushroomed" or has a larger diameter than the rest of the stem, the valve, valve guide, and oil seal should be replaced.
4. Turn valve on "V" blocks and measure the amount of stem runout with a dial gauge. If it exceeds the maximum limit, replace the valve.
Maximum valve stem runout: 0.03 mm (0.0012 in)
5. Valve guide and valve oil seal replacement
If oil leaks into the cylinder through a valve due to a worn valve guide, or if a valve is replaced, the valve guide should also be replaced.
NOTE: The valve oil seal should be replaced whenever a valve is removed or replaced.
a. Measure valve guide inside diameter with a small bore gauge. If it exceeds the limit replace with an oversize valve guide.
Guide diameter (I. D.): Limit: 7.10 mm (0.280 in)
b. To ease guide removal and reinstallation, and to maintain the correct interference fit heat the head to 100 °C (212°F). Use an oven to avoid any possibility of head warpage due to uneven heating.
c. Use the appropriate shouldered punch (special tool) to drive the old guide out and drive the new guide in.
NOTE: When a valve guide is replaced, the 0-ring should also be replaced.
1. Valve guide remover
1. Valve guide installer
d. After installing the valve guide, use the 7 mm reamer (special tool) to obtain the proper valve guide to valve stem clearance.
e. After installing the valve guide in the cylinder head, the valve seat must be recut. The valve should be lapped to the new seat.
6. Grinding the valve seat a. The valve seat is subject to severe wear. Whenever the valve is replaced or the valve face is re-surfaced (see CAUTION) the valve seat should be re-surfaced at a 45° angle. If a new valve guide has been installed the valve seat must be recut to guarantee complete sealing between the valve face and seat.
Remove just enough material to achieve a satisfactory seat.
CAUTION: If the vatve seat is obviously pitted or worn, it should be cleaned with a valve seat cutter. Use the 45° cutter, and when twisting the cutter, keep an even downward pressure to prevent chatter marks.
If cutting section "A" of the valve seat, use 30° cutter. If cutting section "B", use the 45° cutter. If cutting section "C", use 60° cutter. b. Measure valve seat width. Apply mechanic's bluing dye (such as Dykem) to the valve face and valve seat, apply a very small amount of fine grinding compound around the surface of the valve face insert the valve into position, and spin the valve quickly back and forth. Lift the valve, clean off all grinding compound, and check valve seat width. The valve seat and valve face will have removed bluing wherever they contacted each other. Measure the seat width with vernier calipers. It should measure approximately 0.9 — 1.1 mm (0.035 — 0.043 in). Also, the seat should be uniform in contact area. If valve seat width varies, or if pits still exist, further cutting will be necessary.
|
Standard Width |
Wear Limit |
Seat width |
0.9 —1.1 mm (0.035 -0.043 in) |
2.0 mm (0.080 in) |
c. If the valve seat is uniform around the perimeter of the valve face, but is too wide or not centered on the valve face, it must be altered. Use either the 30°, 45° or 60° cutters to correct the improper seat location in the manner described below:
1) If the valve face shows that the valve seat is centered on the valve face, but too wide, then lightly use both the 30° and the 60° cutters to reduce the seat width to 0.9 —1.1 mm (0.035 —0.043 in).
2) If the seat shows to be in the middle of the valve face, but too narrow, use the 45° cutter until the width equals 0.9 ~~ 1.1 mm (0.035 —0.043 in).
1. Valve seat cutter
3) If the seat is too narrow and right up near the valve margin, then first use the 30° cutter and then the 45° cutter to get the correct seat width.
4) If the seat is too narrow and down near the bottom edge of the valve face, then first use the 60° cutter and then the 45° cutter.
7. Lapping the valve/valve seat assembly
a. The valve/valve seat assembly should be lapped if neither the seat nor the valve face are severely worn.
b. Apply a small amount of coarse lapping compound to valve face. Insert the valve into the head. Rotate the valve until the valve and valve seat are evenly polished. Clean off the coarse compound, then follow the same procedure with fine compound.
Continue lapping until the valve face shows a complete and smooth surface all the way around. Clean off the compound material. Apply bluing dye to the valve face and seat and rotate the valve face for full seat contact which is indicated by a grey surface all around the valve face where the bluing has been urbbed away.
c. Valve leakage check
After all work has been on the valve and valve seat, and all head parts have been assembled, check for proper valve/valve seat sealing by pouring solvent into each of the intake ports, then the exhaust ports. There should be no leakage past the seat. If fluid leaks, disassemble and continue to lap with fine lapping compound. Clean all parts thoroughly, reassemble and check again with solvent. Repeat this procedure as often as necessary to obtain a satisfactory seal.
Valve spring and lifters
6 | Adjusting Pad |
10. |
Inner spring |
7 |
Valve Lifter |
11. |
Outer spring |
8. |
Valve Retainer | 12 | Oil Seal |
9 |
Spring Seat | 13. | Valve |
1. Checking the valve springs
a. This engine uses two springs of different sizes to prevent valve float or surging. The valve spring specifications show the basic value characteristics.
b. Even though the spring is constructed of durable spring steel, it gradually loses some of it's tension. This is evidenced by a gradual shortening of free length. Use a vernier caliper to measure spring free length. If the free length of any spring has decreased more than 2 mm (0.080 in) from its specification replace it
c. Another symptom of a fatigued spring is insufficient spring pressure when compressed. This can be checked using a valve spring compression rate gauge. Test each spring individually. Place it in the gauge and compress the spring first to the specified compressed length with the valve closed (all spring specifications can be found in the previous section, Valve spring), then to the length with the valve open. Note the poundage indicated on the scale at each setting. Use this procedure with the outer springs, then the inner springs.
NOTE: All valve springs must be installed with larger pitch upward as shown.
Valve Spring Specifications |
||
OUTER |
INNER |
|
Free length |
39.5 mm (1.555 in) |
35.9 mm (1.413 in) |
Installed length (valve closed) |
34.0 mm (1.339 in) |
31.0 mm (1.220 in) |
Installed pressure |
17.6 -20.6 kg (38.8 - 45.4 lb) |
8.1 -9.9 kg (17.9 -21.8 lb) |
Allowable tilt from vertical |
2.5° |
— |
2. Valve lifter a. Check each valve lifter for scratches or other damage. If the lifter is damaged in any way, the cylinder head surface in which it rides is probably also damaged. If the damage is severe, it may be necessary to replace both the lifter and the cylinder head.
NOTE: For proper valve lifter-to-head clearance, always install lifters on their original valves.
Camshafts, cam chain and cam sprockets
1. Camshaft
a. The cam lobe metal surface may have a blue discoloration due to excessive friction. The metal surface could also start to flake off or become pitted.
b. If any of the above wear conditions are readily visible, the camshaft should be replaced.
c. Even though the cam lobe surface appears to be in satisfactory condition, the lobes should be measured with a micrometer. Cam lobe wear can occur without scarring the surface. If this wear exceeds a pre-determined amount, valve timing and lift are affected. Replace the camshaft if wear exceeds the limits.
d. Install the camshaft on the cylinder head. Place a strip of Plastigage between camshaft and camshaft cap as illustrated (lengthwise along camshaft). Tighten the nuts with specified torque. Remove the camshaft cap and determine the clearance by measuring the width of the flattened Plastigage.
Cap nut tightening torque: 10 Nm (1.0 rrvkg, 7.2 ft lb)
NOTE: Do not turn camshaft when measuring clearance with plastigage.
Camshaft-to-cap clearance:
Standard: 0.020 — 0.054 mm
(0.0008 —0.0021 in) Maximum: 0.160 mm (0.006 in)
If the camshaft-to-cap clearance exceeds specification, measure camshaft bearing surface diameter.
Bearing surface diameter: Standard: 24.967 — 24.980 mm (0.9830 - 0.9835 in)
1) If the camshaft diameter is less than specification, causing excessive clearance, replace the camshaft.
2) If the camshaft is within specificaton and camshaft-to-cap clearance is excessive, replace the cylinder head.
2. Cam chain
Except in cases of oil starvation, the cam chain wears very little. If the cam chain has stretched excessively and it is difficult to keep the proper cam chain tension, the chain should be replaced.
3. Cam sprockets
Check cam sprockets for obvious wear.
4. Cam chain dampers and tensioner
Inspect the top cam chain damper (stopper guide) and two (2) vertical (slipper-type) dampers for excessive wear. Any that shows excessive wear should be replaced. Worn dampers may indicate an improperly adjusted or worn-out cam chain.
Cylinder
1. Inspect the cylinder walls for scratches. If vertical scratches are evident, the cylinder wall should be rebored or the cylinder should be replaced.
2. Measure cylinder wall wear as shown. If wear is excessive, compression pressure will decrease. Rebore the cylinder wall and replace the piston and piston rings. Cylinder wear should be measured at three depths with a cylinder bore gauge. (See illustation.)
|
Standard |
Wear Limit |
Cylinder bore |
67.00 mm (2.638 in) |
67.10 mm (2.642 in) |
Cylinder taper |
- |
0.05 mm (0.002 in) |
Cylinder out-of-round |
- |
0.01 mm (0.0004 in) |
If the cylinder wall is worn more than the wear limit, it should be rebored.
Piston, Rings and Crankshaft
Piston, Rings and CrankshaftPiston and piston rings
1. Piston
a. Measure the outside diameter of the piston at the piston skirt. Measurement should be made at a point 7.8 mm (0.307 in) above the bottom edge of the piston. Place the micrometer at right angles to the piston pin.
Size |
|
Oversize 1 |
- |
Oversize 2 |
67.50 mm (2.657 in) |
Oversize 3 |
- |
Oversize 4 |
68.00 mm (2.677 in) |
b. Determine piston clearance as follows: Minimum bore measurement
- Maximum piston measurement = Piston clearance
EXAMPLE:
67.00 mm (2.6378 in)
- 66.96 mm (2.6362 in) = 0.04 mm (0.0016 in)
Piston clearance
Piston clearance:
Standard: 0.030 — 0.050 mm
(0.0012 —0.0020 in) Service limit: 0.1 mm (0.0039 in)
c. Piston ring/ring groove fit must have correct clearance. If the piston and ring have already been used, the ring must be removed and the ring groove cleaned of carbon. The ring should be then reinstalled. Use a feeler gauge to measure the gap between the ring and the land.
Side clearance |
Top |
0.03 — 0.07 mm (0.0012 -0.0028 in) |
2nd |
0.02 — 0.06 mm (0.0008 -0.0024 in) |
2. Piston ring a. The oversize top and middle ring sizes are stamped on top of the ring.
Oversize 1 |
- |
Oversize 2 |
0.50 mm (0.0197 in) |
Oversize 3 |
- |
Oversize 4 |
1.00 mm (0.0394 in) |
b. The expander spacer of the bottom ring (oil control ring) is color-coded to identify sizes.
The color mark is painted on the expander spacer.
Run-out limit: 0.03 mm (0.0012 in)
Size |
Color |
Oversize 1 |
- |
Oversize 2 |
Blue |
Oversize 3 |
- |
Oversize 4 |
Yellow |
c. Insert a ring into the cylinder, and push it approximately 20 mm (0.8 in) into the cylinder. Push the ring with the piston crown so the ring will be at a right angle to the cylinder bore. Measure the ring end gap with a feeler gauge. If the end gap exceeds tolerance, replace the whole set of rings.
NOTE: The end gap on the expander spacer of the oil control ring is unmeasurable. If the oil control ring rails show excessive gap, all three components should be replaced.
Standard |
Limit |
|
Top/2nd ring |
0.15 — 0.35 mm (0.0059 -0.0138 in) |
1.0 mm (0.039 in) |
Oil control (Rails) |
0.3 — 0.9 mm (0.012 —0.035 in) |
1.5 mm (0.059 in) |
Piston pin
1. Apply a light film of oil to pin. Install in connecting rod small end. Check for play. There should be no noticeable vertical play. If play exists, check connecting rod small end for wear. Replace pin and connecting rod as required.
2. The piston pin should have no noticeable free play in piston. If the piston pin is loose, replace the pin and/or the piston.
Crankshaft
1. Crankshaft run-out
Support the crankshaft at both ends on V-blocks. Measure the amount of crankshaft run-out on the main bearing journals with a dial gauge while rotating crankshaft.
If run-out exceeds limit, replace crankshaft.
2. Inspection of bearings
Check the bearings. If the inner or outer surface is burned, flaked, rough, scratched or worn, the bearings should be replaced.
3. Measuring main bearing oil clearance
a. Clean all crankshaft and crankcase journal surfaces.
b. Place upper crankcase half upside-down on a bench. Install bearing inserts into top crankcase.
c. Install crankshaft into upper crankcase.
d. Place Plastigage on crankshaft journal surface to be inspected.
NOTE: Do not move crankshaft until clearance check has been completed.
e. Install bearings into bottom crankcase. Carefully, place lower crankcase onto upper crankcase.
f. Install crankcase holding bolts 1 through 10. Tighten to full torque in torque sequence cast on crankcase.
Crankcase torque (8 mm bolt): 24 Nm (2.4 mkg, 17 ft-lb)
g. Remove bolts in reverse assembly order (10, 9, 8 ... etc.)
h. Carefully remove lower crankcase. Measure width of Plastigage on crankshaft journals to determine clearance.
Main bearing oil clearance: 0.040 — 0.064 mm (0.0016 -0.0025 in)
4. Crankshaft main bearing selection a. Numbers used to indicate crankshaft journal sizes are stamped on the L.H. crank web. The first five (5) are main bearing journal numbers, starting with the left journal. The four (4) rod bearing journal numbers follow in the same sequence.
The upper crankcase half is numbered 4, 5, or 6 as shown.
1. Main bearing numbers
b. The connecting rods are numbered 4 or 5. The numbers for rods are stamped with ink on the rod itself.
c. The proper bearing selection is made by subtracting the crankshaft journal number from the crankcase or rod size number. Use the color code to choose the proper bearing. EXAMPLE:
Rod No. (Minus) Journal No. = Bearing No.
5-2 = 3 No. 3 bearing is Brown. Use Brown bearing inserts.
BEARING COLOR CODE |
|
No. 1 |
Blue |
No. 2 |
Black |
No. 3 |
Brown |
No. 4 |
Green |
'No. 5 |
Yellow |
" For crankshaft main bearing only.
d. When assembling, apply a liberal coat of motor oil to all bearing surfaces.
NOTE: When applying final torque to the rod caps, observe the following procedures.
e. Apply molybdenum disulfide grease to connecting rod bolt threads. Apply tor-que evenly to both ends of the cap. While tightening, if a torque of 38 Nm (3.8 m kg, 27 ft-lb) or more is reached, DO NOT STOP tightening until final torque is reached. If tightening is interrupted between 35 Nm (3.5 mkg, 25ft-lb) and 41 Nm (4.1 nrvkg. 30 ft-lb), loosen the nut to less than 30 Nm (3.0 nrvkg, 22 ft-lb) and start again. Tighten to full torque specification without pausing.
Rod bearing oil clearance: 0.016 — 0.040 mm (0.0006 —0.0016 in)
Oil pump, Clutch and Starter drive
Oil pump, Clutch and Starter driveOil pump
1. Check the clearance between housing and outer rotor.
Standard clearance: 0.03 — 0.09 mm (0.0012 — 0.0035 in)
2. Check the clearance between outer rotor and inner rotor.
Standard clearance: 0.03 — 0.08 mm (0.0012 — 0.0031 in)
3. Check the plunger for scratches and wear.
Clutch
1. Clutch housing
a. Check the dogs on the clutch housing. Look for cracks and signs of galling on edges. If damage is moderate, deburr. If severe, replace the clutch housing.
NOTE: Galling on the friction plate dogs of the clutch housing will cause erratic clutch operation.
b. Check the clutch housing bearing for damage. If damaged replace bearing.
2. Clutch boss
a. The clutch boss contains a built-in damper beneath the first clutch plate (clutch plate 2). It is not normally necessary to remove the circlip and disassemble the built-in damper unless there is serious clutch chattering.
b. Check splines on clutch boss for galling. If damage is slight to moderate, deburr; if it is severe, replace clutch boss.
NOTE: Galling on clutch plate splines will cause erratic operation.
3. Friction and clutch plates
Check clutch steel plates and friction plates for heat damage. Measure friction plate thickness at 3 or 4 points. Check each clutch plate for signs of heat damage and warpage. Place on surface plate (plate glass is acceptable) and use feeler gauge as illustrated. If warpage exceeds tolerance, replace.
NOTE: For optimum performance, if any friction or clutch plate requires replacement it is advisable to replace the entire set.
4. Clutch actuating mechanism
a. Check the pull rod rack gear teeth for wear and damage, replace if damaged.
b. Check the pull rod thrust bearing for damage, replace if damaged.
c. Check the clutch lever shaft pinion gear teeth for damage, replace if damaged.
1 Plate washer 2. Thrust bearing 3. Pull rod
5. Clutch springs
Measure the clutch spring free length. Replace the springs as a set if any is less than minimum free length.
Clutch spring minimum length: 43.0 mm (1.69 in)
Transmission
1. Inspect each shift fork for signs of galling on gear contact surfaces. Check for bending. Make sure each fork slides freely on its guide bar.
2. Roll the guide bar across a surface place. If the bar is bent, replace.
3. Check the shift cam grooves for signs of wear or damage. If any profile has excessive wear and/or damage, replace cam.
4. Check the cam followers on each shift fork for wear. Check the ends that ride in the grooves in the shift cam. If they are worn or damaged, replace the shift forks.
5. Check shift cam dowel pins and side plate for looseness, damage or wear. Replace as required.
6. Check the shift cam stopper plate and circlip and stopper for wear. Replace as required.
7. Check the transmission shafts using a centering device and dial gauge. If any shaft is bent beyond specified limit, replace shaft.
Maximum run-out: 0.08 mm (0.0031 in)
8. Carefully inspect each gear. Look for signs of obvious heat damage (blue discoloration). Check the gear teeth for signs of pitting, galling or other extreme wear. Replace as required.
9. Check to see that each gear moves freely on its shaft
10. Check to see that all washers and clips are properly installed and undamaged. Replace bent or loose clips and bent washers.
11. Check to see that each gear properly engages its counterpart on the shaft. Check the mating dogs for rounded edges, cracks, or missing portions. Replace as required.
Starter drives
1. Electric starter clutch and gears
a. Check the surface of the idle gear for pitting or other damage. If severe, replace the gear.
b. Check the spring caps and the springs for deformation or damage. If severe, replace as necessary.
c. Check the starter clutch bolts (alien screw) for looseness. If loose, remove the bolts and replace with new bolts. Apply a thread locking compound such as "LOCTITE" to threads and tighten to specified torque. Stake over the end of the bolts.
Starter clutch bolt torque: 25 Nm (2.5 m-kg, 18 ft lb)
d. Check the "HY-VO" chain for damage and wear, replace if damaged.
e. Check the "HY-VO" chain guide for damage, replace if damaged.
Crankcases and strainer cover
I. Check crankcase for cracks or other
damage. I. Clean all oil passages and blow out with
compressed air.
3. Strainer cover: Apply a thread locking compound such as "LOCTITE" to strainer cover bolts during reassembly.
Bearing and oil seals
1. After cleaning and lubricating bearings, rotate inner race with a finger. If rough spots are felt, replace the bearing.
NOTE: Bearings are most easily removed or installed if the housings are first heated to approximately 95° - 125°C (200° - 250°F). Bring the case up to proper temperature slowly. Use an oven to avoid distortion.
2. Check oil seal lips for damage and wear. Replace as required.
Middle gear
Middle gearMiddle gear
1. Damper disassembly
NOTE: Disassembly of the middle gear damper requires the damper compressor (special tool) and a hydraulic press.
a. Place the middle drive shaft in a press with the damper compressor (special tool) in place as shown.
1. Damper compressor 2. Press
b. Press the damper spring and remove the spring retainers.
c. Remove the spring seat, spring, and damper cams from the drive shaft.
2. Inspection
a. Inspect the damper cam surfaces. Check for smooth cam action and excessive wear on the cam surface. If cam surface is severely worn, replace damper assembly.
b. Inspect the damper spring for fatigue, wear and damage. Replace as necessary.
c. Check bearing movement for damage to balls, rough spots, bearing looseness. Inspect gear teeth. If any gear tooth and/ or bearing are damaged, the gear set and/or bearing must be replaced.
3. Middle drive/driven shaft bearing removal
CAUTION: The following procedures should be performed only if the bearing or gear is to be replaced.
a. Middle drive gear
1) Bend down the lock washer of the nut with a suitable center punch.
2) Support the middle drive shaft in a vise securely.
Remove the drive pinion holding nut. Then, remove the drive pinion and bearing.
b. Middle driven gear
1) Support the drive flange in a vise securely. Remove the flange holding nut.
CAUTION: This holding nut has been locked with a thread locking compound, when reinstalling do not forget to apply a thread locking compound such as "LOCTITE" and punch.
2) Remove the drive flange from the driven shaft.
NOTE: Driven gear shaft bearing should be replaced together with a bearing housing.
Middle gear reassembly
a. Middle drive gear bearing and damper
1) Install the bearing onto the drive pinion and secure it with a new lock nut.
Tightening torque:
110 Nm (11.0 rrvkg, 80 ft lb)
2) Stake the lock washer of the nut to the slot on the drive pinion.
3) Install the driven damper cam onto the drive pinion shaft with the cam lobes positioned 90° from the row of shaft oil holes. Positioning tolerance is ± 1 spline (15°) from the 90° position.
4) Install the drive damper cams, spring, spring seat, and retainers using a press and the damper compressor.
1. Oil hole
b. Middle driven gear
1) Install the new bearing housing assembly onto the driven pinion shaft
CAUTION: Do not press the bearing outer race. Always press the inner race with care when installing.
2) Install the drive flange and new "0-ring" onto the driven gear shaft. Apply a thread locking compound such as "LOCTITE" tothe shaft threads and tighten the nut to the specified torque.
Tightening torque:
110Nm (11.0 m-kg, 80 ft lb)
3) Stake the nut with a center punch to lock as shown.
4) Install the new "O-ring" onto the bearing housing.
Engine Assembly and Adjustment
Engine Assembly and AdjustmentImportant information
1. All gaskets and seals should be replaced when an engine is overhauled. All gasket surfaces and oil seal lips must be cleaned.
2. Properly oil all mating engine and transmission parts and bearings during reassembly.
3. All circlips should be inspected carefully before reassembly. Always replace piston pin clips after one use. Replace distorted circlips. When installing a circlip, make sure that the sharp edged corner is positioned opposit to the thrust it receives. See the sectional view below.
4. All lock washers/plates and cotter pins must be replaced when they are removed. Lock washer/plate tab(s) should be bent over along the bolt or nut flat(s) after tightening the bolt or nut properly (see illustration).
Cotter pins should be replaced after one use.
Upper Crankcase Assembly
Upper Crankcase AssemblyCRANKSHAFT/PISTON
. WHEN INSTALLING THE CONNECTING ROD. BE SURE THAT THE SECURING NUTS ARE ON TOP.
Engine assembly
1. Upper crankcase a. Install the connecting rods onto the crankshaft with the proper connecting rod bearings and apply molybedenum disulfide grease to the bolt threads. Apply torque evenly to both ends of the cap.
CAUTION: While tightening, if a torque of 38 Nm (3.8 mkg, 27 ft-lb) or more is reached, DO NOT STOP tightening until final torque is reached.
If tightening is interrupted between 35 Nm (3.5 mkg, 25 ft-lb) and 41 Nm (4.1 mkg, 30 ft-lb), loosen the nut to less than 30 Nm (3.0 mkg, 22 ft-lb) and start again. Tighten to full torque specification without pausing.
CAUTION: When installing the connecting rod, be sure that the securing nuts are on top. Otherwise, engine damage will result.
Rod cap torque: 38 Nm (3.8 mkg, 27 ft-lb)
b. Install the proper crankshaft main bearings into the crankcase and place the crankshaft. Oil the bearings liberaly.
NOTE: Do not forget to install the crankshaft oil seal (L.H.), blind plug (R.H.), "HY-VO" chain and cam chain on the crankshaft before installing. Also, install the chain guide into upper crankcase if removed.
c. Install the starter idle gear, shaft, stopper plate, and new lock plate. Tighten the bolt securely and bend the lock tabs along the bolt flats.
Tightening torque:
10 Nm (1.0 mkg, 7.2 ft-lb)
1, Lock washer
d. Put the starter clutch and sprocket assembly in the "HY-VO" chain and lay it into the crankcase.
e. Install the A.C.G. Generator shaft into the starter clutch assembly.
f. Install the "HY-VO" chain oil spray nozzle. The locating pin on the nozzle should be placed into the crankcase locating slot. Do not forget to install the new "O-ring" onto the nozzle.
1. O-ring
g. Install the new "O-ring" onto the bearing housing and install it with the panhead screw.
h. Install the transmission main axle assembly on the upper crankcase. Point the bearing locating pin toward the crankshaft and lay it on the case.
1. Bearing locating pin
i. Install the middle driven gear (without the middle drive pinion gear).
j. Install the middle driven gear shaft end bearing.
k. Install the dowel pin with "O-ring" into the crankcase.
1. O-ring
2. Lower crankcase a. Install the transmission drive axle assembly into the crankcase.
b. Install the 5th wheel gear and bearing onto the drive axle. Install the bearing cover. Be sure the "O-ring" is on the cover.
1. O-ring
c. Install the shift cam and secure it with the guide pin. Install the stopper plate and bolt and tighten securely.
d. Install the neutral switch.
e. Install the shift forks and guide bar. Each shift fork is identified by a number cast on its side. All the numbers should face the left side and numbered 1, 2, and 3 from left.
Transmission, Clutch and Middle gear
Transmission, Clutch and Middle gearTRANSMISSION
3. Crankcase assembly a. Apply Yamaha bond #4 sealant or equivalent to the crankcase mating surface. Be very careful not to allow any sealant to come in contact with the oil gallery "O-ring" and crankshaft bearings. It is extremely important, however, that sealant be applied around the case stud holes. Apply sealant to within 2 — 3 mm (0.08 — 0.12 in) of the bearings.
CAUTION: Failure to apply sealant here will result in reduced oil pressure and possible crank seizure.
a. 2 — 3 mm (0.08 — 0.12 in) Do not apply sealant
b. The crankcases are assembled by placing the upper case half on the bench and lowering the lower case onto it.
NOTE: Be sure that shift fork No. 2 engages the groove in the 2nd pinion gear on the main axle.
CAUTION: Before installing and torquing the crankcase bolts, check to make sure the transmission is functioning properly by shifting it by hand with the shift cam.
c. Start installation of the crankcase bolts with the center crankshaft area bolts. Place the two bolts without washers in the oil filter area.
d. The crankcase bolts should be torqued in proper sequence. Refer to the tightening sequence in the illustration.
1. Engine ground wire
CRANKCASE TIGHTENING SEQUENCE LOWER CASE
UPPER CASE
8 mm bolt: 24 Nm (2.4 m kg. 1 7 ft lb) 6 mm bolt: 12 Nm (1.2 m kg. 8 7 ft-lb)
4. Oil pump and strainer cover
a. Place the oil pump drive chain on the transmission main axle.
b. Install the thrust plate onto the transmission main axle.
c. Install the oil pump drive sprocket onto the main axle without the spacer collar and place the oil pump drive chain on its sprocket.
1. Oil pump drive sprocket
d. Place the drive chain on the oil pump driven sprocket and install the pump on the crankase. The "O-ring" should be installe properly.
e. Install the drive chain cover on the oil pump and secure with the 2 shouldered bolts and one normal 6 mm bolt.
Tlightening torque:
12 Nm (1.2 mkg, 8.7 ft-lb)
f. Install the strainer cover and torque the bolts to the specification.
Tightening torque:
7 Nm (0.7 m-kg, 5.1 ft lb)
1 Wire clamps
CLUTCH
5. Clutch assembly
a. Insert the spacer coller into the oil pump drive sprocket.
b. Install the primary driven gear (clutch housing) without the bearing and inner spacer.
CAUTION: Be sure that the oil pump drive gear tabs engage the clutch housing grooves on it's back or the tabs will be damaged when tightening the clutch boss securing nut.
1. Spacer collar
c. Install the primary driven gear bearing and inner spacer into the clutch housing.
1 Driven gear bearing 2. Inner spacer
d. Install the large thrust plate and clutch boss onto the main axle.
e. Install a new lock washer-and nut and tighten the nut to the specified torque. Use the clutch boss holder (special tool).
Tightening torque:
70 Nm (7.0 nrvkg, 50 ft-lb)
1. Clutch boss holder
f. Bend the lock washer tabs along the nut flats.
1. Lock tab
g. Install the clutch plates and friction plates alternately on the clutch boss, starting with a friction plate and ending with a friction plate.
h. Install the plate washer, thrust bearing, and clutch pull rod into the clutch pressure plate from inside.
1. Pull rod 2. Thrust bearing 3. Plate washer
i. Install the pressure plate assembly onto the clutch boss.
NOTE: Pressure plate has a dot on it which must line up with the dot on clutch boss.
j. Install the clutch springs and screws. Tighten the screws.
Clutch screw torque: 8 Nm (0.8 m-kg, 5.8 ft lb)
k. Install the oil collector plate.
1. Oil collector plate
I. Set the gear of the clutch pull rod on the pressure plate facing approximately 45° from horizontal toward the rear; set the clutch lever (if installed) on the right crankcase cover parallel to the gasket surface and install the cover to the crankcase. Do not forget to install two dowel pins.
m. If the clutch lever has been removed, install the lever return spring and lever on the shaft after installing the right crankcase cover. In this case make sure that the punch mark on the lever should align with the mark on the crankcase cover when pushing the lever towards the front by hand and then install the circlip.
1 Push
6. Middle gear (installation only, refer to page for the middle gear adjustment). a. Install the middle drive gear assembly with the proper size of shim(s) and secure it with the bearing retainers and new "TORX" screws.
Tightening torque: 25 Nm (2.5 mkg, 18 ft-lb)
b. Stake the screw heads to the dents on the bearing retainers with a center punch.
c. Install the driven gear assembly with the proper size of shims and secure it with the bolts. Apply a thread locking compound such as "LOCTITE" to the bolt threads.
Tightening torque:
25 Nm (2.5 mkg, 18 ft-lb)
1 Shims
d. Install the middle gear case half moon seal onto the crankcase.
1. Seal
Shifter, Generator, Starter and Pickup coils
Shifter, Generator, Starter and Pickup coils7, Shifter assembly a. Install the shift shaft assembly with the stopper lever.
b. Install the shift lever assembly with the positioning spring is properly located on the stopper pin and the teeth should be set properly as shown.
c. Install the left crankcase cover (shifter cover) using a new gasket.
Tightening torque:
12Nm(1.2 mkg, 8.7 ft-lb)
8. A.C. generator a. Install the rotor onto the shaft and tighten the bolt using the rotor holding tool (special tool).
Tightening torque:
55 Nm (5.5 mkg, 40 ft-lb)
b. Install the stator coil assembly onto the crankcase and align the grooves on the stator core with the bolt holes on the crankcase.
c. Install the A.C. generator cover assembly and tighten the bolts to the specification. Do not forget to install the new gasket.
Tightening torque:
12 Nm (1.2 mkg, 8.7 ft-lb)
9. Starter motor
a. Route the A.C. generator leads as shown.
b. Install the starter motor and tighten the bolts to the specification.
Tightening torque: 7 Nm (0.7 mkg, 5.1 ft-lb)
NOTE: Be careful the "O-ring" is not damaged when installing the starter motor.
1 O-ring 2. A. C generator lead
10. Pick-up coil assembly
a. Install the pick-up coil assembly onto the crankcase.
b. Install the timing plate on the crankshaft and tighten the bolt to the specification.
NOTE:
1) Note that there is the locating pin on the crankshaft and the corresponding slot in the timing plate which must be aligned to install the timing plate.
2) Make sure the wire harness clips are properly positioned.
Pistons, Cylinder and Head
Pistons, Cylinder and Head11. Pistons and cylinder
a. Install the pistons on the rods. The arrow on the piston must point to the front of the engine.
NOTE: Before installing the piston pin clips, cover the crankcase with a clean rag so you will not accidentally drop the circlip into the crank-case. Always install new piston pin circlips.
b. Install the rear chain guide on its pivot. Tighten the holding bolt until it stops and then loosen 1/4 turn and then tighten the lock nut
1. Holding bolt 2. Rear cran guide
c. Install the new cylinder base gasket and dowel pins. Install the new "O-rings" to the right side dowel pins.
d. Set the crankshaft so that the all pistons are equal height and align the piston rings as shown.
CAUTION: Make sure the ends of the oil ring expanders are not overlapped.
NOTE: Manufacture's marks or numbers stamped on the rings are en the top side of the rings. Coat the pistons and rings well with oil.
e. Install the piston ring compressors (special tool) and piston bases (special tool). Four piston bases are required.
1. Piston bases 2. Piston ring compressors
f. Tie the cam chain with a piece of mechanic's wire and feed it through the chain opening. Carefully lower the cylinder onto the pistons. Remove the ring compressors and piston bases and repeat this procedure for pistons 1 and 4.
g. Install the cylinder securing nut (front side) and tighten it to the specification.
Tightening torque:
20 Nm (2.0 mkg, 14 ft lb)
h. Set the dial gauge on the No. 1 piston head center as shown to find the No. 1 piston top dead center and check whether the "T" mark on the timing plate and stationary pointer are aligned or not. If not, loosen the pointer securing screw and adjust.
CYLINDER HEAD
12. Cylinder head and cam shafts a. Install the new cylinder head gasket. Install the dowel pins and "O-rings". Locate the cam chain cavity cylinder seal with the tabs down.
b. Install the cylinder head onto the cylinder. Pull the cam chain through the cylinder head as it is installed. Tie the cam chain so that it does not fall into the crankcase.
c. Place the upper cylinder head nuts and washers in place. Follow the illustration for the proper tightening sequence. Torque all nuts in two stages and final torque the upper nuts to the specification.
Tightening torque:
32 Nm (3.2 mkg, 23 ft lb)
NOTE: Don't forget the lower nuts on the front and rear of the cylinder head. Torque to the specification.
Tightening torque: 20 Nm (2.0 mkg, 14ft-lb)
NOTE: Tighten the nuts in two stages, 1/2 torque value and then full torque value. Also lubricate the bolt threads with the engine oil to achieve proper torque values.
a. Copper washers
d. Install the front cam chain guide being certain that it is in its holder down below.
e. Rotate the crankshaft counterclockwise direction until the crankcase pointer and "T" mark on the timing plate are aligned.
f. With the cylinders No. 1 and 4 at the top dead center, slip the cam chain over the sprocket.
cj. Lubricate all cam caps and cam bearings surfaces liberally with oil.
h. Place the cam caps in their proper positions. Install the bolts only finger tight.
CAUTION: The cam caps must be tightened evenly or damage to the cylinder head, cam caps and cam will result. The spaces between the caps and cylinder head should be equal.
i. Torque the cam cap bolts in two stages and final torque to the specification.
Tightening torque:
10 Nm (1.0 m-kg, 7.2 ft-lb)
CAM CHAIN
13. Cam chain, cam sprockets and chain tensioner a. Rotate each cam shaft until the dot on the cam is aligned with the hole on the right cam cap.
CAUTION: Use extreme caution when rotating the cams. Two possible dangers exist. First, the wrench may contact the head and fracture it. Or second, a valve may become bent if the cam is turned the wrong way.
b. Carefully lift the cam chain from the exhaust cam sprocket and pull upward to remove any slack in the chain between the crankshaft and the exhaust cam sprocket. With all slack removed, place the chain back on the cam sprocket.
c. Grip each sprocket simultaneously and place them on the camshaft shoulders while continuing to keep tension on the chain from the crankshaft to the exhaust sprocket
CAUTION: Use only the special hardened shouldered bolts to install the cam chain sprockets to the cams.
Make sure the rollers of the cam chain are centered on both chain guides.
d. Rotate the sprockets slightly to align the bolt holes and insert one special bolt in each sprocket.
NOTE: Tighten only finger tight at this time.
e. Install the center chain guide.
f. Rotate the crankshaft counterclockwise and align the "C" mark on the timing plate with the timing pointer.
g. Remove the end plug and spring from the tensioner assembly.
h. Unlock the oneway cam by pushing it with your finger and push the tensioner rod into the tensioner body until it stops.
i. Install the tensioner to the cylinder and torque the bolts to the specification.
Tightening torque:
10 Nm (1.0 m-kg, 7.2 ft-lb)
j. Reinstall the spring and end plug with the gasket. Torque the end plug to the specification.
Tightening torque:
15 Nm (1.5 m-kg, 11 ft-lb)
k. Rotate the crankshaft more than one full revolution and align the "T" mark on the timing plate with the timing pointer. With the crankshaft at the "T" mark, the dots on the cams should be aligned with the raised holes on the right cam caps. If they are not aligned, disassemble the sprockets and chain tensioner and repeat above procedures.
I. Rotate the crankshaft and install the two remaining shoulder bolts into the cam sprockets. Torque all four sprocket holding bolts to the specification.
CAUTION: Be sure to attain the specified torque value to avoid the possibility of these bolts coming loose and causing serious damage to the engine.
Tightening torque:
20 Nm (2.0 m-kg, 14 ft-lb)
m. Adjust all valves as described in the "PERIODIC INSPECTIONS AND ADJUSTMENTS".
n. Install the cylinder head cover with a new gasket.
o. Install the left and right crankcase covers. The left crankcase cover (pickup coil cover) is required a gasket.
Middle gear servicing
1. Disassembly
Refer to page 3-13 for disassembly.
2. Inspection
Refer to page 3-29 for inspection.
3. Gear lash check
NOTE: The middle gear lash can be checked only when the gears are installed in the crankcase.
a. Install the middle drive pinion holder (special tool) on the crankcase to hold the drive gear stationary during the lash measurement.
NOTE: Before installing the tool, loosen the holder bolt all the way out and after installation tighten this bolt as tight as necessary (finger tight is generally sufficient).
1. Middle drive pinion holder
b. Set the dial gauge to the middle drive flange as shown and gently rotate the drive flange back and forth. Note the lash measurement on the dial gauge.
Middle gear lash: 0.1 ~~ 0.2 mm (0.004 - 0.008 in)
a Middle gear lash
c. Check this engagement at 4 positions. Rotate the drive flange 90° each time and repeat the gear lash check.
NOTE: If the gear lash exceeds the specified limit and adjustment is necessary, the engine or swing arm should be removed from the motorcycle.
4. Gear lash adjustment a. Install the driven gear housing assembly into the crankcase leaving about a 2 mm (0.08 in) gap between the housing and crankcase and install the two bolts to the bearing housing 180° opposite to each other.
a. 2 mm (0.080 in)
b. Install the middle drive shaft holder and dial gauge (refer to "Middle gear lash check").
c. Slowly tighten the bolts alternately until the dial gauge lash measurement reaches 0.2 mm (0.008 in).
Middle Gear
Middle GearMIDDLE GEAR/DAMPER
a. Middle gear lash 0 2 mm (0.008 in)
d. Measure the gap between the driven gear bearing housing flange and the crankcase with a feeler gauge. This is the shim size required.
1 Feeler gauge
e. Install the proper sized shims as shown and tighten the driven gear housing to the specified torque. Recheck the gear lash, it should be within the specification, if not readjust the shims.
Gear lash: 0.1 — 0.2 mm
(0.004 — 0.008 in)
1. Shims
5. Drive gear positioning NOTE:
When the following part(s) is replaced with new one(s), drive gear positioning is necessary:
a. Crankcase
b. Middle gears
c. Middle gear bearing housing
a. The shim thickness necessary for the drive gear positioning can be calculated from the infomations found on the upper crankcase and on the drive gear end.
b. To fined shim thickness "A" use the formula:
A = c - a - b
Where:
a = a numeral (usually a decimal number) printed on the shaft end as shown above and either added to or detracted from the nominal size "43".
b = a bearing thickness (considered constant)
c = a numeral (usually a decimal number) found on the upper crankcase half near the main bearing selection numbers and added to the nominal size "60".
Distance "b" = 16.94 mm
Example:
1) If the shaft is marked +03....."a"
is 43.03 mm.
2) "b" is 16.94 mm.
3) If the crankcase is stamped "45" ....."c" is 60.45 mm.
A = c - a - b
A = 60.45 - 16.94 - 43.03
A = 0.48
Then the necessary shim thickness
is 0.48 mm. c. Shim size are supplied in the following thicknesses:
0.15 mm, 0.20 mm, 0.30 mm, 0.40 mm, and 0.50 mm.
Because the shims can only be selected in 0.05 mm increments the following chaft should be used when encountering last digits that are not 5 or zero(0):
Last digits |
Rounding |
0, 1,2 |
0 |
3, 4, 5, 6, 7 |
5 |
8,9 |
10 |
Shim 0.30 mm + 0.15 mm
Reinstalling Engine
Reinstalling EngineRemounting engine
1. Assembly is the reverse the applicable removal steps.
CAUTION: Always use new bolts in the drive shaft coupling.
2. Install and tighten the engine mounting bolts-
Engine mounting bolt torque: 8 mm bolt:
20 Nm (2.0 m-kg, 14 ft-lb) 10 mm bolt:
42 Nm (4.2 m-kg, 30 ft-lb) 12 mm bolt:
70 Nm (7.0 m-kg, 50 ft-lb)
3. Install a new "0-ring" and install the oil cooler spacer to the crankcase. Make sure the "0-ring" is positioned properly.
Oil cooler spacer bolt torque: 50 Nm (5.0 m-kg, 36 ft-lb)
1. 0-ring
4. Install a new "O-ring". Make sure the "O-ring" is positioned properly.
1 O-ring
5. Install the oil filter element into the filter cover.
Oil filter mounting bolt torque: 15 Nm (1.5 m-kg, 11 ft lb)
6. Install and tighten the engine oil drain plug and middle gear drain plug.
Engine oil drain plug torque: 43 Nm (43 m-kg, 31 ft-lb)
Middle gear drain plug torque: 16 Nm (1.6 m-kg, 11 ft-lb)
7. Add oil to the engine and middle gear case.
Oil quantities: 3.6 L (3.2 Imp qt, 3.8 US qt)
NOTE: The oil quantities are for an overhauled engine.
OIL COOLER
Chapter 4. Carburetor and Air Cleaner
Chapter 4. Carburetor and Air CleanerCARBURETOR
Section view
Specifications
Main jet |
# 102.5 |
Jet needle |
4HZ26-3 |
Needle jet |
Y-0 (#318) |
Starter jet |
# 32.5 |
Fuel level |
5.0 ± 1 mm (0.20 ± 0.04 in) |
Float height |
22.3 mm (0.878 inj |
Pilot screw |
Preset |
Float valve seat |
0 2.0 |
Engine idle speed |
1.100 r/min. |
CAUTION: The pilot screw settings are adjusted for maximum performance at the factory with the use of specialized equipment. Do not attempt to change these settings. If all other engine systems are functioning correctly, any changes will decrease performance.
Disassembly
CAUTION: Separation of the carburetor is not recommended. Usual disassembly for cleaning and inspection is not necessary to separate the carburetors. The carburetor body support screws are locked with a locking compound such "LOCTITE". If the carburetors are separated, misalignment will result.
1. Loosen the starter lever securing screws and remove the starter lever shaft, bushes, and levers. Note the positions of the bushes.
2. Remove the vacuum chamber cover and remove the spring and diaphragm (vacuum piston).
NOTE: Note that there is the tab on the rubber diaphragm. There is the matching recess in the carburetor body for the diaphragm tab.
3. Remove the pilot air jet.
1. Pilot air jet
4. Remove the screws holding the float chamber cover and remove the cover. The main and pilot jets are located in the float bowl. Remove the jets if necessary.
1. Pilot jet 2. Main jet
5. Pull out the float pivot pin. Remove the float assembly. Be careful to not lose the float valve under the float arm.
6. Remove the float valve seat securing screw and remove the float valve seat.
1 Float valve seat
7. Reassemble in reverse order. Pay close attention to the installation of the vacuum piston diaphragm and the location of each jet.
8. If the carburetors should be separated, care must be taken so that they are put together in place according to the following procedures:
a. Place the carburetors on a suface plate and install the lower support plate. Apply a thread locking compound such as "LOCTITE" and tighten the screws securely while holding the carburetor body.
NOTE: When reassembling, the surface plate should be used for the proper carburetor aligmment.
1. Lower support plate 2. Surface plate
b. Install the upper support plate. Apply a thread locking compound such as "LOCTITE" to the support screw threads and tighten the screws securely.
Inspection
1. Examine the carburetor body and fuel passages. If contaminated, wash the carburetor in a petroleum-based solvent. Do not use caustic carburetor cleaning solutions. Blow out all passages and jets with compressed air.
2. Examine the condition of the floats. If the floats are damaged, they should be replaced.
3. Inspect the float needle valve and seat for wear or contamination. Replace these components as a set.
4. Inspect the vacuum piston and rubber diaphragm. If the piston is scratched or the diaphragm is torn, the assembly must be replaced.
1. Vacuum piston 2. Needle jet 3. Set spring
4. Needle jet cover
5. Inspect the starter plunger for damage. If damaged, replace.
Adjustment
Fuel level
NOTE: Before checking the fue level, note the following:
1. Place the motorcycle on a level suface.
2. Adjust the motorcycle position by placing a suitable stand or a garage jack under the engine so that the carburetor is positioned vertically.
1. Connect the level gauge (special tool) or a vinyl pipe of 6 mm (0.24 in) in inside diameter to the float bowl nozzle left or right side carburetor.
2. Set the gauge as shown and loosen the drain screw.
4. Note the fuel level and bring the gauge to the other end of the carburetor line and repeat step 3 above. Note the fuel level again and compare it with the pre-voius gauge reading. They should be equal. If not, place a suitable size of wooden piece or the like under the center stand and adjust.
5. Check the fuel level one by one. The level should be in the specified range.
Fuel level: 5.0 ± 1 mm (0.20 ± 0.04 in) below from the carburetor mixing chamber body edge.
1. Level gauge 2. Drain screw
3. Start the engine and stop it after a few minutes of run. This procedure is necessary to obtain the correct fuel level.
NOTE: Make sure the fuel cock is "ON" or "RES" position.
6. If the fue level is incorrect, remove the caburetor assembly from the motorcycle and check the fuel valve(s) and float assembly(s) for damage.
7. If no damage is found correct the fuel level by slightly bending the float arm tang. Recheck the fuel level.
1. Float arm tang
AIR CLEANER AND CRANKCASE VENTILATION SYSTEM
Refer to "CHAPTER 2" for the air cleaner maintenance.
Chapter 5. Chassis
Chapter 5. ChassisFront Wheel
Front WheelFRONT WHEEL
Removal
1. Place the motorcycle on the center stand.
2. Remove the speedometer cable from the speedometer.
3. Remove the front fender securing bolts and remove the fender.
4. Remove the front fork brace securing bolts and remove the brace.
5. Remove the left brake caliper securing bolts and remove the left brake caliper assembly.
6. Loosen the pinch bolt securing the wheel axle and remove the axle nut.
I. Pinch bolt
7. Remove the axle shaft. In this case, make sure the motorcycle is properly supported.
NOTE: Do not depress the brake lever when the wheel is off the motorcycle as the brake pads will be forced to shut.
8. Lower the wheel until the brake disc comes off the caliper. Turn the right caliper outward so they do not obstruct the wheel and remove the wheel.
Remove any corrosion from the axle with fine emery cloth. Place the axle on a surface plate and check for bends. If bent, replace axle. Do not attempt to straighten a bent axle.
Tubeless tires and aluminum wheels
This motorcycle is equipped with aluminum wheels designed to be compatible with either tube or tubeless tires.
Tubeless tires are installed as standard equipments.
WARNING: Do not attempt to use tubeless tires on a wheel designed for use only with tube-type tires. Tire failure and personal injuly may result from sudden deflation.
Tube-type Wheel — Tube-type Tires only Tubeless type Wheel —
Tube-type or Tubeless tires
WARNING; When using tube-type tires, be sure to install the proper tube also.
TUBELESS TIRE
TUBE-TYPE TIRE
TIRE
WHEEL
NOTE: Refer to "Tubeless tire and aluminum wheel manual" for the proper tubeless and aluminum wheel servicing.
1. Check for cracks, bends or warpage of wheels. If a wheel is deformed or cracked, it must be replaced.
2. Check wheel run-out. If the deflection exceeds the tolerance below, check the wheel bearings or replace the wheel as required.
Rim-run-out limits:
Vertical - 2 mm (0.08 in) Lateral - 2 mm (0.08 in)
3. Check wheel balance. Rotate the wheel lightly several times and observe resting position. If the wheel is not statically balanced, it will come to reset at the same position each time. Install an appropriate balance weight at lightest position (at top).
NOTE: The wheel should be balanced with the brake disc installed.
CAUTION: Tire and wheel should be balanced whenever either one is changed or replaced. Failure to have wheel balanced can result in poor performance, adverse handling characteristics, and shortened tire life.
4. After installing a tire, ride conservatively to allow the tire to seat itself on the rim properly- Failure to allow proper seating may cause tire failure, resulting in damage to the motorcycle and injury to the rider.
5. After repairing or replacing a tire, check to be sure the valve stem lock nut is securely fastened. It not, torque it as specified.
Tightening torque:
1.5 Nm (0.15 m-kg 1.1 ft lb)
Replacing wheel bearings
If the bearings allow play in the wheel hub or if wheel does not turn smoothly, replace the bearings as follows:
1. Clean the outside of the wheel hub.
2. Drive the bearing out by pushing the spacer aside and tapping around the perimeter of the bearing inner race with a soft metal drift pin and hammer. The spacer "floats" between the bearings. Both bearings can be removed in this manner.
WARNING: Eye protection is recommended when using striking tools.
3. To install the wheel bearing, reverse the above sequence. Use a socket that matches the outside race of the bearing as a tool to drive in the bearing.
CAUTION: Do not strike the center race or balls of the bearing. Contact should be made only with the outer race.
Installing front wheel
When installing the front wheel, reverse the removal procedure. Note the following points:
1. Lightly grease the lips of the front wheel oil seals and the gear teeth of speedometer drive and driven gears. Use lightweight lithium soap base grease.
2. Make sure there is enough gap between the disc pads to slide the disc into place.
3. Make sure the projecting portion (torque stopper) of the speedometer housing is positioned correctly.
1. Torque stopper
4. Tighten the axle nut.
Axle nut torque:
78 Nm (7.8 m-kg, 50 ft lb)
NOTE: Tighten the pinch bolts temporarily before tightening the axle nut.
5. Install the left brake caliper assembly.
lighting torque 35 Nm (3.5 rrvkg, 25 ft lb)
6. Install the front fork brace.
7. Install the front fender.
8. Before tightening the pinch bolts, stroke the front forks several times to make sure of proper fork operation. With the pinch bolts loose, work the left fork leg back and forth until the proper clearance between the disc and caliper bracket are obtained.
9. Tighten the left and right pinch bolts.
Axle pinch bolt torque: 20 Nm (2.0 m-kg, 14fMb)
Rear Wheel
Rear Wheel
Removal
1. Place the motorcycle on the center stand.
2. Remove the seat. Next, remove the rear fender installation bolts and remove the rear fender.
3. Remove the axle nut cotter pin and axle nut.
4. Loosen the rear axle pinch bolt.
1 Pinch belt
5. Remove the tension bar from the brake caliper assembly. The tension bar can be removed by removing the cotter pin and nut from the tension bar bolt.
1. Cotter pin 2. Tension bar nut
6. While supporting the brake caliper, pull out the rear axle.
7. Hold up the brake caliper assembly.
8. Move the wheel to the right side to separate it from the final gear cases and remove the rear wheel.
Rear axle inspection
Remove any corrosion from the axle with fine emery cloth. Place the axle on a surface plate and check for bends. If bent, replace axle. Do not attempt to straighten a bent axle.
Rear wheel inspection
NOTE: Refer to "Tubeless tire and aluminum wheel manual" for the proper tubeless and aluminum wheel servicing.
1. Check for cracks, bends or warpage of wheels. If a wheel is deformed or cracked, it must be replaced.
2. Check wheel run-out. If the deflection exceeds the tolerance below, check the wheel bearings or replace the wheel as required.
Rim-run-out limits:
Vertical - 2 mm (0.08 in) Lateral - 2 mm (0.08 in)
3. Check wheel balance. Rotate the wheel lightly several times and observe resting position. If the wheel is not statically balanced, it will come to reset at the same position each time. Install an appropriate balance weight at lightest position (at top).
NOTE: The wheel should be balanced with the brake disc installed.
CAUTION: Tire and wheel should be balanced whenever either one is changed or replaced. Failure to have wheel balanced can result in poor performance, adverse handling characteristics, and shortened tire life.
4. After installing a tire, ride conservatively to allow the tire to seat itself on the rim properly- Failure to allow proper seating may cause tire failure, resulting in damage to the motorcycle and injury to the rider.
5. After repairing or replacing a tire, check to be sure the valve stem lock nut is securely fastened. It not, torque it as specified.
Tightening torque:
1.5 Nm (0.15 m-kg 1.1 ft lb)
Replacing wheel bearings
If the bearings allow play in the wheel hub or if wheel does not turn smoothly, replace the bearings as follows:
1. Clean the outside of the wheel hub.
2. Drive the bearing out by pushing the spacer aside and tapping around the perimeter of the bearing inner race with a soft metal drift pin and hammer. The spacer "floats" between the bearings. Both bearings can be removed in this manner.
WARNING: Eye protection is recommended when using striking tools.
3. To install the wheel bearing, reverse the above sequence. Use a socket that matches the outside race of the bearing as a tool to drive in the bearing.
CAUTION: Do not strike the center race or balls of the bearing. Contact should be made only with the outer race.
Installing rear wheel
1. Lightly grease lips of rear wheel oil seals.
2. Make sure the brake pads are installed properly and that there is enough gap to install the rear disc.
CAUTION: If it is necessary to separate the brake pads, do so carefully to avoid damage to the pad surface.
3. Install the wheel assembly and axle.
NOTE: Before installing the rear wheel, apply a light coating of lithium base grease to the final gear case splines.
When installing the rear wheel, be sure the splines on the wheel hub fit into the final gear case.
CAUTION: Always use a new cotter pin on the axle nut.
Tightening torque:
Axle nut: 105 Nm (10.5 m-kg, 75 ft lb)
Axle pinch bolt:6 Nm (0.6 m-kg, 4.3 ft-lb)
4. Install the rear fender and seat.
Brakes
BrakesCAUTION: Disc brake components rarely require disassembly. Do not disassemble components unless absolutely necessary. If any hydraulic connection in the system is opened, the entire system should be disassembled, drained, cleaned and then properly filled and bled upon reassembly. Do not use solvents on brake internal components. Solvents will cause seals to swell and distort. Use only clean brake fluid for cleaning. Use care with brake fluid. Brake fluid is injurious to eyes and will damage painted surfaces and plastic parts.
Caliper pad replacement
It is not necessary to disassemble the brake caliper and brake hose to replace the brake pads.
1. Remove the brake caliper securing bolts and remove the brake caliper assembly.
2. Remove the brake caliper cover.
1. Brake caliper cover
3. Remove the pad retaining clips.
1. Pad retaining clip
4. Pull out the pad retaining pins and remove the pad spring.
1 Pad retaining pin 2. Pad spring
5. Remove the brake pads.
1. Brake pad
6. Install the new brake pads and shims. Before installing the pads, install the shim on the back plate which faces the caliper piston. Also replace the following parts if pad replacement is required.
NOTE: Replace the pads as a set if either is found to be worn to the wear limit.
a. Pad retaining clips
b. Pad retaining pins
c. Pad spring
d. Brake pads
e. Shims
Caliper disassembly
1. Remove the caliper brake hose. Allow fluid in the caliper assembly to drain into a container.
2. Place the open hose end into the container and pump the old fluid out carefully.
3. Remove the caliper support bolts and the brake pads as described in the caliper pad replacement procedure.
4. Remove the caliper assembly from the caliper frame.
5. Remove the retaining ring and the dust seal.
6. Remove the piston.
CAUTION: Cover the piston with a rag. Use care so that the piston does not cause injury as it is expelled from the cylinder.
7. Remove the piston seal.
Master cylinder disassembly
1. Front master cylinder a. Remove the brake light switch.
b. Remove the brake hose.
c. Remove the brake lever and spring.
d. Remove the master cylinder from the handlebar. Remove the reservoir cap and drain the remaining fluid.
e. Remove the master cylinder dust boot
f. Remove the snap ring.
g. Remove the master cylinder cup assembly. Note that the cylinder cups are installed with the larger diameter (lips) inserted first.
Brake inspection and repair
Recommended brake component
Replacement schedule: Brake pads; As required Piston seal, dust seal; Every two years Brake hoses; Every four years Brake fluid; Replace only when brakes are disassembled
1. Replace the caliper piston if it is scratched.
2. Replace any brake pad worn beyond limits. Always replace the brake pads as a set.
Wear limit:
Front and rear 0.5 mm (0.020 in)
See Caliper pad replacement procedure for a listing of the parts to be replaced when pads are replaced.
3. Replace piston and dust seals if damaged. Replace seals every two years.
4. Inspect master cylinder body. Replace if scratched. Clean all passages with new brake fluid.
5. Inspect the brake hoses. Replace every four years or immediately if cracked, frayed, or damaged.
6. Check for wear and deflection of disc.
Maximum deflection (front and rear):
0.15 mm (0.006 in) Minimum disc thickness:
Front: 7.0 mm (0.28 in)
Rear: 8.0 mm (0.32 in)
WARNING: If disc is worn beyond minimum thickness or deflection exceeds specified amount, replace disc.
MASTER CYLINDER
Brake reassembly
1. All internal parts should be cleaned in new brake fluid only. Internal parts should be lubricated with brake fluid when installed.
2. Caliper reassembly
Replace the following parts whenever a caliper is disassembled: bleed screw and cap, piston seal, dust seal, and retaining ring.
a. Install the piston seal and piston. Place the caliper cylinder into the caliper frame.
b. Install the shims, brake pads, pad spring, pad retaining pins and the pad retaining clips.
c. Install the caliper assembly on the front fork (For front brake). Install the caliper assembly on the bracket (For rear brake).
NOTE: Apply a thread locking compound such as "LOCTITE" to the support bolts.
Caliper support bolt torque: 35 Nm (3.5 mkg, 25 ft-lb)
3. Attach the brake hoses.
Brake hose torque: 26 Nm (2.6 mkg, 19 ft lb)
4. Master cylinder reassembly
Reassemble master cylinder as shown in illustration.
Brake hose torque: (all brake union blots) 26 Nm (2.6 mkg, 19 ft-lb)
5. Brake disc assembly
If the brake disc has been removed from the hub or is loose, tighten the bolts.
Disc bolt torque: 20 Nm (20 m-kg, 14 ft-lb)
6. Air bleeding
NOTE: Bleed the brake system in order of the following steps.
1. Anti-dive unit
2. Front brake caliper
3. Rear brake caliper
WARNING: If the brake system is disassembled or if any brake hose has been loosened or removed, the brake system must be bled to remove air from the brake fluid. If the brake fluid level is very low or brake operation is incorrect, bleed the brake system.
Failure to bleed the brake system properly can result in a dangerous loss of braking performance.
a. Add proper brake fluid to the reservoir. Install the diaphragm, being careful not to spill or overflow the reservoir.
b. Connect the clear plastic tube of 4.5 mm (3/16 in) inside diameter tightly to the bleed screw. Put the other end of the tube into a container.
c. Slowly apply the brake lever or pedal several times. Pull in the lever (push down the pedal). Hold the lever or pedal in "on" position. Loosen the bleed screw. Allow the lever or pedal to travel slowly toward its limit When the limit is reached, tighten bleed screw. Then release the lever (or pedal).
d. Repeat step "c" procedure until all air bubbles are removed from system.
NOTE: If bleeding is difficult it may be necessary to let the brake fluid system stabilize for a few hours. Repeat the bleeding procedure when the tiny bubbles in the system settle out.
Brake disc installation
1. When installing the brake disc(s), the slots on the disc should be positioned as shown.
NOTE: Make sure the directions in which discs are installed. For this purpose an identification mark is stamped on the brake disc.
1. Slot 2. Identification mark (Rotating direction)
1. Slot 2 Identification mark (Rotating direction)
Tires
TiresTo ensure maximum performance, long service, and safe operation, note the following: Tire air pressure
Always check and adjust the tire pressures before operating the motorcycle.
WARNING: Tire inflation pressure should be checked and adjusted when the temperature of the tire equals the ambient air temperature. Tire inflation pressure must be adjusted according to total weight of cargo, rider, passenger, and accessories (fairing, saddlebags, etc. if approved for this model), and vehicle speed.
Basic weight: With oil and full fuel tank |
242 kg (534 lb) |
|
Maximum load |
194kg (428 lb) |
|
Cold tire pressure |
Front |
Rear |
Up to 90 kg (198 lb) load* |
226 kPa (2.3 kg/cm'. 32 psi) |
245 kPa (2.5 kg/cm2. 36 psi) |
90 kg (198 1b).-Maximum load |
245 kPa (2.5 kg/cm2, 36 psi) |
284 kPa (2.9 kg/cm2, 42 psi) |
High speed riding |
245 kPa (2.5 kg/cm2. 36 psi) |
284 kPa (2.9 kg/cm2. 42 psi) |
Load is the total weight of cargo, rider, passenger, and accessories.
WARNING: Proper loading of your motorcycle is important for the handling, braking, and other performance and safety characteristics of your motorcycle. Do not carry loosely packed items that can shift. Securely pack your heaviest items close to the center of the motorcycle, and destribute the weight evenly from side to side. Properly adjust the suspension for your load, and check the condition and pressure of your tires. NEVER OVERLOAD YOUR MOTORCYCLE. Make sure the total weight of the cargo, rider, passenger, and accessories (fairing, saddlebags, etc. if approved for this model) does not exceed the maximum load of the motorcycle. Operation of an overloaded motorcycle could cause tire damage, an accident, or even injury.
Inspection
Always check the tires before operating the motorcycle. If a tire tread shows crosswise lines (minimum tread depth), if the tire has a nail or glass fragments in it, or if the side wall is cracked, replace the tire.
Minimum tire tread depth (front and rear) |
1.0 mm (0.04 in) |
WARNING: It is dangerous to ride with a worn-out tire. When a tire thread begins to show lines, replace the tire immediately.
WARNING: This motorcycle is fitted with "V" range tires (for super high speed running). The following points must be observed in order for you to make fully effective use of these tires.
1. Never fail to use "V" range tires in tire replacement. "S" or "H" tires may have a danger of bursting at super high speeds.
2. Tires have a relatively low gripping on the road surface when new, so do not allow any new ones to be subjected to load from maximum speed until after approx. 100 km (60 mi.).
3. Before any high-speed runs, remember to give a sufficient warm-up to the tires.
4. Always use the correct tire inflation pressure according to the operating conditions.
Front Forks
Front Forks
Removal and disassembly
WARNING: Securely support the motorcycle so it won't fall over when the front wheel and front forks are removed.
1. Remove the front wheel. Refer to "FRONT WHEEL"
2. Remove the windscreen assembley.
3. Remove the actuating piston housing securing bolts, and remove the actuating piston housing from the anti-dive valve assembly.
4. Remove the caliper cylinder securing bolts.
NOTE: Do not depress the brake lever when the wheel is off the motorcycle as the brake pads will be forced shut.
5. Remove the fork air valve cap and depress the valve until the air pressure escapes completely from the both forks.
6. Remove the rubber cap from the top of the fork.
NOTE: Before loosen the fork pinch bolts, loosen the fork cap bolt.
1. Rubber cap
7. Loosen the fork pinch bolts in the handle crown and under bracket.
8. Remove the damper, air joint pipe bracket and circlip.
1. Damper 2. Air joint pipe 3. Circlip
9. Slide the inner fork tube out of the handle crown and under bracket Remove the front forks.
10. Remove the dust seal with a thin screwdriver. Take care not to scratch the inner fork tube. Discard the dust seal.
11. Remove the cap bolt and fork spring.
1. Cap bolt 2. Fork spring
12. Place an open container under the fork and turn the fork upside down and drain the oil.
NOTE: Do not remove the drain bolt from outer fork tube, the cylinder securing bolt can not be removed unless the drain bolt is in place.
13. Remove the anti-dive valve assembly from the bottom of the fork.
14. Remove the cylinder securing bolt from the bottom of the outer fork tube.
15. Remove the damper rod (cylinder complete) and rebound spring.
1. Damper rod (Cylinder complete) 2. Rebound spring
16. Remove the retaining clip and back-up ring from the outer fork tube.
1. Retaining clip 2. Back-up ring
17. Hold the front fork outer tube in a vise horizontally. Put in the inner fork tube just before it bottoms out and then pull it back quickly.Repeat this step until the inner fork tube can be pulled out from the outer fork tube (usual 2 or 3 times). Then, the oil seal, seal spacer, guide bush, and slide bush all come out together, and remove the two valve springs, oil lock piece valve, and oil lock piece.
CAUTION: Don't bottom out the inner fork tube in the above step, or the oil lock piece valve and oil lock piece will be damaged.
1. Put in slowly 2. Pull back quickly
1. Slide bush 2. Guide bush 3. Seal spacer 4. Oil seal 5. Inner fork tube
Inspection
Clean and inspect all front fork components. Replace any worn or damaged components prior to reassembly.
1. Check the inner fork tube and replace if the tube is badly scratched or bent.
WARNING: Do not attempt to straighten a bent inner fork tube as this may dangerously weaken the tube.
2. Check the outer surface of the fork seal seat and outer surface of the back-up ring seat in the outer fork tube for damage. Replace the tube if for necessary.
3. Check the outer tube for dents. Replace the tube if for necessary.
4. Check the free length of the fork spring.
Fork spring free length: 522.5 mm (20.6 in)
5. Check the 0-ring of the cap bolt air joint pipe bolt, and air joint cover. Replace any damaged 0-ring.
6. Check the damper rod for wear, damage, or contamination. Blow out all oil passages with compressed air. If it is worn or damaged, replace it.
7. Check the oil lock piece valve and oil
lock piece. Replace it, if damaged.
Reassembly
NOTE: In front fork reassembly, be sure to use following new parts.
Valve spring
Guide bush
Slide bush
Oil seal
Dust seal
1. Make sure all components are clean before reassembly.
2. Install the rebound spring to the damper rod.
3. Slide the damper rod into the inner fork tube from its top.
4. Fit the two valve springs, oil lock piece valve and oil lock piece in that order over the damper rod sticking out of the inner fork tube.
1. Damper rod 2. Oil lock piece valve 3. Valve spring
4. Oil lock piece
5. Insert the inner fork tube in the outer fork tube.
NOTE: For this insertion, mate the threaded end hole of the damper rod and the hole in the outer fork tube bottom end, and also mate the lower oil passage of the four in the oil lock piece and the lowest hole in the side of the outer fork tub.
6. Apply thread-locking compound such as LOCTITE to the cylinder securing bolt and install it. Torque the bolt to specification.
Tightening torque:
23 Nm (2.3 mkg, 17 ft-lb)
7. Install the anti-dive valve housing onto the front fork and secure it with bolts. Torque the bolts to specification.
NOTE: Before installing the anti-dive valve housing, install the O-rings around the front fork oil pasages.
Tightening torque:
7 Nm (0.7 mkg, 5.1 ft-lb)
8. Install the guide bush by pressing it in with special tool. Then, install the seal spacer into the outer fork tube.
1. Guide bush
9. Apply oil to the oil seal, and install the oil seal by pressing it in with special tool. Then, install the back-up ring and retaining clip.
NOTE: Before appling oil, tape the inner tube over its groove so that the groove edge will not damage the oil seal lip.
1. Oil seal
10. Install the dust seal and fork spring.
NOTE: When installing the fork springs, the greater pitch should be at the bottom. The main fork spring has a small coil diameter at the bottom.
11. Pour the specified amount of recommended fork oil into the inner fork tube.
Fork oil capacity (each fork): 286 ± 4 cm3 (10.1 ± 0.14 Imp oz, 9.67 ± 0.14 US oz) Recommended oil:
SAE 5W type SE motor oil or equivalent
12. After filling, slowly pump the forks up and down to distribute the oil and temporarily install the cap bolt.
13. Slide the fork into the under bracket.
14. Apply a light coat of lithium soap base grease to the O-rings in the air joint bracket. Install the circlip, air joint bracket and damper over the inner fork tube.
15. Slide the fork into the handle crown in the following way.
a. Make sure the projecting portion (stopper) of the air joint bracket is positioned correctly.
b. Fit the front fork by pushing it up until its top is flush with the handle crown top end. Holding the front in this position, temporarily tighten the pinch bolts with fingers.
16. Tighten the fork pinch bolts at the handle crown and under bracket. Then, tighten the cap bolt.
Tightening torque: Handle crown: 20 Nm (2.0 mkg, 14 ff-lb) Under bracket: 23 Nm (2.3 mkg, 17 ft-lb) Cap bolt: 23 Nm (2.3 mkg, 17 ft-lb)
1 7. Fit the fork with air using a manual air pump or other pressurized air supply.
Standard air pressure: 39.2 kPa (0.4 kg/cm2, 5.7 psi)
18. Install the air valve cap.
19. Install the caliper cylinder, the actuating piston housing and the front wheel. Refer to "FRONT WHEEL".
Tightening torque: Caliper cylinder: 35 Nm (3.5 mkg, 25 ft lb) Actuating piston housing: 5 Nm (0.5 mkg, 3.6 ft-lb)
Anti-Dive system
Anti-Dive systemSystem inspection
1. Apply the front brake for a few minutes and check to see if any brake fluid leaks out of the pipe joints, the master cylinder, or the actuating piston housing.
2. Check the fork for fork oil leakage.
3. Turn the anti-dive adjusting bolt to the maximum position.
4. Compress the front forks while applying the front brake. If the front forks are compressed easily, the anti-dive system may be damaged.
Removal
1. Release the air from the front fork by pressing the air valve pin.
2. Remove the drain screw from front fork and drain the fork oil.
3. Remove the brake hose from the actuating piston housing.
1. Actuating piston housing
4. Remove the bolts securing the actuating piston housing, and remove the housing from the anti-dive valve housing.
1 Securing bolt 2. Anti-dive valve hausing
5. Remove the anti-dive adjusting bolt cover.
CAUTION: The adjusting bolt can not be removed from its seat.
1. Adjusting bolt
6. Remove the bolts securing the anti-dive valve assembly and remove the housing assembly from the front fork. Remove two O-rings from the front fork.
1. Anti-dive valve assembly 2. 0-ring
Inspection
NOTE: The anti-dive valve housing can not be disassembled so it must be replaced with a new one if the anti-dive valve malfunction is found.
1. Remove the circlip and remove the actuating piston from the actuating piston housing.
CAUTION: Do not remove the O-ring from the actuating piston.
1. Circlip 2. Actuating piston
2. Check the piston, O-ring, and cylinder for wear, cracks, rust, and/or scrathces. If any damage is found, replace the actuating piston housing assembly.
3. Check the piston separator for cracks and replace if damaged.
4. Check the spring seat rivetted portion of the adjusting bolt for damage. Replace the adjusting bolt seat assembly if damgaed.
Assembly
1. Lubricate the actuating piston with clean brake fluid, and carefully insert the piston into the actuating piston housing cylinder until the shoulder of the piston is flush with the cylinder edge.
2. Install the washer and circlip.
3. Install the separator into the actuating piston housing.
4. Install new O-rings around the front fork oil pasages.
5. Install the anti-dive valve housing onto the front fork and secure it with bolts. Torque the bolts to the specification.
Tightening torque: 7 Nm (07 rrvkg, 5.1 ft-lb)
6. Install the actuating piston housing onto the anti-dive valve housing and secure it with two bolts. Torque the bolts to the specification.
Tightening torque: 5 Nm (0.5 mkg, 3.6 ft-lb)
7. Connect the brake hose to the actuating piston housing with the union bolt and copper washers. Torque it to the specification.
Tightening torque: 26 Nm (2.6 mkg, 19 ft-lb)
8. Pour the specified amount of front fork oil into the fork inner tube.
Front fork oil capacity (each leg): 286 ± 4 cm3 (10.1 ± 0.14 imp oz,
9.67 ± 0.14 US oz) Recommended oil: SAE 5W type SE motor oil or equivalent
9. Add proper brake fluid into the brake reservoir being careful not to spill or overflow.
10. Connect the clear plastic tube of 4.5 mm (0.18 in) in inside diameter tightly to the actuating piston housing bleed screw. Put the other end of the tube into a container.
11. Slowly apply the brake lever several times. Pull in the lever. Hold the lever in the "on" position. Loosen the bleed screw. Allow the lever to travel slowly toward its limit. When the limit is reached, tighten the bleed screw. Then release the lever.
12. Repeat the above step until ail air bubbles are removed from the brake line. It may be necessary to bleed the caliper cylinder in the same manner.
NOTE: If the bleeding is difficult it may be necessary to let the brake fluid in the system stabilize for a few hours and repeat the bleeding procedure.
13. Fill the fork with air using a manual air pump or other pressurized air supply.
Standard air pressure: 39.2 kPa (0.4 kg/cm2, 5.7 psi)
14. Adjust the anti-dive adjusting bolt. See Anti-Dive Adjustment
WARNING: The anti-dive setting must be the same on both anti-dive units.
Steering Head
Steering Head
Adjustment
See Steering Head Bearings for Steering head adjustment.
Removal
1. Remove the front wheel, front forks, windscreen, handlebars and meter assembly.
2. Remove the stem bolt and steering crown.
1 Steering stem bolt
3. Remove the lock washer, top fitting nut (ring nut) and rubber damper.
1. Lock washer
1. Top fitting nut
1. Rubber damper
4. Support the steering stem (under bracket) and remove the bottom fitting nut (ring nut).
5. Remove the bearings.
Inspection
1. Wash the bearings in solvent.
2. Inspect the bearings for pitting or other damage. Replace the bearings if pitted or damaged. Replace the races when bearings are replaced.
3. Clean and inspect the bearing races. Spin the bearings by hand. If the bearings are not smooth in their operation in the races, replace bearings and races.
Reassembly
1. Grease the bearings and races with wheel bearing grease.
2. Install the steering stem (under bracket) and bearings.
3. Install the bottom fitting nut. Tighten it to approximately 10 — 12 Nm (1.0 — 1.2 mkg, 7.2 ~~ 8.7 ft-lb). Do not over tighten it. Tighten the top fitting nut.
4. Continue reassembly in the reverse of disassembly order.
5. When assembly is complete, check the steering stem by turning it from lock to lock. If there is any binding or looseness, readjust the steering stem tightness.
Steering stem bolt torque: 110Nm (11.0 m-kg, 80 ft lb)
Rear Suspension (Swingarm and Shocks)
Rear Suspension (Swingarm and Shocks)
Inspection
1. Remove the rear wheel and both shock absorbers. Grasp the swing arm and try to move it from side to side as shown. There should be no noticeable side play.
2. The swing arm is mounted on tapered bearings. Move the swing arm up and down as shown. The swing arm should move smoothly, without tightness, binding or rough spots that could indicate damaged bearings.
Adjustment
1. Measure the gap between the frame and the swing arm on the left and right sides. There should be not more than 1.6 mm (0.062 in) difference between the left and right gaps.
NOTE: It may be easier to inspect the gap with the rear wheel removed; however, such removal is not necessary.
LESS THAN 1.6 mm (0.062 in) DIFFERENCE BETWEEN A AND B GAPS.
2. If the left and right gaps differ by more than the limit [1.6 mm (0.062 in)] adjust as follows:
a. Remove the pivot shaft caps from the left and right sides of the swing arm.
b. Loosen both the left and right pivot shafts lock nuts.
c. Loosen the pivot shaft on the side of the greater swing arm/frame gap. Loosen only slightly (counterclockwise, approximately one-half turn). After loosening, tighten the opposite pivot shaft (clockwise) to 5 — 6 Nm (0.5 ~~ 0.6 m-kg, 3.6 - 4.3 ft lb).
1. Lock nut 2 Pivot shaft
d. Measure the gap again between the frame and the swing arm. If the left and right gaps are not within 1.6 mm (0.062 in) of each other, repeat step. c.
e. When the left and right gaps are adjusted properly, tighten the pivot shaft lock nut.
NOTE: Do not allow the pivot shaft to turn while tightening the lock nut
Pivot shaft lock nut torque: 100 Nm (10 mkg, 72 ft lb).
Removal
1. Remove the middle gear flange holding bolts.
2. Remove the rear wheel and shock absorbers. Remove the rear brake assembly.
3. Remove the final gear assembly.
4. Remove the swing arm pivot caps, the pivot shafts and the swing arm.
Inspection and lubrication
1. Remove the oil seals and the bearings. Inspect the bearings for pitting or other damage. Make sure that the bearings roll freely. If a bearing is damaged, both bearings and both sets of inner and outer bearing races should be replaced.
CAUTION: Do not use compressed air to spin the bearings dry. This causes damage to the bearing surfaces.
NOTE: When installing new bearings, grease liberally with lithium base, waterproof wheel bearing grease.
2. Always replace the grease seals when bearings are removed.
3. Examine the rubber boot for damage. Replace if damaged.
Installation
Installation of the swing arm can be accomplished by reversing the removal procedure. Observe adjustment procedures for obtaining equal frame/swing arm spacing.
CAUTION: A lock washer for left side pivot bolt must be replaced with a new one and the tab should be bent over along the bolt flat after tightening.
REAR SHOCK ABSORBER ("DE CARBON" SYSTEM) Handling notes
WARNING: This shock absorbers are provided with a separate type tank filled with high-pressure nitrogen gas. To prevent the danger of explosion, read and understand the following information before handling the shock absorbers.
The manufacturer can not be held responsible for property damage or personal injury that may result from improper handling.
1. Never tamper or attempt to disassemble the cylinder or the tank.
2. Never throw the shock absorber into an open flame or other hight heat. The shock absorber may explode as a result of nitrogen gas expansion and/ or damage to the unit.
3. Be careful not to damage any part of the gas tank. A damaged gas tank will impair the damping performance or cause a malfunction.
4. Take care not to scratch the contact surface of the pistion rod with the cylinder; or oil could leak out.
5. When scrapping the shock absorber, follow the instructions on disposal.
Notes on disposal
Before disposing the shock absorber, be sure to extract the nitogen gas. To do so, drill a 2 — 3 mm (0.08 ~ 0.12 in) hole through the tank at a position 25 ~~ 30 mm (1.0 — 1.2 in) from the bottom end of the tank. At this time, wear eye protection to prevent eye damage from escaping gas and/or metal chips.
Removal and reinstallation
1. Remove the seat and side covers (Left and right).
2. Remove the rear stay and rear fairing.
3. Remove the muffler securing bolts and remove the mufflers.
4. Remove the rear shock absorber mounting nuts and standing handle securing bolt. Then, pull out the rear shock absorber from the frame.
5. For reinstallation, reverse the procedure for removal. When installing, observe the specified tightening torque.
Upper (Left and right sides): 30 Nm (3.0 nrvkg. 22 ft-lb)
Bottom (Left and right sides): 30 Nm (3.0 mkg. 22 ft-lb)
Rear stay: 23 Nm (2.3 mkg. 17 ft lb)
Inspection
1. Check the rod. If it is bent or damaged, replace the shock absorber.
2. Check for oil leakage. If oil leakage is evident replace the shock absorber.
3. Operate shock absorber rod to check damping. There should be not noticeable damping as the shock extends.
Cable and Fittings
Cable and FittingsCable maintenance
NOTE: See Maintenance and Lubrication intervals charts. Cable maintenance is primarily concerned with preventing deterioration through rust and weathering and providing proper lubrication to allow the cable to move freely within its housing.
WARNING: Cable routing is very important. For details of cable routing, see the cable routing diagrams at the end of this manual. Improperly routed or adjusted cables may make the motorcycle unsafe for operation.
1. Remove the cable.
2. Check for free movement of cable within its housing. If movement is obstruced, check for fraying or kinking of the cable strands. If damage is evident, replace the cable assembly.
3. To lubricate the cable, hold it in a vertical position. Apply lubricant to the uppermost end of cable. Leave it in the vertical position until lubricant appears at the bottom. Allow any excess to drain and reinstall the cable.
NOTE: Choice of lubricant depends upon conditions and preferences. However, a semi-drying chain and cable lubricant will perform adequately under most conditions.
Throttle maintenance
1. Remove the Phillips head screws from throttle housing assembly and separate the two halves of housing.
2. Disconnect the cable end from the throttle grip assembly and remove the grip assembly.
3. Wash all parts in a mild solvent and check all contact surfaces for burrs or other damage. (Also clean and inspect right-hand end of the handlebar.)
4. Lubricate all contact surfaces with a light coat of lithium soap base grease and reassemble.
NOTE: Tighten the housing screws evenly to maintain an even gap between the two halves.
5. Check for smooth throttle operation and quick spring return when released and make certain that the housing does not rotate on the handlebar.
Shaft Drive
Shaft DriveSpecial Tools and Troubleshooting
Special Tools and TroubleshootingThe following special tools are not available but can be constructed for the final gear disassembly and assembly:
PRESS TOOL NO. 1
PRESS TOOL NO. 2
GEAR CASE HOLDING TOOL
Troubleshooting
1. The following conditions may indicate damaged shaft drive components:
Symptoms |
Possible damaged areas |
1. A pronounced hesitation or "jerky" movement during acceleration, deceleration, or sustained speed. (This must not be confused with engine surging or transmission characteries). |
A. Damage to bearings. |
B. Improper gear lash. |
|
C. Gear tooth damage. |
|
2. A "rolling rumble" noticeable at low speed; a high-pitched whine; a "clunk" from a shaft drive component or area. |
D. Drive flange/universal joint bolts loose. |
3. A locked-up condition of the shaft drive mechanism; no power transmitted from engine to rear wheel. |
E. Broken drive-shaft. |
F. Disconnected flange/universal joint connection. |
|
G. Broken gear teeth. |
|
H. Seizure due to lack of lubrication. |
|
I. Small foreign object lodged between moving parts. |
NOTE: Damage areas A, B, and C above may be extremely difficult to diagnose. The symptoms are quite subtle and difficult to distinguish from normal motorcycle operating noise. If there is reason to believe component(s) are damaged, remove component(s) for specific inspection.
2. Inspection notes
a. During coasting, accelerating or decelerating, the "rolling rumble" will increase with rear wheel speed, not engine or transmission gear speeds. However, such noise may also be due to wheel bearings.
b. Noise that varies with acceleration and deceleration: Following incorrect reassembly, a condition of too-little gear lash may produce a whine during deceleration.
CAUTION: Too-little gear lash is extremely destructive to gear teeth. If a test ride following reassembly indicates this condition, stop riding immediately to minimize damage to gears.
c. A slight "thunk" must be distinguished from normal motorcycle operation. It will be most noticeable at low speed and could indicate broken gear teeth.
WARNING: If broken gear teeth are suspected, stop riding immediately. This condition could lead to locking-up of the shaft drive assembly and result in harm to a rider.
d. If the drive flange/universal joint bolts are slightly loose, a "clunk" may be felt when slowly taking off, or when changing from slow acceleration to slow decelration. At high speed this will result in vibration.
WARNING: Do not continue riding a motorcycle suspected of having loose flange/universal joint bolts. The components may break, causing injury to a rider.
3. Troubleshooting chart
Where Basic Conditions "a" and "b" above exist, consider the following chart:
Elevate and spin front wheel. Feel for wheel bearing damage. |
Yes |
Replace wheel bearing. (See CHAPTER 5 "FRONT WHEEL") |
I No |
||
Check rear wheel. Feel for bearing damage. |
No |
Rear wheel bear-inbgs and shaft drive bearings probably not damaged. Repeat test or remove individual components. |
Yes |
||
Remove rear wheel. Check for wheel bearing damage. |
Yes |
Repelace rear wheel bearing. (See "REAR WHEEL" section in this chapter.) |
No |
||
Remove drive shaft components. |
4. Oil leak inspection
If a shaft drive component is suspected of leaking oil, first thoroughly clean the entire motorcycle. The spparent location of an oil leak on a dusty motorcycle may be misleading. Dry the motorcycle and apply a leak-localizing compound or a dry-powder spray that will limit the flow of any leaking oil. Operate the motorcycle prepared in this way for the distance necessary to precisely locate the leak. There are the possibilities that a component housing may have been damaged by road debris or an accident, or a gasket or seal may be cracked or broken. However, on new or nearly new motorcycle an apparent oil leak may be the result of a rust-preventive coating or excess assembly lubrication of seals. Always clean the motorcycle and recheck the suspected location of any apparent leakage.
5. Checking drained oil
Whenever a problem is suspected in either the middle or final gear assemblies, drain and inspect the oil. Metal particles on the drain plug or in the oil could indicate a bearing seizure or other problem in the component. However, a small amount of metal particles in the oil is normal.
Final gear Removal and adjustment
Final gear Removal and adjustment
Final gear removal
1. Remove the rear axle and left shock absorber. Remove the rear wheel (see "REAR WHEEL" section in this chapter).
2. Remove the 4 nuts holding the final drive unit to the swing arm.
3. Remove the final gear assembly.
4. Remove the circlips, plate washer and oil seal. Then pull out the drive shaft.
1. Circlip 2. Plate washer 3. Oil seal 4. Drive shaft
Gear lash check and adjustment
1. Secure the gear case in a vice or other support.
2. Remove the drain plug from the final gear case. Then, install a specified size of bolt (as shown) into the drain plug hole. Finger-tighten the bolt until it holds the ring gear.
NOTE: The bolt should not be over tightened, finger tight is sufficient.
3. Install the final gear lash measurement tool on the gear coupling.
1. Gear lash measurement tool (Final gear)
4. Mount a dial gauge against the lash measurement tool at the scribed mark (60 mm (2.36 in) from the center of the shaft).
5. Use the special wrench to gently rotate the gear coupling back and forth. Note the lash measurement on the dial gauge.
Final gear lash: 0.25 — 0.50 mm (0.010 — 0.020 in) When using the measurement tool. 0.1 — 0.2 mm (0.004 — 0.008 in) Actual gear lash on the final gear teeth
1. Middle and final gear noising tool
6. If the gear lash exceeds the specified limits, adjust as follows.
a. To reduce gear lash, increase the ring gear shim.
b. To increase gear lash, reduce ring gear shim.
1. Ring gear shlim
c. If it is necessary to increase the ring gear shim by more than 0.1 mm (0.004 in) reduce the thrust washer thickness by 0.1 mm (0.004 in) for each 0.1 mm (0.004 in) of ring gear shim increase and if it is necessary to reduce shim by more than 0.1 mm (0.004 in), reverse above procedure.
Final gear Disassembly and Reassembly
Final gear Disassembly and ReassemblyFinal gear disassembly
1. Remove the nuts and bolts holding the bearing housing.
2. Remove the ring gear assembly and thrust washer from the final gear case.
3. Remove the self-locking nut from drive pinion by using the holding tool (special tool) and remove the coupling.
1. Middle and final gear holding tool
4. Remove the drive pinion bearing retainer with the retainer remover (special tool).
CAUTION: The drive pinion bearing retainer nut is left hand threads. Turn the retainer nut clockwise to loosen.
1. Drive pinion bearing retainer remover
5. Remove the drive pinion and bearing with the slide hammer and adapter (special tool).
CAUTION: This drive pinion removal should be performed only if gearing replacement is necessary. Do not re-use bearings or races after removal.
1. Slide hammer 2. Crank installer adapter
6. Remove the guide coller, oil seal, and roller bearing from the main housing by using the press tool No. 1 (special tool) and a press. Use an appropriate supports for the main housing during this operation. The roller bearing may be reused if undamaged. Do not re-use oil seal.
7. Rear drive pinion roller bearing; removal of this bearing is difficult and seldom necessary. Heat the bare housing to 150°C (302°F). Use an appropriately shaped punch to remove the roller bearing outer race. Remove the inner race from the drive pinion-
Final gear reassembly
1. Install the new rear drive pinion roller bearing. Heat the bare bearing to 150°C (302°F) and use an appropriately adapter to install the roller bearing outer race. Install the inner race onto the drive pinion.
2. Using the press tool No. 2 (special tool) and a press, install the guide coller, new oil seal, and roller bearing into the main housing in that order.
NOTE: The removed roller bearing can be used if undamaged; however, we recommend replacement with a new one.
3. Final drive/ring gear positioning
NOTE: When the following part(s) is replaced with new one(s), gear positioning is necessary:
a. Final gear
b. Ring gear bearing housing
c. Bearing(s)
a. The shim thickness "A" necessary for the drive pinion gear positioning can be calculated from the informations found on the final gear case and on the drive gear end.
To fined shim thickness "A" use the formula:
A = a - b
Where: a =a numeral (usually a decimal number) on the gear near the tooth and either added to or detracted from the nominal size "84". b =a numeral on the gear case appearing as a whole figure (ie. 83.50).
Example:
1) If the pinion gear is marked "+01" ....: "a" is 84.01.
2) If the gear case is marked "83.50".
A = 84.01 - 83.50
A = 0.51
Then the necessary shim thickness is 0.51 mm.
Shim sizes are supplied in the following thicknesses:
0.15 mm, 0.30 mm, 0.40 mm, 0.50 mm, 0.60 mm.
Because the shims can only be selected in 0.05 mm increments the following
chart should be used when encountering last digits that are not 5 or zero (0):
Last digits |
Rounding |
0, 1.2 |
0 |
3, 4, 5, 6. 7 |
5 |
8, 9 |
10 |
Shim thickness: 0.50 mm
b. The shim thickness "B" necessary for the ring gear positioning can be calculated from the informations found on the final gear case, ring gear, and bearing.
To find shim thickness "B" use the formula:
B = c + d-(e + f)
Where:
c = a numeral on the gear case appearing as a whole figure (ie. 45.52)
d = a numeral (usually a decimal number) on the outside of the ring gear bearing housing and added to the nominal size "3".
e = a numeral (usually a decimal number) on the inside of the ring gear and; either added to or detracted from the nominal size "35.40".
f = a bearing thickness (considered constant)
Distance "f" = 13.00 mm
Example:
1) If the gear case is marked "45.52".
2) If the ring gear bearing housing is marked "35"....."d" is 3.35.
3) If the ring gear is marked "+01" .....
"e" is 35.40 + 0.01 = 35.41.
4) "f" is 13.00.
B = c + d-(e + f)
B = 45.52 + 3.35 - (35.41 + 13.00)
8 = 48.87 - (48.41)
B = 0.46
Then the necessary shim thickness is 0.41 mm.
NOTE: Use the chart for the drive pinion shim to select the ring gear shim size.
Shim thickness: 0.40 mm
4. Install the drive pinion gear with the proper size of shim(s) and secure it with the bearing retainer nut with the drive pinion bearing retainer remover (special tool).
NOTE: The bearing retainer nut is left hand threads;
turn the nut to counterclockwise to tighten.
Tightening torque: 110 Nm (11.0 mkg, 80 ftlb)
5. Install the ring gear assembly without the thrust washer. Adjust the gear lash (refer to "Gear lash check and adjustment").
6. Place four pieces of "PLASTIGAGE" between the originally fitted thrust washer and ring gear.
7. Install the gear case onto the ring gear assembly and tighten the nuts and bolts with the specified torque.
Tightening torque:
Bolt/Nut: 23 Nm (2.3 mkg, 17 ftlb)
NOTE: Do not turn the drive pinion/ring gear when measuring clearance with "PLASTIGAGE".
8. Remove the ring gear assembly and determine the clearance by measuring the width of the flattened "PLASTIGAGE".
Ring gear thrust clearance:
0.1 - 0.2 mm (0.004 - 0.0078 in)
1. PLASTIGAGE
9. If the clearance exceeds the specification above, replace the thrust washer to obtain the proper clearance.
Drive Shaft / Joint
Drive Shaft / Joint
Removal
1. Remove the rear wheel.
2. Remove the final gear case assembly.
3. Remove the drive shaft.
4. To remove the universal joint, it is necessary to remove the swing arm. Remove the universal joint assembly.
Inspection
1. Drive shaft
Inspect the shaft splines for wear and/or damage. If excessive, replace the drive shaft
NOTE: When installing the drive shaft lubricate splines with molybdenum disulfied grease.
2. Universal joint
a. There should be no noticeable play in the universal joint bearings. If there is any play in the bearing, replace the universal joint assembly.
b. Move the universal joint up and down and from side to side. The universal joint should move smoothly. Without tightness, binding or rough spots that could indicate damaged bearings. If damaged, replace the universal joint assembly.
Reinstallation
When installing the drive shaft and the universal joint reverse the removal procedure. Note the following points:
1. Lubricate the shaft splines with molybdenum disulfied grease.
2. Tighten the universal joint securing bolts and final gear case securing nuts with the specified torque:
Final gear case:
42 Nm (4.2 mkg, 30 ft lb) Universal joint:
44 Nm (4.4 mkg, 32 ft-lb)
Chapter 6. Electrical
Chapter 6. ElectricalElectrical Components
Electrical Components
ELECTRICAL COMPONENTS
Wiring Diagram
Wiring DiagramXJ900RL CIRCUIT DIAGRAM
1 | Main switch | 21 | Neutral switch | 41 | Tachometer |
2 | Handlebar switch (Right) | 22 | Rear brake switch | 42 | Over revolution switch |
3 | "LIGHT" switch | 23 | Flasher relay | 43 | Reed switch |
4. | "ENGINE STOP" switch | 24 | Cancelling unit | 44 | Digital clock |
5. | "START" switch | 25 | Rectifier with regulator | 45 | "NEUTRAL" indicator light |
B | Front brake switch | 26 | A C Generator | 46 | "OIL" indicator light |
7 | Fuel sender | 27 | Oil level switch | 47. | "HIGH BEAM" indicator light |
B | Fuse box | 28 | Clutch switch | 48 | Horn |
B | Diode | 29 | Handebar switch (Left) | 49 | Front flasher light (Right) |
10 | Starting-circuit cut-off relay | 30 | "TURN" switch | ||
11. | Rear flasher light (Right) | 31 | 'HORN' switch | ||
12 | Rear flasher light (Left) | 32 | Passing light switch "PASS" | ||
13 | Tail/brake light | 33 | "LIGHTS" (Dimmer) switch | ||
14. | Battery | 34 | Front flasher light (Left) | ||
15 | Starter relay | 35 | Auxilary light | ||
16 | Starter motor | 36 | Headlight | ||
17 | Spark plug | 37 | Meter assembly | ||
18 | Ignition coil | 38 | Meter light | ||
19. | Ignitor | 39 | "TURN" indicator light | ||
20 | Pick-up coil | 40 | Fuel meter |
COLOR CODE
Br | Brown | Y | Yellow | L | Blue |
R | Red | Dg | Dark Green | P | Pink |
W | White | Ch | Chocolate | 0 | Orange |
B | Black | Sb | Sky Blue | G | Green |
Y/B | Yellow/Black | Y/R | Yellow/Red | E | Ground |
Br/W | Brown/White | R/W | Red/White | B/R | Black/Red |
Y/G | Yellow/Green | L/R | Blue/Red | Gy | Grey |
W/G | White/Green | R/Y | Red/Yellow | G/Y | Green/Yellow |
L/W | Blue/White | W/G | White/Green | B/Y | Black/Yellow |
Electric Starting System
Electric Starting SystemCircuit diagram
Starter motor
1. Removal
See Engine Dissassembly, Starter and Generator.
2. Inspection and repair
a. Check the outer surface of the commutator. If its surface is dirty, clean with # 600 grit sand paper.
b. The mica insulation between commutator segments should be 0.4 — 0.8 mrn (0.02 — 0.03in) below the segment level. If not, scrape to proper limits with appropriately shaped tool. (A hack saw blade can be ground to fit.)
NOTE: Mica insulation of commutator must be undercut to ensure proper operation of commutator.
c. The starter's armature coil should be checked with an ohm meter for insulation breakdown (shorting to each other or to ground) and for continuity. Reference figure is given below.
Coil resistanec: Armature coil: 0.014 Ω ± 6 % at 20°C (68°F)
d. Check the front and rear cover bearings for damage. If damaged, the starter assembly must be replaced.
e. Check brush length. Replace brush if at or near, limits.
Minimum brush length: 8.5 mm (0.33 in)
f. Check brush spring pressure. Compare it with a new spring. Replace the old spring if it is weak.
Starter relay
1. Inspection
a. Disconnect starter relay leads at the relay.
b. Connect pocket tester leads to the relay terminals (ohms x 1 scale).
c. Turn ignition to "ON" position, engine stop switch to "RUN" and change lever to "NEUTRAL".
d. Push the starter switch. The relay should click once and the scale should read zero if it does not read zero, the relay must be replaced.
1 Battery lead (+) 2. Starter motor lead
e. If the relay does not click, check the leads from the starter switch and from the battery (white/red, blue/white). Turn the ignition off. Use (ohms x 1) scale on tester. The resistance between these leads should be no more than 3.4 ohms. If there is more resistance, the relay should be replaced.
1 Blue/White 2 White/Red
Starting-circuit cut-off relay
1. Inspection
a. Remove the seat.
b. Remove the starting-circuit cut-off relay from the electrical components holding plate, and disconnect the connector.
1 Starting-circuit cut-off relay
c. Check the resistance of the relay coil windings with the pocket tester. If the resistance is not within specification, replace the relay.
d. Check the relay function with a 12 volt battery and the pocket tester. Connect the leads as shown in the illustration. If the resistance readings do not equal those shown in the illustration, replace the relay.
Neutral switch
Diode
1. Inspection
a. Remove the seat.
b. Remove the diode from the electrical components holding plate, and disconnect the connector.
c. Check the resistance of the diode with the pocket poster as shown in the illustration. If the resistance is not specification, replace the diode.
NOTE: Only the Yamaha Pocket Tester will give a 9.5 Ωreading when testing continuity. The particular characteristics of other testers will vary the continuity test readings.
1. Inspection
a. Remove the seat.
b. Disconnect the 4-pin connector from the main wire harness.
c. Connect the pocket tester leads as shown, and set the tester selector to ohm x 1.
When the transmission is in neutral, the tester should read zero ohms. When the transmission is in gear, the tester should read infinity.
1. Neutral 2 In gear 3. Sky blue 4 Ground
Clutch switch
1. Inspection
a. Remove the seat.
b. Disconnect the 4-pin connector from the main wire harness.
c. Connect the pocket tester leads as shown, and set the tester slector to ohm x 1.
When the clutch is disengaged, the tester should read zero ohms. When the clutch is engaged, the tester should read infinity.
1. Disengaged 2. Engaged 3. Black/Yellow 4. Ground
Charging System
Charging SystemCircuit diagram
A. C. Generator
1. Checking method
a. Connect D. C. voltmeter to the battery terminals.
b. Start the engine.
c. Accelerate engine to approximately 2,000 r/min or more and check generated voltage,
Generated voltage:
14.5 ± 0.3 V at 20°C (68°F)
1 Battery
d. If the indicated voltage cannot be reached, then perform the tests in step 2.
CAUTION: Never disconnect leads from the battery while the generator is in operation. If the battery is disconnected, the voltage across the generator terminals will increase, damaging the semiconductors.
2. Resistance test of field coil and stator coil
a. Remove the seat. Disconnect the 2-pin connector and 3-pin connector from the A. C. Generator.
b. Check the resistance between terminals. If resistance is out of specification, coil is broken. Check the coil connections. If the coil connections are good, then the coil is broken inside and it should be replaced.
Field coil resistance (Green-Brown): 4.0 Ω ± 10 % at 20°C (68°F)
Stator coil resistance (White-White): 0.46 Ω ± 10 % at 20°C (68°F)
1 Brown 2. Green
1. White 2. White
Voltage regulator
The AC Voltage Regulator is a small and, normally, very reliable component. Due to its construction, it is lightweight and free from the wear and misadjustment associated with mechanical voltage regulators. If the following inspection reveals that the regulator is faulty, it cannot be adjusted and must be replaced.
1. Rectifier with regulator
1. Checking AC Voltage regulator
a. Remove the seat.
b. Remove the left side cover.
c. Measure the specific gravity of the battery fluid. If it is less than 1.260, remove the battery and recharge until it is more than 1.260.
d. Check the battery terminals and couplers for looseness.
e. Connect two Yamaha pocket testers to the regulator coupler as illustrated.
CAUTION: Be careful not to let the tester leads short circuit when connecting them to the regulator snap connector leads.
f. Turn the main switch on. Make sure that V2 is less than 1.8V.
NOTE: Do not turn on lights or signals.
g. Make sure that V2 gradually increases up to 9 - 11V when the engine is started and its revolutions go up.
h. Make sure that V, maintains the level of 14.2 — 14.8 V even when engine revolutions increase.
i. If these levels are not maintained, the regulator is defective and must be replaced.
2. Checking the silicon rectifier
a. Check the silicon rectifier as specified using the Yamaha pocket tester.
Checking element |
Pocket tester connecting point |
Good |
Shorted |
Open |
|
(+) (red) | (-)
(black) |
||||
D, |
d | a | O | O | X |
a | d | x | 0 | X | |
D2 |
d | b | O | o | X |
b | d | X | o | X | |
D3 |
d | c | O | o | X |
c | d | X | o | X | |
D4 |
a | e | O | o | X |
e | a | X | 0 | X | |
D5 |
b | e | O | o | X |
e | b | X | o | X | |
D6 |
c | e | O | o | X |
e | c | X | o | X |
O: Continuity
x: Discontinuity (∞)
b. Even if only one of the elements is broken, replace the entire assembly.
CAUTION: The silicon rectifier can be damaged if subjected to overcharging. Special care should be taken to avoid a short circuit and/or incorrect connection of the positive and negative leads at the battery. Never connect the rectifier directly to the battery to make a continuity check.
Ignition System
Ignition SystemCircuit diagram
Description
This model is equipped with a battery operated, fully transistorized breakerless ignition system. By using magnetic pick-up coils the need for contact breaker points is eliminated. This adds to the dependability of the system by eliminating frequent cleaning and adjustment of points and ignition timing. This T. C. I. (Transistor Control Ignition) unit in corporates an automatic advance circuit controlled by signals generated by the pick-up coil. This adds to the dependability of the system by eliminatng the mechanical advancer. This T. C. I. system consists of two main units; a pick-up unit and ignitor unit.
Operation
The T. C. I. functions on the same principle as a conventional D. C. ignition system with the exception of using magnetic pick-up coils and a transistor control box (T. C. I.) in place of contact breaker points.
1. Pick-up unit
1 Pick-up coils
This unit consists of two pick-up coils and a magneto mounted on the crank-case (L. H.). When the reluctor (timing plate) projection passes the pick-up coil, the two signals are generated at the pick-up coil and transmited to the ignitor unit as a signal. The full ignition advance is determined by the width of the reluctor (timing plate) projection.
2. Ignitor unit
1 Ignitor unit (T.C.I, unit)
This unit has such functions of wave form, duty control, switching, electrical ignition advance, and etc. The ignition timing is advanced electrically using two signals from the pick-up coil. The duty control circuit is provided to control the on time period of the primary ignition current to reduce the electrical consumption. This unit also incorporates a protective circuit for the ignition coil. If the ignition switch is turned on and the crankshaft is not turned, the protective circuit stops current flow to the primary coil within a few seconds. When the crankshaft is turned over, the current is turned on again by the signals generated by the pick-up coils.
CAUTION: Do not run the engine without any spark plug cap(s) in place. Due to the high secondary voltage, it is possible to damage the internal insulation of the secondary coil.
Inspection
The entire ignition system can be checked for misfire and weak spark using the Electro Tester. If the ignition system will fire across a sufficient gap, the entire ignition system can be considered good. If not, proceed with individual component tests until the problem is found. 1. Warm up engine thoroughly so that all electrical components are at operating temperature.
2. Stop the engine and connect the tester as shown.
3. Start the engine and increase the spark gap until misfire occurs. (Test at various r/min between idle and red line.)
Minimum spark gap: 6 mm (0.24 in)
CAUTION: Do not run engine in neutral above 6,000 r/ min for more than 1 or 2 seconds.
Troubleshooting Chart
Check entire ignition connections. |
Poor connection ► |
Correct.
|
▼ OK |
||
Check battery voltage and specific gravity. |
Low voltage/specific gravity ► |
Recharge battery.
|
▼ OK |
||
Check fuse and fuse connections. |
Weak connection or open circuit ► |
Correct connection or replace fuse.
|
▼ OK |
||
Check ignition coil resistance (primary and secondary).
Primary: 2.7Ω ± 10%@20°C (68°F) Secondary: 13.2KΩ ± 20%@20°C (68° F) |
If other than specified ► |
Replace ignition coil.
|
▼ OK |
If other than specified ► |
Replace pickup coil assembly.
|
Check pickup coil resistance. Pickup coil: 120Ω ± 10% at 20°C (68°F) |
||
▼ OK |
||
Check operation of sidestand switch (if fitted) and relay. |
Faulty ► |
Check sidestand relay sidestand switch, diode and neutral switch.
|
▼ OK |
||
TCI unit is faulty, replace unit. |
Ignition coil
1. Coil spark gap test.
a. Remove the fuel tank and disconnect the ignition coil from wire harness and spark plugs.
b. Connect the Electro Tester as shown.
CAUTION: When testing twin secondary lead coils, one lead must always be grounded and the other lead may not exceed the maximum spark gap because the insulation on the secondary windings may be destroyed by the overly high voltages that can be generated.
c. Connect fully charged battery to tester.
d. Turn on spark gap switch and the increase gap to maximum unless misfire occurs first.
Minimum spark gap: 6 mm (0.24 in)
2. Direct current resistance test
Use a pocket tester or equivalent ohm-meter to determine resistance and continuity of primary and secondary coil windings.
Primary coil resistance:
2.7 Ω ± 10% at 20°C (68°F) Secondary coil resistance:
13.2 KΩ ± 20 % at 20°C (68°F)
Pick-up coil
1. Inspection
a. Remover the seat.
b. Disconnect the pick-up coil leads from the ignitor unit.
c. Check the resistance of the pick-up coil windings with the pocket tester. If the resistance is not within specification, replace the pick-up coil assembly.
Pick-up coil resistance:
1 20 Ω ± 10 % at 20°C (68°F)
1 Black 2 Orange 3 Brown
Spark plug
The life of a spark plug and its discoloring vary according to the habits of the rider. At each periodic inspection, replace burned or fouled plugs with new ones of the specified type. It is actually economical to install new plugs often since it will tend to keep the engine in good condition and prevent excessive fuel consumption.
1. Inspection
a. Inspect and clean at the specified intervals and replace as required.
b. Clean the electrodes of carbon and adjust the electrode gap to the specification.
2. Installation
Be sure to use the proper reach, type and electrode gap plug(s) as a replacement to avoid overheating, fouling or piston damage.
Type: BPR8ES (NGK) Electrode gap:
0.7 — 0.8 mm (0.028 — 0.031 in) Tightening torque:
20 Nm (2.0 mkg, 14ft-b)
Lighting System
Lighting SystemCircuit diagram
Lighting system tests and checks
The battery provides power for operation of the headlight, taillight, and meter lights. If none of the above operates, always check battery voltage before proceeding further. Low battery voltage indicates either a faulty battery, low battery electrolyte, or a defective charging system. See page 6-9 "CHARGING SYSTEM" for checks of battery and charging system. Also check fuse condition. Replace any "open" fuses. There are individual fuses for various circuits (see complete Circuit Diagram).
NOTE: Check the headlight bulb first before performing the following check.
1. Headlight does not come on. (High and/or low beam)
Check for voltage (12V) on "R/Y" lead at "LIGHTS" switch connector. |
No voltage |
Check wiring circuit from fuse to "LIGHTS" switch connector. |
Voltage OK ▼ |
||
Check for voltage (12V) on "L/B" lead at "LIGHTS" (Dimmer) switch connector. |
No voltage |
Check "LIGHTS'* switch and wiring circuit from "LIGHTS" switch to "LIGHTS" (Dimmer) switch connector. |
Voltage OK ▼ |
||
Check for voltage (12V) on "Y" or "G" leads at headlight bulb socket. |
No voltage |
"LIGHTS" (Dimmer) switch and/or wiring circuit from "LIGHTS" (Dimmer) switch to headlight bulb socket is faulty Repair. |
2. Taillight does not come on.
When the "LIGHTS" switch is "PO" or "ON" and the main switch is "ON" or "P" positions.
Check for voltage (12V) on "L" lead at "LIGHTS" switch connector |
No voltage ► |
|
Voltage OK ▼ | ||
Check for voltage (12V) on "L" lead at main switch connector. |
No voltage |
Wiring circuit from "LIGHTS" switch to main switch connector is faulty, repair. |
Voltage OK ▼ | ||
Check for voltage (12V) on "L/R" lead at main switch connector. |
No voltage |
Main switch is faulty, replace |
Voltage OK ▼ |
||
Check for voltage (12V) on "L" lead at taillight bulb socket. |
No voltage |
Wiring circuit from main switch to taillight bulb socket is faulty. repair. |
3. Auxiliary light does not come on.
When the "LIGHTS" switch is "PO" or "ON" and the main switch is "ON" or "P" position.
Check for voltage (12V) on "L" lead at "LIGHTS" switch connector. |
No voltage |
"LIGHTS" switch is faulty, replace. |
Voltage OK ▼ | ||
Check for voltage (12V) on "L" lead at main switch connector. |
No voltage |
Wiring circuit from "LIGHTS" switch to main switch connector is faulty, repair. |
Voltage OK ▼ | ||
Check for voltage (12V) on "L/R" lead at main switch connector. |
No voltage |
Main switch is faulty, replace. |
Voltage OK ▼ | ||
Check for voltage (12V) on "L/R" lead at auxiliary light bulb socket. |
No voltage |
Wiring circuit from main switch to auxiliary light bulb socket is faulty, repair. |
Signal System
Signal SystemSIGNAL SYSTEM Circuit diagram
Signal system tests and checks
The battery provides power for operation of the horn, brakelight, indicator lights and flasher light. If none of the above operates, always check battery voltage before proceeding further. Low battery voltage indicates either a faulty battery, low battery water or a defective charging system. See page 6-9 "CHARGING SYSTEM" for checks of battery and charging system. Also check fuse condition. Replace any "open" fuses. There are individual fuses for various circuits (see complete Circuit Diagram).
1. Horn does not work
Check for voltage (12V) on "Br" lead at horn terminal. |
No voltage ► |
Check wiring circuit from fuse to horn terminal. |
Voltage OK ▼ |
||
Check for voltage on "P" lead at "HORN" switch connector. |
No voltage ► |
Wiring circuit from horn to "HORN" switch is faulty, repair. |
Voltage OK ▼ |
||
Check for continuity of "HORN" switch. |
No continuity |
"HORN" switch is faulty, replace. |
Continuity ▼ |
||
Adjust horn, replace if damaged. |
2. Brake light does not work a. Front brake
Check for voltage (12V) on "Br" Lead at front brake switch connector |
No voltage |
Check wiring circuit from fuse to brake switch connector. |
Voltage OK ▼ |
||
Check for voltage (12V) on "Gy" lead at front brake switch connector while applying brake. |
No voltage |
Front brake switch is faulty, replace |
Voltage OK ▼ |
||
Check for voltage (12V) on "Y" lead at brake light bulb socket while applying brake. |
No voltage |
Wiring circuit from brake switch to Brake light bulb socket is faulty, repair. |
b. Rear brake
Check for voltage (12V) on "Br" lead at rear brake switch connector. |
No voltage |
Check wiring circuit from fuse to brake switch connector. |
Voltage OK ▼ |
||
Check for voltage (12V) on "Y" lead at rear switch connector while applying brake. |
No voltage |
Rear brake switch is faulty or maladjustment, replace or adjust. |
Voltage OK ▼ |
||
Check for voltage (12V) on "Y" lead at brake light bulb socket while applying brake, |
No voltage |
Wiring circuit from brake switch to brake light bulb socket is faulty, repair. |
3. Flasher lights (left and/or right) do not work
Check for voltage (12V) on "Br" lead at flasher relay terminal. |
No voltage |
Check wiring circuit from fuse to flasher relay terminal. |
Voltage OK ▼ |
||
Check for voltage (12V) on "Br/W" lead at flasher relay terminal. |
No voltage |
Flasher relay is faulty, replace. |
Voltage OK ▼ |
||
Check for voltage (12V) on "Br/W" lead at "TURN" switch connector. |
No voltage |
Wiring circuit from flasher relay to "TURN" switch is faulty, repair. |
Voltage OK ▼ |
||
Check for voltage (12V) on "Ch" and/or "Dg" lead at "TURN" switch connector. |
No voltage |
"TURN" switch is faulty, replace. |
Voltage OK ▼ |
||
Check for voltage (12V) at left and/or right flasher (front and/or left bulb socket. |
No voltage |
Wiring circuit from "TURN" switch to flasher bulb is faulty, repair. |
Self-cancelling flasher system
1. Description
The self-cancelling flasher system turns off the turn signal after a period of time or distance involved in turning or changing lanes. Generally, the signal will cancel after either 10 seconds, or 150 meters (490 feet), whichever is greater. At very low speed, the function is determined by distance; at high speed, especially when changing speeds the cancelling determination is a combination of both times and distance.
2. Operation
The handlebar switch has three positions:
L (left), OFF, and R (right). The switch lever will return to the "OFF" position after being pushed to L or R, but the signal will function. By pushing the lever in, the signal may be cancelled manually.
3. Inspection
If the flasher self-cancelling system should become inoperative, proceed as follows: a. Pull of the 6-pin connector from the flasher cancelling unit, and operate the handlebar switch.
If the signal operates normally in L, R, and OFF, the following are in good condition.
1) Flasher relay
2) Bulb
3) Lighting circuit
4) Handlebar switch light circuit
If 1) through 4) are in good condition, the following may be faulty:
1) Flasher cancelling unit.
2) Handlebar switch reset circuit
3) Speedometer sensor circuit
b. Pull off the 6-pin connector from the flasher cancelling unit, and connect a tester (ohms x 100 range) across the white/green and the black leads on the wire harness side. Turn the speedometer shaft If the tester needle swing back and forth between 0 and co, the speedometer sensor circuit is in good condition. If not, the sensor to wire harness may be inoperative.
c. Pull the 6-pin connector from the flasher cancelling unit Check if there is continuity between the yellow/red lead on the wire harness side and the chassis.
"TURN" switch OFF: oo "TURN" switch L or R: 0 il
If the tester needle does not swing as indicated above, check the handlebar switch circuit and wire harness.
d. If no defect is found with the above three check-ups and the flasher cancelling system is still inoperative, replace the flasher cancelling unit.
e. If the signal flashes only when the handlebar switch lever is turned to L or R and it turns off immediately when the handlebar switch lever returns to center, replace the flasher cancelling unit
Sensors and Switches
Sensors and SwitchesFuel sender unit
1. Inspection
a. Remove the sender unit from the fuel tank.
b. Use a pocket tester (with ohm x 10 scale) for this check. Connect the pocket tester leads across the green lead and the black lead of the sender unit. The meter should show the following resistance at the specified fuel level. If not replace the sender unit.
Fuel sender resistance |
|
Full |
2—12Ω |
1/2 |
40Ω |
Empty |
87.5 — 102.5 Ω |
Oil level switch
1. Inspection
a. Remove the oil level switch from the engine.
b. Use a pocket tester (with ohm x 1 scale) for this check.
Connect the pocket tester lead as shown.
When the oil level switch stands up right the tester should read infinity. When the oil level switch stands up side down, the tester should read 0 ohms.
Tachometer
1. Description
This model has been equipped with an electric tachometer. This tachometer receives its impulses from one of the stator leads of the alternator.
2. Inspection
a. If the tachometer should become inoperative, the following troubleshooting steps will be useful.
1) Remove the headlight rim.
2) Turn the ignition switch to the "ON" position.
3) Inside the headlight shell disconnect the tachometer leads from the main harness.
Use a pocket tester to check and set the meter selector to the "DC 20" position.
Connect tester leads between brown and black leads from main harness. Meter should show 12 volts D. C. |
Less than 12 volts or no voltage ► |
Weak connection or open circuit between fuse and main harness |
YES ▼ |
||
Replace tachometer assembly |
Digital clock
1. Inspection
If the digital clock should become inoperative, the following troubleshooting steps will be useful.
a. Remove the headlight rim.
b. Turn the ignition switch to the "ON" position.
c. Inside the headlight shell disconnect the digital clock leads from the main harness. Use a pocket tester to check and set the meter selector to the "DC 20" position.
Connect tester leads between brown and black leads from main harness. Meter should show 12 volts D. C |
Less than 12 volts or no voltage ► |
Weak connection or open circuit between fuse and main harness |
YES ▼ |
||
Replace digital clock assembly |
2. Adjustment
This digital clock always show the time regardless of the main switch position.
To set the time:
Turn ignition "ON"
Set hour by pushing or holding the "H" switch.
Set minutes by pushing or holding the "M" switch.
NOTE: If setting the clock after the power source has been interupted (eg: disconnected battery, blown fuse) It may be necessary to first hold the "H" switch for 10 seconds; before setting the correct time.
1. Digital clock
Switches
Switches may be checked for continuity with a pocket tester on the "ohm x 1" position.
1. Main switch
Switch Position |
Wire Color | |||
R | Br | L | L/R | |
OFF | ||||
ON | ![]() |
![]() |
||
P (parking) | ![]() |
2. "ENGINE STOP" switch
Switch Position | Wire Color | |
R/W | R/W | |
RUN | ![]() |
|
OFF |
3. "LIGHTS" switch (right handlebar)
SwitchPosition | Wire Color | ||
R/Y | L | L/B | |
ON | ![]() |
||
PO | ![]() |
||
OFF |
4. Starter switch (right handlebar)
Button Position | Wire Color | |
L/W | B | |
OFF | ||
ON | ![]() |
5. "LIGHTS" (Dimmer) switch
Switch Position | Wire Color | ||
Y | L B | G | |
HI | ![]() |
||
LO | ![]() |
6. "TURN" switch (left handlebar)
Switch Position | Wire Color | ||||
Dg | Br/W | Ch | Y/R | B | |
R | ![]() |
![]() |
|||
R —N | ![]() |
||||
N — Push | |||||
L —N | ![]() |
||||
L | ![]() |
![]() |
7. "HORN" switch (left handlebar)
Switch Position | Wire Color | |
P | B | |
PUSH | ![]() |
|
OFF |
8. Passing light switch (left handlebar)
Button Position | Wire Color | |
Y | R/Y | |
OFF | ||
PUSH | ![]() |
Battery
BatteryBattery
1. Checking
If the battery shows the following defects, it should be replaced.
a. The battery voltage will not rise to a specific value or no gassing occurs in any cell even after many hours of charging.
b. Sulfation of one or more cells is indicated by the plates turning white or an accumulation of material in the bottom of the cell.
c. Specific gravity readings after a long slow charge indicate a cell to be lower than any others.
d. Warpage or buckling of plates or insulators is evident.
WARNING: Battery fluid is poisonous and dangerous, causing severe burns, etc. Contains sulfuric acid. Avoid contact with skin, eyes or clothing.
Antidote: EXTERNAL-Flush with water. INTERNAL-Drink large quantities of water or milk. Follow with milk of magnesia, beaten egg or vegetable oil. Call physician immediately.
Eyes: Flush with water for 15 minutes and get prompt medical attention. Batteries produce explosive gases. Keep sparks, flame, cigarettes, etc., away. Ventilate when charging or using in enclosed space. Always shield eyes when working near batteries. KEEP OUT OF REACH OF CHILDREN.
2. The service life of a battery is usually 2 to3 years, but lack of care as described below will shorten the life of the battery.
a. Negligence in keeping battery topped off with distilled water.
b. Battery being left discharged.
c. Over-charging with heavy charge.
d. Freezing.
e. Filling with water or sulfuric acid containing impurities.
f. Improper charging voltage or current on new battery.
3. If the motorcycle is not to be used for a long time, remove the battery and have it stored. The following instructions should be observed:
a. Recharge the battery periodically.
b. Store the battery in a cool, dry place.
c. Recharge the battery before reinstalla-tion.
Battery |
YB14L/12V, 14AH |
Electrolyte |
Specific gravity: 1.280 |
Initial charging current |
1.4 amp for 10 hours (new battery) |
Recharging current |
10 hours (or until specific gravity reaches 1.280) |
Refill fluid |
Distilled water (to maximum level line) |
Refill period |
Check once per month (or more often, required) |
Chapter 7. Specifications
Chapter 7. SpecificationsGeneral Specifications
General Specifications1 | Model Code Number | 33F | |||
2 | Frame Starting Number | 33F-000101 | |||
3 | Engine Starting Number | 33F-000101 | |||
4 a |
Dimensions: Overall Length |
2,190 mm (86.2 in) | |||
b | Overall Width | 735 mm (28.9 in) | |||
c | Overall Height | 1,240 mm (48.8 in) | |||
d | Seat Height | 790 mm (31.1 in) | |||
e f |
Wheelbase Minimum Ground Clearance |
1,480 mm (58.3 in) 150 mm ( 5.9 in) | |||
5. a. | Weight: With Oil and Full Fuel Tank |
242 kg (534 lb) | |||
6 | Minimum Turning Radius | 2,600 mm (102.4 in) | |||
7 a |
Engine: Engine Type |
D.O.H.C., air-cooled, gasoline | |||
b | Cylinder Arrangement | Forward-incline, parallel 4-cylinder | |||
c | Displacement | 853 cm3 (52.05 cu.in) | |||
d | Bore x Stroke | 67.0 x 60.5 mm (2.638 x 2.382 in) | |||
e | Compression Ratio | 9.6 : 1 | |||
f | Compression Pressure | 785 - 1,177 kPa (8.0 - 12.0 kg/cm2, 114-171 psi) | |||
g | Starting System | Electric | |||
8 | Lubrication System |
|
|||
9 | Engine Oil Type or Grade Above 15°C (60°F) Below 5°C (40°F) |
SAE 20W40 type SE motor oil SAE 10W30 type SE motor oil | |||
10. a. |
Engine Oil Capacity Periodic Oil Change |
2.5 L (2.2 Imp qt. 2.6 US qt) | |||
b | Oil Filter Replacement | 2.8 L (2.5 Imp qt, 3.0 US qt) | |||
c | Total Amount | 3.6 L (3.2 Imp qt, 3.8 US qt) | |||
11 | Final Gear Oil | ||||
a | Grade or Type | SAE 80 API "GL-4" Hypoid gear oil | |||
b | Final Gear Case Oil Amount | 0.2 L (0.18 impqt, 0.21 US qt) | |||
12 | Air Filter | Dry type element | |||
13. a. | Fuel Type | Regular gasoline | |||
b | Tank capacity | 22.0 L (4.84 Imp gal, 5.81 US gal) | |||
c | Reserve Amount | 5.0 L (1.10 Imp gal, 1.32 US gal) | |||
14 | Carburetor | ||||
a | Type | BS35 x 4 | |||
b | Manufacturer | MIKUNI | |||
15 | Spark Plug | ||||
a | Type | BPR8ES | |||
b | Manufacturer | NGK | |||
c | Gap | 0.7 ~ 0.8 mm (0.028 — 0.032 in.) | |||
16 | Clutch Type | Wet multiple disc | |||
17. | Transmission: | ||||
a b c |
Primary Reduction System Primary Reduction Ratio Secondary Reduction System |
Spur gear 97/58 (1.672) Shaft drive |
|||
d | Secondary Reduction | ||||
Transmission output Type/teeth/ratio | Spur gear, 48/37 (1.297) | ||||
Middle gear case Type/teeth/ratio | Bevel gear, 19/18 (1.055) | ||||
Final gear case Type/teeth/ratio | Bevel gear, 32/11 (2.909) | ||||
e | Transmission Type | Constant mesh, 5-speed drum shifter | |||
f | Operation | Left foot operation | |||
g | Gear Ratios | ||||
1st | 35/16 (2.187) | ||||
2nd | 30/20 (1.500) | ||||
3rd | 30/26 (1.153) | ||||
4th | 28/30 (0.933) | ||||
5th | 26/32 (0.812) | ||||
18 | Chassis: | ||||
a | Frame Type | Tubular steel double cradle | |||
b | Caster Angle | 27° | |||
c | Trail | 114 mm (4.49 in) | |||
19 a b c d |
Tire Type Tire Size (F) Tire Size (R) Manufacturer |
Tubeless 100/90 V18 120/90 V18 PIRELLI, BRIDGESTONE | |||
20 a |
Tire Pressure UP to 90 kg (198 lb) load* (F) |
(Cold pressure) 226 kPa (2.3 kg/cm2, 32 psi) |
|||
(R) | 245 kPa (2.5 kg/cm2, 36 psi) | ||||
b | 90 kg (198 lb) - 194 kg (428 lb) load* (F) | 245 kPa (2.5 kg/cm2, 36 psi) | |||
(R) | 284 kPa (2.9 kg/cm2, 42 psi) | ||||
c | High-speed Riding (F) | 245 kPa (2.5 kg/cm2, 36 psi) | |||
(R) | 284 kPa (2.9 kg/cm2, 42 psi) | ||||
*Toral weight of accessories, etc. excepting motorcycle | |||||
21. a. b. c. d. |
Brake Front Brake Type Operation Rear Brake Type Operation |
Dual Hydraulic disc Right hand Single hydraulic disc Right foot |
|||
22 | Suspension | ||||
a | Front Suspension | Telescopic fork | |||
b. | Rear Suspension | Swingarm | |||
23 | Shock Absorber | ||||
a | Front Shock Absorber | Oil damper, air and coil spring | |||
b | Rear Shock Absorber | Oil damper, gas and coil spring | |||
24. a. b. |
Wheel Travel Front Wheel Travel Rear Wheel Travel |
150 mm (5.9 in) 102 mm (4.0 in) |
|||
25. a. b. c. d. |
Electrical ignition System Generator System Battery Type or Model Battery Capacity |
Transistor ignition A.C. generator YB14L 12V 14AH |
|||
26 | Headlight Type | HALOGEN | |||
27 a b c d e f |
Bulb Wattage x Pcs Headlight Turn light Tail/Brake light Meter light License light Auxiliary light |
60W/55W x 1 27W x 4 8W/27W x 2 3.4W x 6 8W x 2 3.4W x 1 |
|||
28. a. b. c. d. |
Indicator Light Wattage x Pcs NEUTRAL HIGH BEAM TURN OIL |
3.4W x 1 3.4W x 1 3.4W x 2 3.4W x 1 |
Engine Specifications
Engine Specifications
1. a. b. |
Cylinder Head Volume |
|
31.5 - 32.3 cm3 (1.92 - 1.97 cu.in) |
||||
2. a. b. c. d. |
Cylinder |
|
|||||
3. b. c. d. |
Camshaft Cam Cap Inside Diameter |
Chain drive Center 25+0.021-0 mm (0.984+0.0008-0 in) 25-0.020-0.33 mm (0.984-0.0008-0.0013 in) 0.020 ~ 0.054 mm (0.0008 - 0.0021 in) |
|||||
e. |
Cam Dimensions |
||||||
|
Intake |
"A" |
36.75 - 36.85 mm (1.447 - 1.451 in) |
||||
Exhaust |
"A" |
36.25 — 36.35 mm (1.427 — 1.431 in) |
|||||
f. |
|
Open Open |
B.T.D.C. 38° B.B.D.C. 66° |
||||
Overlap |
a = 64° |
||||||
g. |
|
||||||
h. i. |
Cam Chain Type/Number of Links |
BUSH-CHAIN/120 |
|||||
4. b. |
Valve, Valve Seat, Valve Guide Valve Dimensions |
0.11 — 0.15 mm (0.0043 - 0.0059 in) |
|||||
|
|
|
|
"A" Head Dia. IN. |
36.1 ± 0.1 mm (1.42 ± 0.004 in) |
|
"D" Margin Thickness Limit IN. |
0.7 mm (0.028 in) |
|
c. |
Stem Outside Diameter IN. |
7-0.10-0.025mm (0.2756 -0.0004-0.0010 in) |
EX. |
7-0.25-0.040 mm (0.2756 -0.0010-0.0016 in), |
|
d |
Guide Inside Diameter IN. |
7+0.12-0. mm (0.2756 -0.0005-0.in) |
EX. |
7+0.12-0. mm (0.2756 -0.0005-0. in) |
|
e. |
Stem-to-guide Clearance IN. |
0.010 — 0.037 mm (0.0004 - 0.0015 in) |
EX. |
0.025 — 0.052 mm (0.0010 - 0.0020 in) |
|
f. |
Stem Runout Limit |
<0.03 mm (0.0012 in)> |
g- |
Valve Seat Width Standard <Limit> |
0.9 - 1.1 mm (0.035 - 0.043 in) |
5. a. |
Valve Spring Free Length |
|
b. |
Spring rate EX. |
|
Outer Spring IN. |
|
|
c. |
Compression Length (Valve Closed) |
|
d. |
Compression Force (Valve Closed) Inner Spring IN. |
|
e. |
Tilt Limit |
2.5° 1.7 mm (0.067 in) |
f. |
Direction of Winding (Top View) |
Intake |
Exhaust |
||
|
|
||||
6. a. |
Piston Piston Size/Measuring Point (A) |
67.0 mm (2.638 in)/7.8 mm (0.307 in) |
|||
|
|||||
b. c. d. |
Clearance between Piston & Cylinder |
0.03 - 0.05 mm (0.0012 - 0.0020 in) |
|||
7. |
Piston Ring |
||||
|
Top Ring |
B = 1.2-0.01-0.03 mm (0.47-0.0004-0.0012in) |
|||
|
2nd Ring |
B = 1.2-0.01-0.03 mm (0.472-0.0004-0.0012 in) |
|||
|
Oil Ring |
T = 2.8 ± 0.15 mm (0.110 ± 0.0059 in) |
|||
b. |
End Gap (Installed) Limit |
Top Ring 2nd Ring Oil Ring |
0.15 - 0.35 mm (0.0059 - 0.0138 in) |
||
c |
Side Clearance |
Top Ring 2nd Ring |
0.03 - 0.07 mm (0.0012 - 0.0028 in) |
||
d. |
Plating or Coating |
Top Ring |
Chrome plated, Ferox coating |
||
8. |
Connecting Rod |
0.016 - 0.040 mm (0.0006 - 0.0016 in) |
9. a. b. c. d. e. |
Crankshaft
Assembly Width "B" Deflection Limit "C" Journal Oil Clearance |
|
|
f. |
Color Code - Corresponding Size Blue |
|
|
|
Black |
1.5+0.002-0.002mm(0.0591+0.00008-0.00008in) |
|
Brown |
1.5-0.002-0.006mm(0.0591-0.00008-0.00024in) |
||
Green |
1.5-0.006-0.010mm(0.0591-0.00024-0.00039in) |
||
Yellow |
1.5-0.010-0.014mm(0.0591-0.00039-0.00055in) |
||
10. a. b. c. d. e. g i. j- |
Clutch Clutch Plate Thickness/Quantity Clutch Spring Free Length/Quantity Primary Reduction Gear Backlash Tolerance |
3.0 ± 0.1 mm (0.12 ± 0.004 in)/8 2.0 ± 0.1 mm (0.080 ± 0.004 in)/7 44.0 mm (1.73 in)/5 116 87 - 93 25 — 31 |
|
11. a. |
Transmission |
|
|
12 |
Shifter |
|
|
13. a. b. c. d. |
Carburetor |
|
|
e. f. g h. i. j- k. I. m. n. o. P- q- |
Main Jet Main Air Jet Jet Needle Needle Jet Throttle Valve Pilot Jet Pilot Air Jet Pilot Screw (turns out) Pilot Outlet Size Starter Jet Valve Seat Size Fuel Level Float Height |
(MJ.) (M.A.J.) (J.N.) (N.J.) (Th.V.) (P.J.) (P.A.J.) (P.S.) (P.O.) (G.S.) (V.S.) (F.L) (F.H.) |
#102.5 #45 4HZ26-3 Y-0 (#318) 135 #40 #160 Pre-set 2 turns 00.8 #32.5 Φ2.0 5 ± 1 mm (0.20 ± 0.04 in) 22.3 ± 0.5 mm (0.9 ± 0.02 in) |
r. s. |
Engine Idling Speed Vacuum Pressure at Idling Speed |
1,100 ± 50 r/min 225 - 235 mmHg (8.85 — 9.25 inHg) |
14. g- |
Lubrication System: Lubrication Diagram |
Paper filter |
15. |
Middle Gear Backlash |
0.1 - 0.2 mm (0.004 ~~ 0-008 in) |
16. |
Final Gear Backlash |
0.1 — 0.2 mm (0.004 - 0.008 in) |
17. |
Crankcase Tightening Sequence |
|
LOWER CASE |
UPPER CASE |
|
|
|
|
Tightening Torque: 8 mm bolt: 24 Nm (2.4 mkg. 1 7 ft-lb) 6 mm bolt: 12 Nm (1.2 mkg, 8.7 ft-lb) |
18. |
Tightening Torque |
|||||||
Part to be tightened |
Part name |
Thread size |
Q'ty |
Tightening torque |
Remarks |
|||
Nm |
mkg |
ft lb |
||||||
ENGINE: |
||||||||
Camshaft cap |
Bolt |
M6x1.0 |
24 |
10 1.0 7.2 |
Tighten in stages |
|||
Cam chain (Front) (Rear) |
Stud bolt Nut Stud bolt Nut |
M6x1.0 |
2 |
5 0. 5 3.6 10 1.0 7.2 |
Apply oil Apply oil |
|||
Exhaust pipe |
Stud bolt |
M6x1.0 |
8 |
8 0.8 5.8 |
Apply oil |
|||
Oil passage blind plug |
Screw |
M6x1.0 |
1 |
7 0.7 5.1 |
||||
YICS passage |
Stud bolt |
M8x1.25 |
2 2 2 |
15 1.5 11 |
Apply oil |
|||
Spark plug |
— |
M14X1.25 |
4 |
20 2.0 14 |
||||
Cylinder head |
Nut |
M10x1.25 |
12 |
32 3.2 23 |
Apply oil |
|||
Cylinder head cover |
Bolt |
M6x1.0 |
8 |
10 1.0 7.2 |
||||
Cam chain (Cylinder-Front) |
Stud bolt Nut |
M8x1.25 |
1 1 |
8 0.8 5.8 |
Apply oil |
|||
Connecting rod |
Nut |
M8x0.75 |
8 |
38 3.8 27 |
Apply Molybedenum disulfide grease |
|||
Cam sprocket |
Bolt |
M7x1.0 |
4 |
20 2.0 14 |
||||
Cam chain tensioner |
Bolt |
M6x1.0 |
2 |
10 1.0 7.2 |
||||
Cam chain tensioner guide |
Bolt |
M8x1.25 |
1 |
3 0.3 2.2 |
||||
Oil Pump cover |
Screw |
M6x1.0 |
4 |
7 0.7 5.1 |
||||
Strainer housing |
Screw |
M6x1.0 |
3 |
7 0.7 5.1 |
||||
Oil pump |
Bolt |
M6x1.0 |
3 |
12 1.2 8.7 |
||||
Oil filter |
Union bolt |
M20x1.5 |
1 |
15 1.5 11 |
||||
Engine drain bolt |
Bolt |
M14x1.5 |
1 |
43 4.3 31 |
||||
Strainer cover |
Bolt |
M6x1.0 |
13 |
12 1.2 8.7 |
||||
Oil pump sprocket |
Bolt |
M6x1.0 |
1 |
12 1.2 8.7 |
||||
Buffle plate |
Screw |
M6x1.0 |
3 |
7 0.7 5.1 |
||||
Oil cooler adapter plate |
Union bolt |
M20x1.5 |
1 |
50 5.0 36 |
Part to be tightened |
Part name |
Thread size |
Q'ty |
Tightening torque |
Remarks |
||
Nm |
mkg |
ft-lb |
|||||
Oil cooler hose and adapter |
Bolt |
M6x1.0 |
4 |
12 |
1.2 |
8.7 |
|
Oil hose |
Bolt |
M6x1.0 |
1 |
12 |
1.2 |
8.7 |
|
Oil cooler |
Bolt |
M6x1.0 |
3 |
10 |
1.0 |
7.2 |
|
Oil cooler hose clamp |
Nut |
M8x1.25 |
1 |
10 |
1.0 |
7.2 |
|
Carburetor joint |
Bolt |
M6x1.0 |
8 |
12 |
1.2 |
8.7 |
|
Air filter case cover |
Screw |
M6xt.O |
4 |
5 |
0.5 |
3.6 |
|
Air filter case and frame |
Bolt |
M6x1.0 |
3 |
5 |
0.5 |
3.6 |
|
Exhaust pipe joint band |
Bolt |
M8x1.25 |
6 |
20 |
2.0 |
14 |
|
Exhaust pipe ring nut |
Nut |
M6x1.0 |
8 |
10 |
1.0 |
7.2 |
|
Exhaust pipe and frame |
Bolt |
M1 0x1.25 |
2 |
25 |
2.5 |
18 |
|
Cylinder |
Stud bolt Bolt |
M10x1.25 M10X1.25 |
8 4 |
20 20 |
2.0 2.0 |
14 14 |
|
Crankcase |
Bolt Bolt |
M8x1.25 M6x1-0 |
19 19 |
24 12 |
2.4 1.2 |
17 8.7 |
|
Bearing plate stopper |
Screw |
M8x1.25 |
4 |
25 |
2.5 |
18 |
|
Breaker cover |
Screw |
M6x1.0 |
8 |
8 |
0.8 |
5.8 |
|
Generator cover . |
Bolt |
M6x1.0 |
3 |
12 |
1.2 |
8.7 |
|
Generator housing bearing |
Screw |
M6x1.0 |
3 |
10 |
1.0 |
7.2 |
|
Change cover |
Bolt |
M6x1.0 |
10 |
12 |
1.2 |
8.7 |
|
Drive shaft housing bearing |
Bolt |
M6x1.0 |
3 |
12 |
1.2 |
8.7 |
|
Clutch cover |
Bolt |
M6x1.0 |
10 |
12 |
1.2 |
8.7 |
|
Clutch cable holder |
Bolt |
M6x1.0 |
2 |
12 |
1.2 |
8.7 |
|
Middle drain bolt |
Bolt |
M8x1.25 |
1 |
16 |
1.6 |
11 |
|
Breather pipe 1 |
Screw |
M6x1.0 |
3 |
7 |
0.7 |
5.1 |
|
Breather pipe 2 |
Screw |
M6x1.0 |
4 |
7 |
0.7 |
5.1 |
|
Main gallary blind plug |
Plug |
M20X1.5 |
2 |
12 |
1.2 |
8.7 |
Apply oil |
Stopper plate |
Bolt |
M6x1.0 |
1 |
10 |
1.0 |
7.2 |
|
Clutch starter outer |
Bolt |
M8x1.25 |
3 |
25 |
2.5 |
18 |
|
Upper guide |
Bolt |
M6x1.0 |
3 |
10 |
1.0 |
7.2 |
|
Clutch pressure plate |
Bolt |
M6x1.0 |
5 |
8 |
0.8 |
5.8 |
|
Clutch boss |
Nut |
M20X1.0 |
1 |
70 |
7.0 |
50 |
|
Drive shaft bearing |
Nut |
M34x1.0 |
1 |
110 |
11.0 |
80 |
Part to be tightened |
Part name |
Thread size |
Q'ty |
Tightening torque |
Remarks |
||
Nm |
mkg |
ft ib |
|||||
Driven shaft bearing |
Nut |
M65x1.5 |
1 |
110 |
11.0 |
80 |
|
Middle gear flange |
Nut |
M14x1.5 |
1 |
90 |
9.0 |
65 |
|
Housing bearing |
Bolt |
M8x1.25 |
4 |
25 |
2.5 |
18 |
|
Stopper plate |
Screw Bolt |
M6x1.0 M6x1.0 |
1 1 |
7 8 |
0.7 0.8 |
5.1 5.8 |
|
Change pedal |
Bolt |
M6x1.0 |
1 |
10 |
1.0 |
7.2 |
|
Change pedal link |
Nut |
M6x1.0 |
2 |
10 |
1.0 |
7.2 |
|
A.C. Generator |
Bolt |
M10x1.25 |
1 |
55 |
5.5 |
40 |
|
Pick-up coil base |
Screw |
M6x1.0 |
2 |
8 |
0.8 |
5.8 |
|
Rotor |
Bolt |
M8x1.25 |
1 |
24 |
2.4 |
17 |
|
Brush |
Screw |
M6x1.0 |
2 |
8 |
0.8 |
5.8 |
|
Timing plate |
Screw |
M6x1.0 |
1 |
8 |
0.8 |
5.8 |
|
Starter motor |
Bolt |
M6x1.0 |
2 |
7 |
0.7 |
5.1 |
|
Oil level switch |
Bolt |
M6x1.0 |
2 |
7 |
0.7 |
5.1 |
|
Drive shaft |
U Nut |
M14x1.5 |
1 |
110 |
11.0 |
80 |
|
Bearing cap |
Bolt Nut |
M10x1.25 M8x1.25 |
2 6 |
23 23 |
2.3 2.3 |
17 17 |
|
Oil mount screw |
Plug |
M14x1.5 |
1 |
23 |
2.3 |
17 |
|
Oil drain screw |
Plug |
M14x1.5 |
1 |
23 |
2.3 |
17 |
|
Bearing retainer |
— |
M65x1.5 |
1 |
110 |
11.0 |
80 |
|
Final gear case |
Stud bolt Stud bolt |
M10x1.25 M8x1.25 |
4 6 |
17 9 |
1.7 0.9 |
12 6.5 |
Chassis Specifications
Chassis Specifications
1 |
Steering System Lock-to-iock Angle |
|
Taper roller bearing KOYO 32005 |
2.
d. f. g |
Front Suspension
Oil Grade Enclosed Air Pressure |
K1 K2
|
150 mm (5.91 in) No |
3. d. |
Rear Suspension Optional Spring |
K1 K2 |
No. |
4. |
Rear Arm |
|
|
5. b. c. |
Wheel |
Cast wheel <2.0 mm (0.08 in) > |
|
6. b. |
Disc Brake Outside Dia. x Thickness |
Front |
Dual disc |
c. |
Pad Thickness Limit |
<0.5 mm (0.020 in) > |
d. e. f. |
Master Cylinder Inside Dia. Caliper Cylinder Inside Dia. Brake Fluid Type |
Front |
15.87 mm (0.62 in) |
7. |
Brake Lever & Brake Pedal |
|
|
8. |
Clutch Lever Free Play |
2 — 3 mm (0.08 -0.12 in) |
Recommended combinations of the front fork and rear shock absorber settings. Use this table as guidance to meet specific riding and motorcycle load conditions.
Front fork |
Rear shock absorber |
Loading condition |
|||||
Air pressure |
Spring seat |
Damping adjuster turns out* |
Solo rider |
With passenger |
With accessory equipments |
With accessory equipments and passenger |
|
1 |
39.2 — 78.5 kPa (0.4 - 0.8 kg/cm2, 5.7 - 11.4 psi) |
|
6 |
O |
|||
2 |
39.2 — 78.5 kPa (0.4 - 0.8 kg/cm2, 5.7 - 11.4 psi) |
|
4 |
O |
|||
3 |
58.8 — 98.1 kPa (0.6 - 1.0 kg/cm2, 8.5 - 14.2 psi) |
|
4 |
O |
|||
4 |
78.5 ~~ 118 kPa (0.8 - 1.2 kg/cm2, 11.4 - 17.1 psi) |
|
3 |
O |
Each numeral shows the damping value which can be set when the pointer is aligned with the individual slit in the spring seat. The damping adjuster may be further turned for a softer or harder damping; in each of the above settings, itis recommended that the damping be adjusted by one (1) or two (2) clicks on the softer side and one (1) click on the harder side.
1 9. Tightening Torque |
|||||
Parts to be tightened |
Thread size |
Tightening torque |
Remarks |
||
Nm |
nrkg |
ft-lb |
|||
CHASSIS: |
|||||
Front wheel axle and nut |
M14x 1.5 |
78 |
7.8 |
50 |
|
Front fender and front fork |
M6 x 1.0 |
9 |
0.9 |
6.5 |
|
Handle crown and inner tube |
M8 x 1.25 |
20 |
2.0 |
14 |
|
Handle crown and steering shaft |
M25 x 1.0 |
110 |
11.0 |
80 |
|
Under bracket and inner tube |
M8 x 1.25 |
23 |
2.3 |
17 |
|
Front fork cylinder and outer tube |
M8 x 1.25 |
23 |
2.3 |
17 |
|
Brake caliper (Front and rear) |
M10 x 1.25 |
35 |
3.5 |
25 |
|
Front fork and axle holder |
M8 x 1.25 |
20 |
2.0 |
14 |
|
Anti-nose dive and front fork |
M5 x 0.8 |
5 |
0.5 |
3.6 |
|
Brake disc and wheel hub |
M8x 1.25 |
20 |
2.0 |
14 |
|
Brake caliper and bleed screw (Front and rear) |
M8 x 1.25 |
6 |
0.6 |
4.3 |
|
Anti-nose dive and bleed screw |
M8 x 1.25 |
6 |
0.6 |
4.3 |
|
Union bolt (Front and rear) |
M10 x 1.25 |
26 |
2.6 |
19 |
|
Brake pipe and joint |
M10x 1.0 |
19 |
1.9 |
13 |
|
Master cylinder and master cylinder cap |
M5 x 0.8 |
2 |
0.2 |
1.4 |
|
Handle crown and handlebar |
M12 x 1.25 |
93 |
9.3 |
67 |
|
Handlebar and grip bar |
M10x 1.25 |
50 |
5.0 |
36 |
|
Grip bar and grip end |
M18 x 1.5 |
26 |
2.6 |
19 |
|
Front brake master cylinder and master cylinder bracket |
M6 x 1.0 |
9 |
0.9 |
6.5 |
|
Fuel sender unit and fuel tank |
M5 x 0.8 |
4 |
0.4 |
2.9 |
|
Engine mounting bolt Front, upper |
M10 x 1.25 |
42 |
4.2 |
30 |
|
Engine stay and frame |
M8x 1.25 |
20 |
2.0 |
14 |
|
Pivot shaft and rear arm |
M22 x 1.5 |
6 |
0.6 |
4.3 |
|
Pivot shaft and lock nut |
M22 x 1.5 |
100 |
10.0 |
72 |
|
Rear shock absorber and frame |
M10 x 1.25 |
30 |
3.0 |
22 |
|
Rear shock absorber and rear arm |
M10x 1.25 |
30 |
3.0 |
22 |
|
Rear shock absorber and housing gear |
M10 x 1.25 |
30 |
3.0 |
22 |
|
Rear wheel axle and nut |
M14x 1.5 |
105 |
10.5 |
75 |
Parts to be tightened |
Thread size |
Tightening torque |
Remarks |
||
Nm |
rrvkg |
ft-lb |
|||
Middle gear flange and cross joint |
M8 x 1.25 |
44 |
4.4 |
32 |
|
Frame and muffler bracket |
M10 x 1.25 |
42 |
4.2 |
30 |
|
Rear footrest and muffler bracket |
M10 x 1.25 |
42 |
4.2 |
30 |
|
Rear brake master cylinder and frame |
M8 x 1.25 |
20 |
2.0 |
14 |
|
Compression bar and rear arm |
M10 x 1.25 |
30 |
3.0 |
22 |
|
Compression bar and caliper bracket |
M10 x 1.25 |
30 |
3.0 |
22 |
|
Rear stay and frame |
M8 x 1.25 |
23 |
2.3 |
17 |
Electrical Specifications
Electrical Specifications
1. |
Voltage |
12V |
||
2. |
Ignition System |
5°/1,050 r/min |
||
|
||||
c. |
Advancer Type |
Electrical type |
||
3. a. b. |
T.C.I. Pick up Coil Resistance (Color) T.C.L Unit-Model/Manufacturer |
120 Ω ± 20% at 20°C (68°F) (O-B, Gy-B) TID14-19/HITACHI |
||
4. a. b. c. d. |
Ignition Coil Primary Winding Resistance |
CM12-20/HITACHI 2.7Ω ± 10%at20°C (68°F) |
||
5. |
Charging System |
A.C. Generator |
||
|
||||
d. e. f. |
Field (Inner) Coil Resistance (Color) |
4.0 n ± 10% at 20°C (68°F) (G-Br) |
6. |
Voltage Regulator |
Field control type |
7. |
Rectifier |
SH233-1 2/SHINDENGEN |
8. |
Battery |
12V 14AH |
9. e. f. g h. |
Electric Starter System Commutator Dia. Starter Switch Manufacturer |
Constant mesh type |
10. |
Horn |
Plane type/2 |
11. |
Flasher Relay |
Condenser type |
12. |
Self-Cancelling Unit |
1A0/MATSUSHITA |
13. |
Oil Level Switch |
4H7/NIPPONDENSO |
14. |
Fuel Gauge |
31A/NIPPON SEIKI 2 - 12Ω at 20°C (68°F) |
15. |
Starting-Circuit Cut-Off Relay |
12R/0MR0N |
16.
|
Circuit Breaker |
Fuse 30A/1 |
General Torque Specifications
General Torque SpecificationsThis chart specifies torque for standard fasteners with standard I.S.O. pitch threads. Torque specifications for special components or assemblies are included in the applicable sections of this book. To avoid warpage, tighten multi-fastener assemblies in a crisscross fashion, in progressive stages, until full torque is reached. Unless otherwise specified, torque specifications call for clean, dry threads. Components should be at room temperature.
A (Nut) |
B (Bolt) |
General torque specifications |
||
Nm |
m-kg |
ft lb |
||
10 mm |
6 mm |
6 |
0.6 |
4.5 |
12 mm |
8 mm |
15 |
1.5 |
11 |
14 mm |
10 mm |
30 |
3.0 |
22 |
17 mm |
12 mm |
55 |
5.5 |
40 |
19 mm |
14 mm |
85 |
8.5 |
61 |
22 mm |
16 mm |
130 |
13.0 |
94 |
A: Distance across flats B: Outside thread diameter
DEFINITION OF UNITS
Unit |
Read |
Definition |
Mesure |
mm |
Millimeter |
10-3 meter |
Length |
kg |
kilogram |
103 gram |
Weight |
N |
Newton |
1 kg x m/sec2 |
Force |
Nm |
Newton meter |
N x m |
Torque |
Pa |
Pascal |
N/m2 |
Pressure |
L |
Liter |
Volume or Capacity |
|
r/min |
Rotation per minute |
Engine Speec |
Chapter 8. Exploded Diagrams
Chapter 8. Exploded DiagramsEngine Components
Engine ComponentsCYLINDER HEAD
VALVE
CAM CHAIN
CRANKSHAFT/PISTON
. WHEN INSTALLING THE CONNECTING ROD. BE SURE THAT THE SECURING NUTS ARE ON TOP.
OIL COOLER
Transmission Components
Transmission ComponentsCLUTCH
TRANSMISSION
MIDDLE GEAR/DAMPER
Final Drive
Final DriveFINAL GEAR/DRIVE SHAFT
Wheels and Brakes
Wheels and BrakesFRONT MASTER CYLINDER
REAR MASTER CYLINDER
FRONT BRAKE CALIPER
REAR BRAKE CALIPER
FRONT WHEEL
REAR WHEEL
Suspension Components
Suspension ComponentsFRONT FORK
REAR SHOCK ABSORBER
SWING ARM
• APPLY LITHIUM-BASE GREASE
Lubrication Diagrams
Lubrication DiagramsLUBRICATION DIAGRAMS
Cable Routing
Cable RoutingCABLE ROUTING
*1: Pass front brake switch lead and right handlebar switch lead behind air hose.
*2: Pass brake hose and throttle cable between air hose and meter stay.
*3: Pass clutch cable, clutch switch lead, left handlebar switch lead and starter cable behind air hose.
*4: Pass speedometer cable outside meter stay, in front of fairing fitting stay, and outside brake hose.
*5: Pass horn leads in front of brake joint.
*6: Pass front flasher light leads between horn and brake joint.
*7: Pass wire harness between under bracket and wire harness stay.
*1: Fasten ground lead together left ignition coil.
*2: Pass clutch cable between air cleaner joint #3 and #4
Electrical
ElectricalSPEEDOMETER/TACHOMETER
ELECTRICAL 1
ELECTRICAL 2
1 | Diode Block | 6 | Starting Circuit cut-off Relay |
2 | Horn | 7 | Rectifier/Regulator |
3 | Fuel Meter Sender Unit | 8 | Flasher Cancelling Unit (except Germany) |
4 | Flasher Relay | 9 | Clutch Switch |
5 | Starter Relay |
Fuel Meter Sender Unit Resistance
Full | 2Ω~12Ω at 20°C (68°F) |
Empty | 87.5Ω - 102.5Ω at 20°C (68°F) |
WIRING DIAGRAM
1 | Main switch | 18 | Ignition coil | 35 | Auxilary light |
2 | Handlebar switch (Right) | 19 | Ignitor | 36 | Headlight |
3 | "LIGHT" switch | 20 | Pick-up coil | 37 | Meter assembly |
4 | "ENGINE STOP" switch | 21 | Neutral switch | 38 | Meter light |
5 | "START" switch | 22 | Rear brake switch | 39 | "TURN" indicator light |
6 | Front brake switch | 23 | Flasher relay | 40 | Fuel meter |
7 | Fuel sender | 24 | Cancelling unit | 41 | Tachometer |
8 | Fuse box | 25 | Rectifier with regulator | 42 | Over revolution switch |
9 | Diode | 26 | A C Generator | 43 | Reed switch |
10 | Starting-circuit cut-off relay | 27 | Oil level switch | 44 | Digital clock |
11 | Rear flasher light (Right) | 28 | Clutch switch | 45 | "NEUTRAL" indicator light |
12 | Rear flasher light (Left) | 29 | Handebar switch (Left) | 46 | "OIL" indicator light |
13 | Tail brake light | 30 | "TURN" switch | 47 | "HIGH BEAM" indicator light |
14 | Battery | 31 | 'HORN' switch | 48 | Horn |
15 | Starter relay | 32 | Passing light switch "PASS" | 49 | Front flasher light (Right) |
16 | Starter motor | 33 | "LIGHTS" (Dimmer) switch | ||
17 | Spark plug | 34 | Front flasher light (Left) |
COLOR CODE
8r | Brown | Y | Yellow | L | Blue | R/W | Red/White | Y/B | Yellow/Black | Y/R | Yellow/Red | E | Ground |
R | Red | Dg | Dark Green | P | Pink | L/W | Blue/White | Br/W | Brown/White | R/W | Red/White | B/R | Black/Red |
W | White | Ch | Chocolate | 0 | Orange | L/B | Blue/Red | Y/G | Yellow/Green | L/R | Blue/Red | Gy | Gray |
B | Black | Sb | Sky Blue | G | Green | R/Y | Red/Yellow | W/G | White/Green | G/Y | Green/Yellow | B/Y | Black/Yellow |